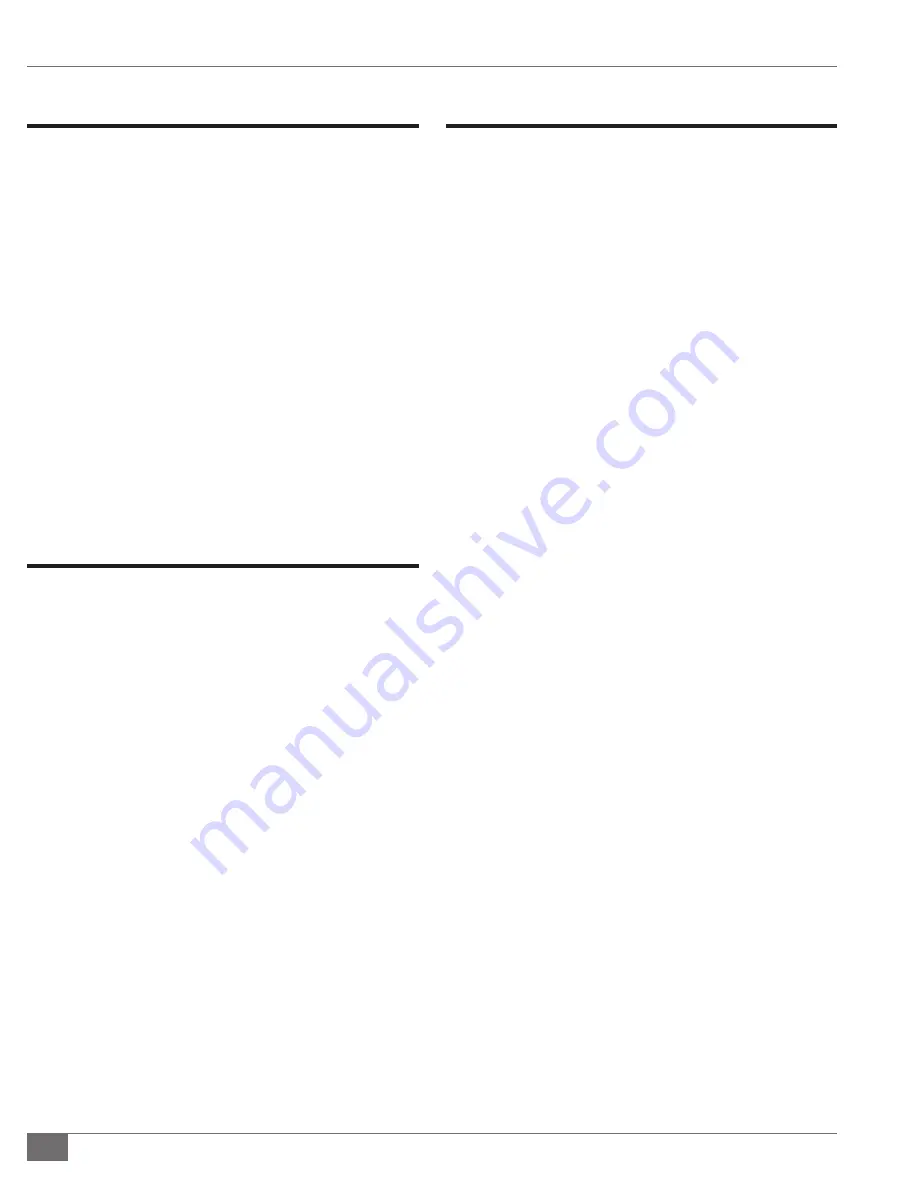
© Fulton Group N.A., Inc. 2022
INSTALLATION
VSRT-IOM-2022-0728
SECTION 2
2-42
Insulation
NOTE:
It is recommended that for inspection and
maintenance, pumps, flanges, valves and fittings are left
uninsulated but suitably shielded for safety.
Adhere to the following:
1. The boiler is insulated at the factory. No additional
insulation on the boiler pressure vessel is required.
Adding insulation may damage the boiler and its
components.
2. Feedwater tanks, surge tanks and deaerators should
be insulated. Insulation should be chosen with care
such that the fluid in the tanks does not exceed the
maximum operating temperature of the pump.
3. Blow
off vessels should
not
be insulated.
4. Equipment should be insulated with material suitable
for the application and temperatures expected.
System Interfaces
Refer to System Diagram
(Figur
e 25)
.
Feedwater Tank
Where an atmospheric feedwater tank is to be fitted, ad-
here to the following:
1. Vent to a safe location.
2. Boiler feed tank shall have a capacity sufficient to
satisfy boiler consumption as well as maintain proper
feedwater tank temperature. Capacity should provide
a minimum of 10 minutes of storage. Boiler pump is
to provide a capacity of 2.5 times the evaporation rate
for on/off pumps and 1.5 times the evaporation rate
for continuous running pumps. The discharge pressure
of the pump must be 3% over the boiler safety valve
setting and include the necessary additional pressure to
overcome piping losses.
3. See
Feedwater Instruction Manuals
for detailed
instructions.
The Feed Water Piping
Where the feed water piping is to be fitted, adhere to the
following:
1. Size makeup water piping adequately to provide proper
water supply. Do not reduce feedwater piping smaller
than supplied line size. Depending on installation,
feedwater piping may need to be larger to minimize
pressure drop of feedwater piping.
2. Do not use the feed water pump as a support for the
feed water piping. This could add undue strain to the
pump head. Use proper piping supports as necessary to
support feed water piping.
3. Do not use stainless steel within the Boiler External
Piping (BEP) boundary.
4. Ensure all piping is done in compliance with all
applicable codes.
5. See Feedwater Instruction Manuals for detailed
instructions.
Blowdown Tank
Where a blowdown tank is to be fitted, adhere to the
following:
1. Vent to a safe location.
2. Have a capacity sufficient to satisfy boiler blowoff, as
well as maintain proper drain temperature.
3. Ensure compliance with all applicable codes when
determining connection piping between the boiler and
the blowdown tank.
4. Do not downsize vent pipe (this may cause pressure
build up in the blowdown tank).
5. Ensure means to control discharge drain temperature
below 140°F or maximum allowable temperatures
allowed by local jurisdiction.
6. Do not insulate the blowdown tank.
Содержание VSRT Series
Страница 2: ......
Страница 84: ... FultonGroupN A 2022 OPERATION VSRT IOM 2022 0728 SECTION3 3 20 THIS PAGE LEFT INTENTIONALLY BLANK ...
Страница 102: ... FultonGroupN A Inc 2022 MAINTENANCE TROUBLESHOOTING VSRT IOM 2022 0728 SECTION4 4 18 PAGE LEFT INTENTIONALLY BLANK ...
Страница 115: ...Questions PleaseContactYourLocalManufacturer sRepresentative SECTION5 VSRT IOM 2022 0728 SERVICEDOCUMENTS 5 13 NOTES ...
Страница 116: ... FultonGroupN A 2022 SERVICEDOCUMENTS VSRT IOM 2022 0728 SECTION5 5 14 NOTES ...
Страница 117: ...Questions PleaseContactYourLocalManufacturer sRepresentative SECTION5 VSRT IOM 2022 0728 SERVICEDOCUMENTS 5 15 NOTES ...