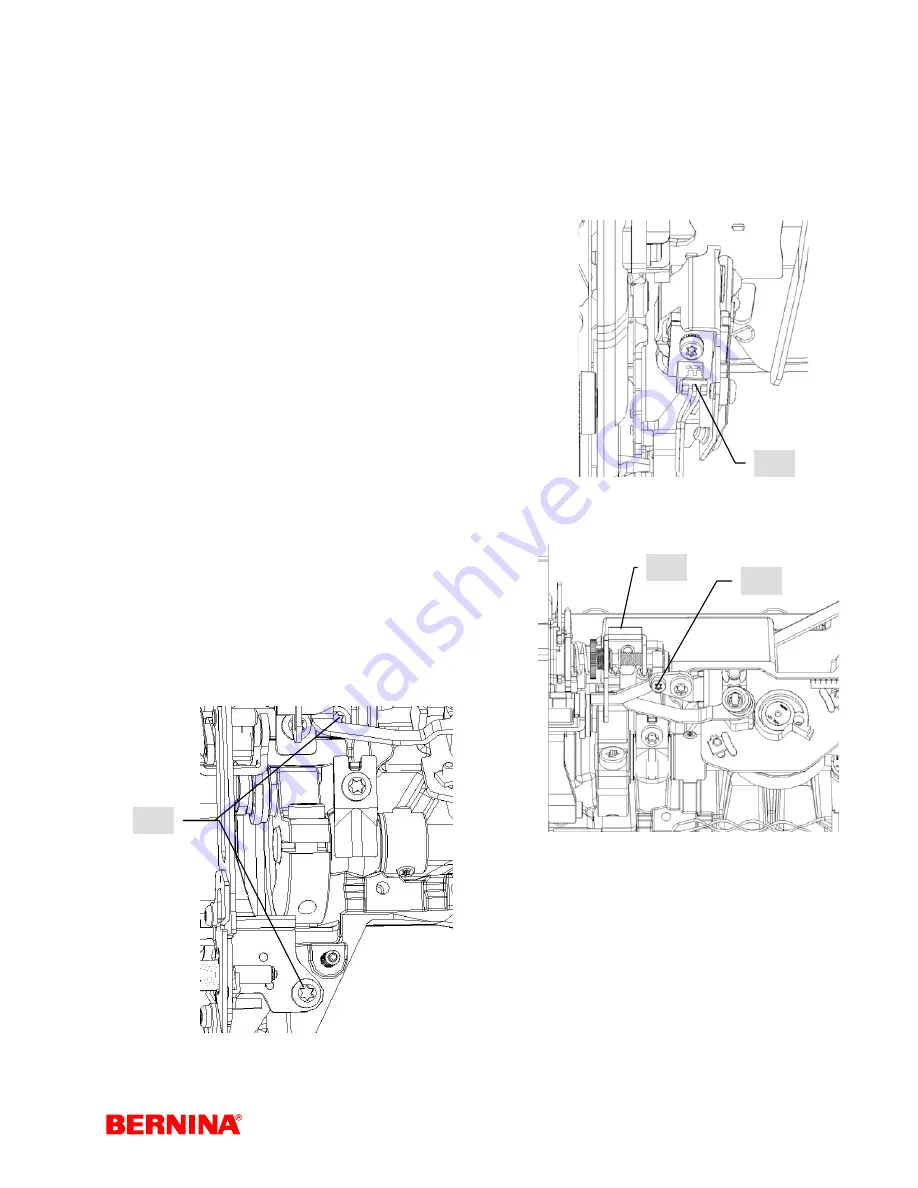
Service-Manual_artista_630_640_english_V4.01_032069_50_04.doc
42
4.24 artista 640 upper thread tension
Disassembly:
1. Remove
covers.
2. Disconnect thread clamp magnet (
22
)
3. Remove link clip (
20
).
4. Remove
screw
(
21
).
5. Remove the two securing screws (
58
).
6. Remove thread tension unit.
Assembly:
1. Fit new thread tension unit and tighten securing screws (
58
)
and (
21
).
2. Refit link clip (
20
).
3. Note the position of the thread tension release.
4. Set the stitch width limiter (
73
) with screw (
74
).
5. Reconnect thread clamp magnet plug.
6. Refit rear and front covers.
7. Set thread tensioner (
p. 63-64
).
8. Set regulator spring (
p. 65
):
9. Check thread tension release mechanism. (
p. 61
)
10. Sew-off.
58
20
21
22