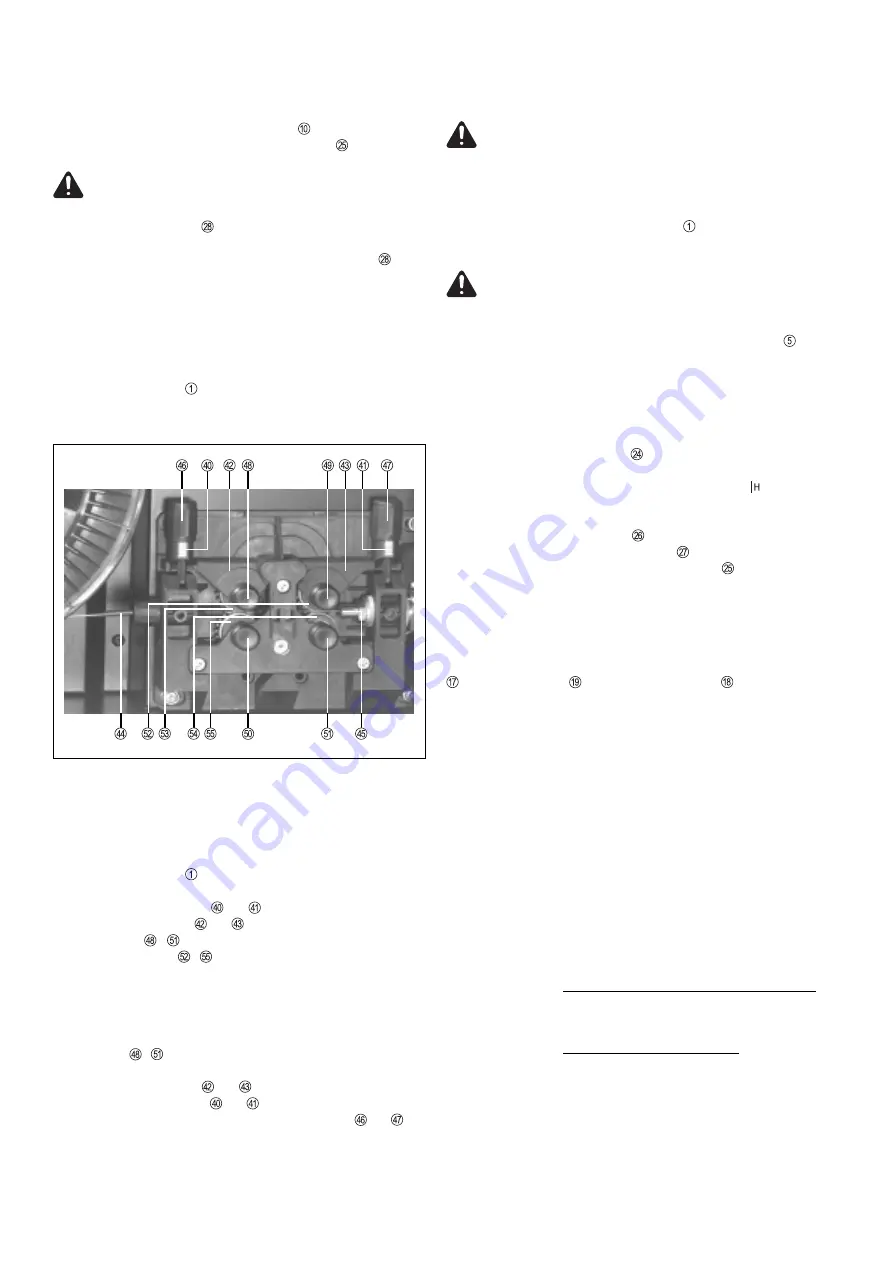
40
MIG/MAG WELDING
Warning!
Before starting up for the first time, read the sections headed
Safety rules and Starting to use the power source.
- Plug the earth cable into the current socket and latch it in firmly.
- Connect the other end of the earth cable to the workpiece
- Plug the machine into the mains
- Switch the machine on at the mains switch
- Mains control lamp lights up
Warning!
On water-cooled machines, the water-flow must be
checked at regular intervals while the machine is in operation - you
must be able to see that the coolant is flowing back properly.
- Pre-select the welding program with the program selector switch (No
Program indicator must not light up or start flashing)
N.B.!
All the programs were welded with a standard torch (apart from T.I.M.E.
programs). When standard programs are welded with a T.I.M.E. torch, this
may lead to changes in the welding properties.
- Shift the operating-mode switch on the wirefeeder into the desired
position
- Connect the remote-control unit to the remote-control socket (for pulsed-
arc welding, connect up the TR 34 T.I.M.E. remote-control unit and set
the operating-mode switch on the TR 34 T.I.M.E. to Pulsed-arc welding)
- Set the arc-length correction dial to 0
- Set the droplet-detachment correction dial to 0
- Set the required amperage on the welding power dial (command value
is shown on the amperage indicator)
- Open the gas-cylinder valve
- Set the gas-flow rate
- Press the torch trigger and start welding
N.B.!
In some cases, it may be necessary to correct the gas pre-flow time
or gas post-flow time and/or the soft-start speed .
ADJUSTMENT GUIDELINES FOR THE T.I.M.E.
PROCESS
Thanks to the single-dial operation of the T.I.M.E. Synergic, it is only
necessary to set the appropriate wirefeed speed ; the correct welding voltage
is then set automatically. Corrections are only then needed to the arc length.
Calculating the deposition rate
This formula only holds good for a wire diameter of 1.2 mm and for unalloyed
and low-alloy steel wires. It takes no account of spattering losses (typically
1 - 2 %).
e.g. wirefeed speed = 20m/min
Wirefeed speed [m/min] x 60 x 8.9
Deposition rate [kg/h] =
1000
20 m/min x 60 x 8.9
Deposition rate [kg/h] =
1000
= 10.68 kg/h
- Shift the selector switch for digital indications into the m/min position
- Set a value of ~ 5 m/min on the welding power dial
Warning!
During the wire-infeed operation, hold the welding torch
facing away from your body.
- Press the wire-inch button until the wire electrode protrudes out of the
end of the torch
- To end the wire-infeed operation, release the wire-inch button
N.B.!
The wire spool must not continue to unreel after you release the torch
trigger. Re-adjust the brake if necessary.
- Screw in the contact tube
- Fit the gas nozzle
- Close the wire-spool cover
- Shift the mains switch to the O position
CHANGING THE FEED ROLLERS
In order to achieve satisfactory wire travel, the feed rollers must be suitable
for the diameter and alloy of the wire to be welded.
- Shift the mains switch to the O position
- Open the wire-spool cover
- Pivot the clamping devices and forwards
- Pull the pressure levers and upwards
- Pull out axles -
- Remove feed rollers -
- Insert new feed rollers
N.B.!
Insert the feed rollers in such a way that you can still see and read the
designation for the wire diameter.
- Push axles - back in again - the anti-twist lock of each axle must
latch into place
- Push the pressure levers and downwards
- Pivot the clamping devices and into the vertical position
- Set the contact pressure by means of the clamping nuts and
- Close the wire-spool cover
Fig.16
4-roller drive
Содержание T.I.M.E. SYNERGIC
Страница 2: ......
Страница 27: ...OPERATING INSTRUCTIONS...
Страница 28: ......
Страница 53: ...MODE D EMPLOI...
Страница 54: ......
Страница 79: ...ERSATZTEILLISTE SPARE PARTS LIST LISTE DE PI CES DE RECHANGE...
Страница 80: ......