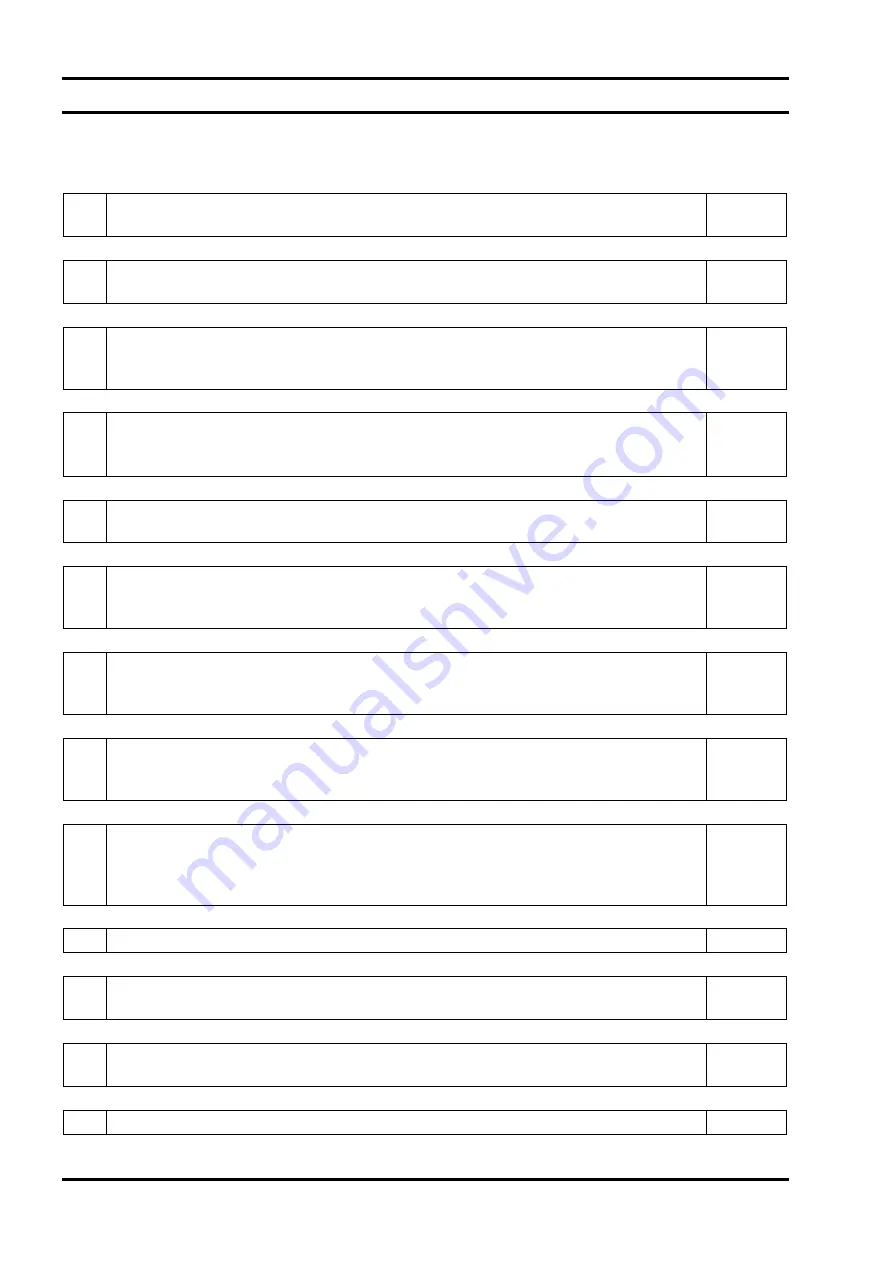
- 14 -
INZ-TN1ZSS-E
4.5 Installation procedure
Install equipments, referring to the following procedure.
Item Page
(1) Check that the installation location for each equipment satisfies the contents in “4.1
↓
(2) Check that the installation location for the receiver unit and the transmitter unit satisfies
the contents in “4.2 Mounting dimensions of receiver unit and transmitter unit”.
P.12
↓
(3) Check that the companion flange which meets the contents in “4.3 Mounting range of
companion flange” is prepared at the installation locations for the receiver unit and the
transmitter unit.
P.13
↓
(4) Check that the installation location for the receiver unit and the transmitter unit has two
types of
φ
8/6 tube (for the receiver/transmitter unit) for air purge connection, provided
with the flow meter (regulator permitted).
P.18
↓
(5) Check that the power supply of rated voltage 100 to 240V AC ± 10%, and rated fre-
quency 50/60Hz is prepared at the installation location for the control unit.
↓
(6) Perform zero calibration, referring to “6.1 Zero calibration”. Note that, if the power is
“OFF” for a long time, about 90 minutes of warm up time is necessary after power ON
to perform zero calibration.
↓
(7) Record the light quantity value when zero calibration is performed (output value of the
probe adjusting the received light quantity (BNC receptor)), referring to “4.6 Checking
received light quantity”.
P.15
↓
(8) Perform span calibration referring to “6.2 Span calibration”. Pay attention to the position
and the length of the exhaust tube not to aspirate span gas. Feed zero gas after span cali-
bration.
↓
(9) Mount the angle adjustment unit to the companion flange, and adjust the angle using an
optical axis adjusting tool (laser pointer, etc), referring to “4.7.2 Adjustment procedure”.
If the furnace is operated, be sure to adjust the angle in a state where air purge is per-
formed.
↓
(10) Perform the piping connection to purge air, referring to “4.8 Piping system diagram”.
P.18
↓
(11) Mount the receiver box and the transmitter box to the angle adjustment unit, referring to
“4.9 Assembly of receiver unit and transmitter unit”.
P.18
↓
(12) Connect the Receiver/Transmitter cable and the cable between control unit and receiver
unit, referring to “4.10 Wiring connection”.
↓
(13) Turn ON the control unit.
↓
Содержание FE ZSS
Страница 1: ...Instruction Manual INZ TN1ZSS E CROSS STACK LASER GAS ANALYZER TYPE ZSS...
Страница 13: ...INZ TN1ZSS E 3...