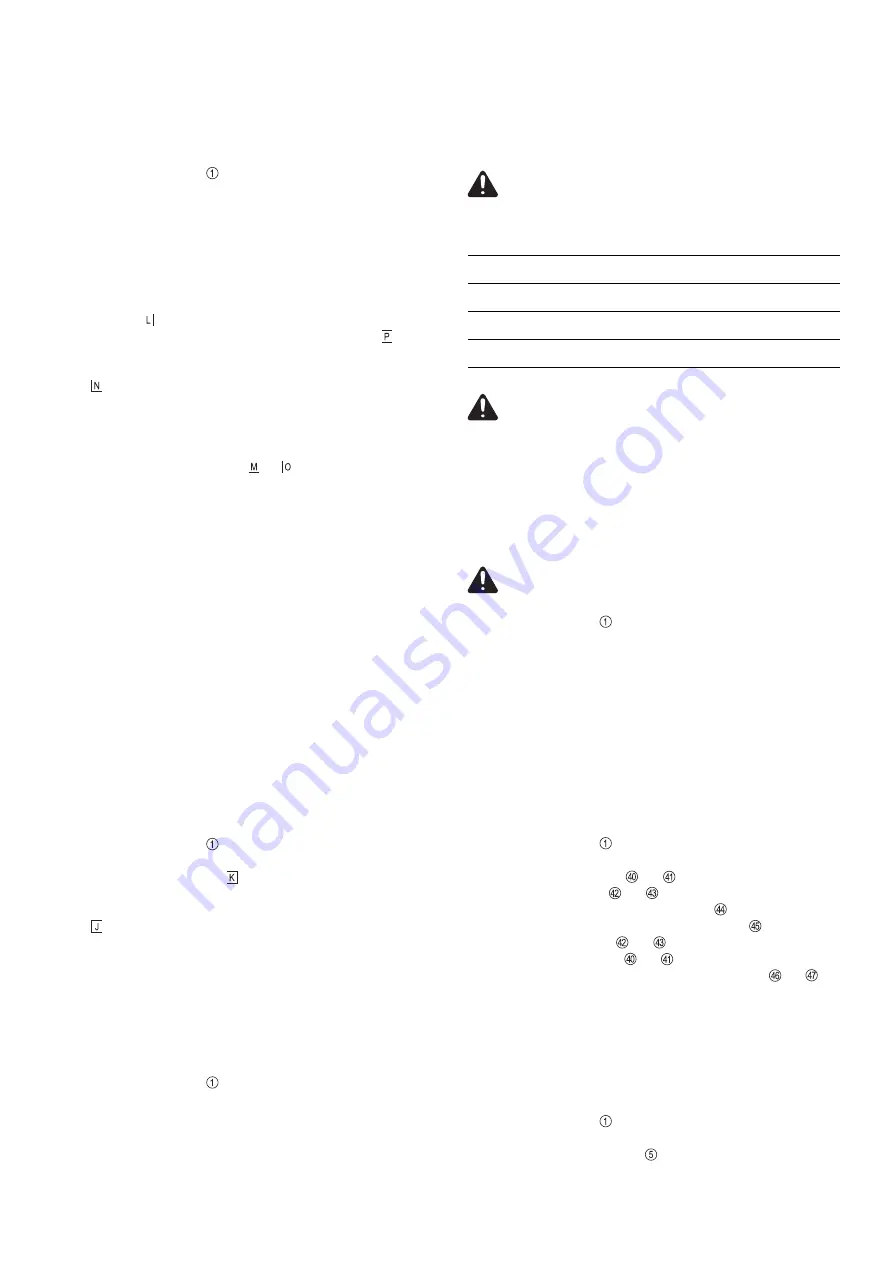
39
MOUNTING THE INTERCONNECTING CABLE TO THE
WIREFEEDER
- Shift the mains switch to the O position
- Place the wirefeeder (with press-fit insulating sleeve) onto the location
pivot on the power source
- Loosen the cable grip and pull the interconnecting cable through, the right
way round, as far as the metal clamping sleeve on the protective hose
N.B. !
Do not cross over or kink any of the lines
- Plug the Welding potential bayonet socket of the interconnecting cable
to socket and turn it to latch it
- Plug the 37-pole control socket into the control-plug socket and fasten
it tightly with the swivel nut
- Plug the gas hose of the interconnecting cable onto the shielding gas socket
and tighten with the swivel nut
N.B. !
