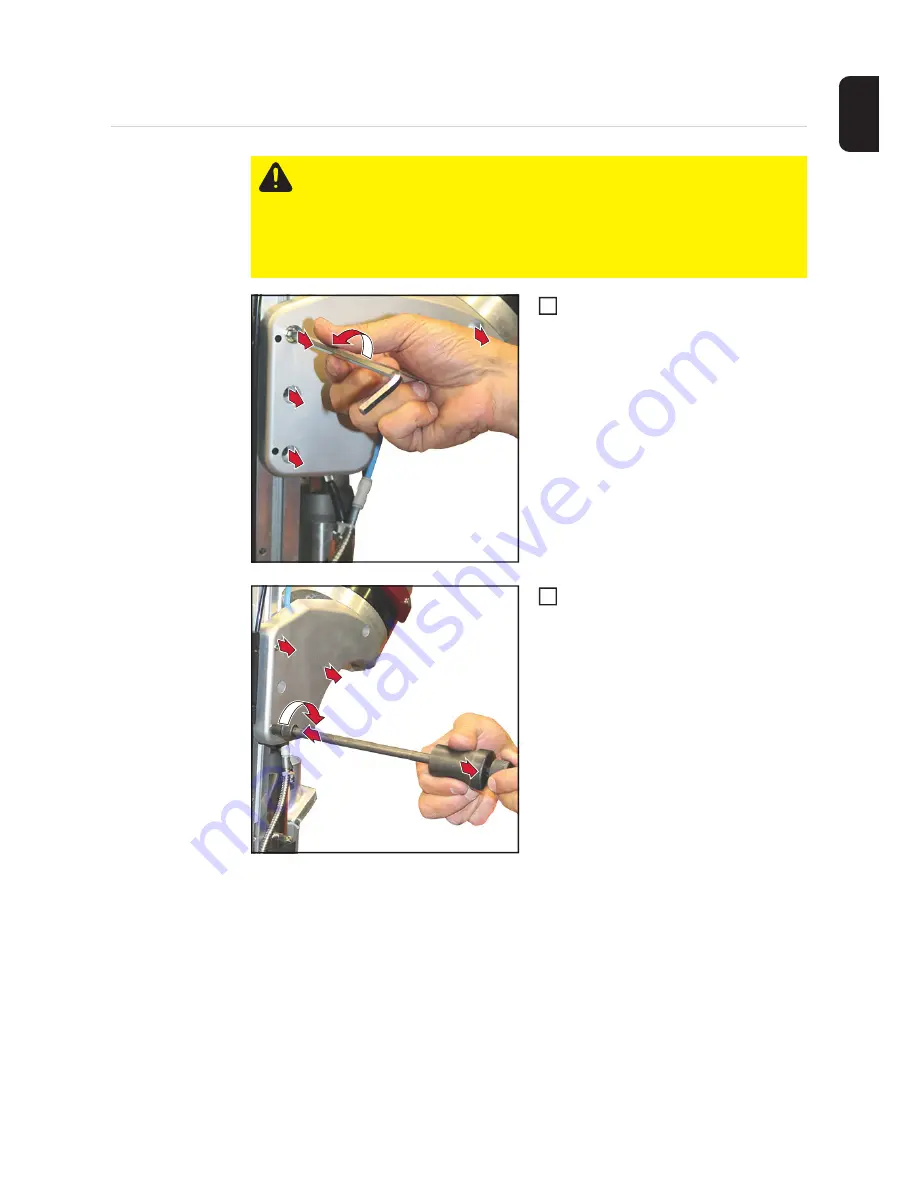
53
EN-US
Connecting Laser Optics and Extra Extraction
Connecting Laser
Optics
Remove 5 x Allen screws size 6 mm
For assembly:
the 3 x shorter screws are located one be-
low the other; the 2 x longer screws opposi-
te each other.
Remove 2 x register pins:
a)
Position and connect extractor
tool for register pins
b)
Hit the vibrating mass on the ext-
ractor tool backward and then re-
move the register pins
c)
Remove bracket for robot connec-
tion
CAUTION!
Risk of damage to the laser welding head as a result of contamination
from above.
-
Please observe the Operating Instructions, specifications and safety instruc-
tions issued by the manufacturer of the laser optics
-
Prior to connection, position the laser welding head so that the longitudinal
axis on the laser welding head is outside of the horizontal (> 90°). This will
ensure that no dirt can get into the laser optics from above.
1
1
5x
1
1
1
1
b
a
a
c
c
2
Содержание LaserHybrid MHP 360i LH
Страница 2: ...2 ...
Страница 4: ...4 ...
Страница 8: ...8 ...
Страница 17: ...General Information ...
Страница 18: ......
Страница 29: ...Operating controls and connections ...
Страница 30: ......
Страница 38: ...38 ...
Страница 39: ...Commissioning ...
Страница 40: ......
Страница 49: ...49 EN US Pull the protective hoses across the connections 8 8 8 ...
Страница 74: ...74 ...
Страница 75: ...Maintenance ...
Страница 76: ......
Страница 98: ...98 ...
Страница 99: ...Appendix ...
Страница 100: ......
Страница 102: ...102 Spare parts list LaserHybrid TPSi PP PP 0RXQWLQJ SODWH QRW LQFOXGHG LQ VHW ...
Страница 103: ...103 9 9 9 QJLQH 8QLW 5 1 5 5 75 7 6 EOXH UHG EODFN QRW LQFOXGHG LQ VHW QRW LQFOXGHG LQ VHW ...
Страница 104: ...104 DVHU EULG PP PP PP 8 U1L 2SWLRQ 0LQL URVV HW ...
Страница 106: ...106 7UXPSI 2SWLF 5H HVLJQ IRFDO OHQJWK PP ...
Страница 107: ...107 7UXPSI 2SWLF DPHUD 5H HVLJQ IRFDO OHQJWK PP ...
Страница 108: ...108 3UHFLWHF 2SWLF IRFDO OHQJWK PP ...
Страница 109: ...109 LJK DJ 2SWLF IRFDO OHQJWK PP ...
Страница 110: ...110 ...