First check whether O-ring seals have been inserted
- Plug the water forward-flow and return-flow hoses of the interconnecting
cable to the plug-on connectors and , red-to-red and black-to-black,
and tighten with the swivel nut
- Screw down the tension-relieving cable-grip
MOUNTING / CONNECTING THE GAS CYLINDER
- Stand the cylinder on the platform of the power-source trolley
- Fix the gas cylinder in place with both safety chains
N.B.!
The cylinder is only fixed properly if the chains are placed around the
top part of the cylinder (but not around the neck of the cylinder)
- Take off the protective cap from the cylinder
- Give the cylinder valve a quick turn to the left so as to blow off any dirt
that may have accumulated
- Check the seal on the pressure regulator
- Screw the pressure regulator onto the gas cylinder and tighten it
- Link up the shielding-gas connector on the interconnecting cable to the
pressure regulator, by means of the gas hose
MOUNTING THE WELDING TORCH
- Shift the mains switch to the O position
- Check that the torch is correctly tooled up. Insert it - infeed tube first - into
the central torch connector
- Tighten the swivel nut by hand to fix the torch in place
- Plug the control plug of the welding torch onto the torch control connection
and latch it
- Plug the gas-hose of the welding torch into the gas connector and latch it
STARTING UP THE COOLING UNIT
N.B.!
Always check the volume and cleanliness of the coolant water before
starting to use the unit. The cooling unit is factory-filled with approx. 2l of coolant
(mixing ratio 1:1) before dispatch.
- Shift the mains switch to the O position
- Remove the screw cap
- Top up with coolant (mixing ratio as per following table)
- Screw the cap back on again
N.B.!
Use clean tap water only. The electrical conductivity of all other
antifreeze agents makes them unsuitable for use here.
Warning!
As Fronius has no influence on factors such as the quality,
purity and filling-level of the coolant, no warranty is given for the
coolant pump.
Outside temperature
Water-to-spirit mixing ratio
+ °C to -5°C
4 l : 1 l
-5°C to -10°C
3.75 l : 1.25 l
-10°C to -15°C
3.5 l : 1.5 l
-15°C to -20°C
3.25 l : 1.75 l
Warning!
The coolant circulation must be checked at regular intervals
while the machine is in operation - it must be possible to see that the
return-flow to the reservoir is working correctly.
Under more difficult conditions (extra-long hosepacks, big height differences
etc.), use the FK 71 R cooling unit, with a cooling power of 2.6 kW and a pump
pressure of 4.4 bar.
MOUNTING THE WIRE SPOOL
Warning!
The wire-reel fixture is only for holding and securing
standard welding-wire reels of max. 20 kg.
- Shift the mains switch to the O position
- Open the wire-spool cover
- Mount the wire spool onto the spool holder - the right way round
- Slot the locking bolt into the opening provided on the body of the spool
- Adjust the braking force with the clamping screw
- Replace the wire-spool cover or side panel
N.B.!
The brake should always be adjusted so that the wire does not continue
unreeling after the end of welding - but without overtightening the clamping
screw, as this would cause motor overload.
FEEDING IN THE WIRE ELECTRODE
- Shift the mains switch to the O position
- Open the wire-spool cover
- Pivot the clamping devices and forwards
- Pull the pressure levers and upwards
- Insert the wire electrode though the infeed tube of the 4-roller drive and
around 5 cm into the infeed tube of the welding torch
- Push the pressure levers and downwards
- Pivot the clamping devices and into the vertical position
- Set the contact pressure by means of the clamping nuts and
N.B.!
Set a contact pressure that is high enough to ensure smooth wire feed,
but not so high that the wire electrode is deformed.
- Arrange the hosepack in as straight a line as possible
- Detach the gas nozzle from the torch
- Unscrew the contact tube
- Plug in the mains plug
- Shift the mains switch to the I position
- Mains control lamp lights up
- Shift the program selector switch to the required position (No Program
indicator must not light up)
Содержание T.I.M.E. SYNERGIC
Страница 2: ......
Страница 27: ...OPERATING INSTRUCTIONS...
Страница 28: ......
Страница 53: ...MODE D EMPLOI...
Страница 54: ......
Страница 79: ...ERSATZTEILLISTE SPARE PARTS LIST LISTE DE PI CES DE RECHANGE...
Страница 80: ......