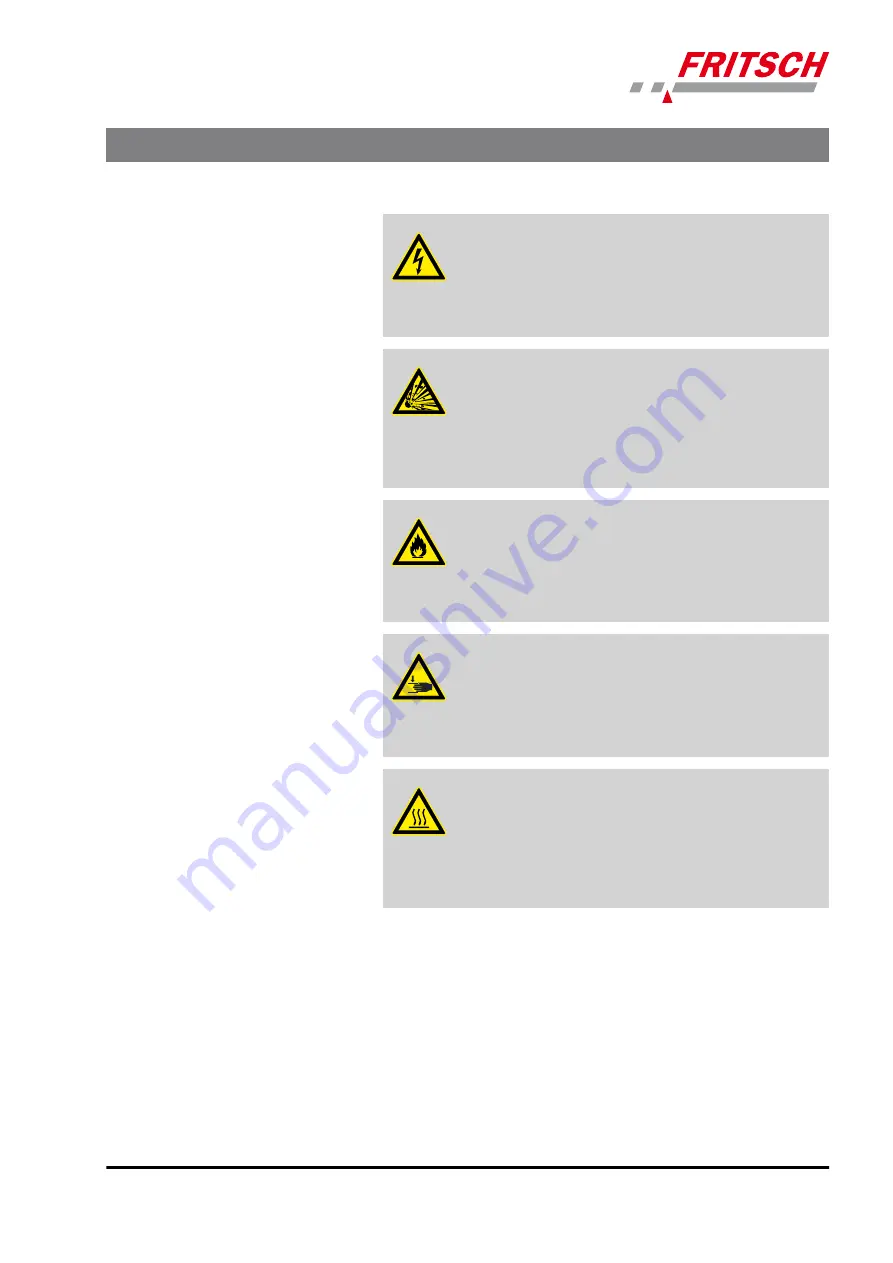
DANGER!
This symbol and keyword combination points out a
directly hazardous situation due to electrical current.
Ignoring information with this designation will result in
serious or fatal injury.
DANGER!
This symbol and keyword combination designates con-
tents and instructions for proper use of the machine in
explosive areas or with explosive substances. Ignoring
information with this designation will result in serious
or fatal injury.
DANGER!
This symbol and keyword combination designates con-
tents and instructions for proper use of the machine
with combustible substances. Ignoring information with
this designation will result in serious or fatal injury.
WARNING!
This symbol and keyword combination points out a
directly hazardous situation due to movable parts.
Ignoring information with this designation can result in
hand injuries.
WARNING!
This symbol and keyword combination points out a
directly hazardous situation due to hot surfaces.
Ignoring information with this designation can result in
serious burn injuries due to skin contact with hot sur-
faces.
Safety information can refer to specific, individual procedure instructions.
Such safety information is embedded in the procedure instructions so
that the text can be read without interruption as the procedure is being
carried out. The keywords described above are used.
Safety information in the procedure
instructions
Safety information and use
- 11 -
Содержание PULVERISETTE 1 premium Series
Страница 17: ...3 8 Protection class IP 44 Technical data 17 ...
Страница 54: ...14 Safety logbook Date Maintenance Repair Name Signature Safety logbook 54 ...
Страница 56: ...V Voltage 16 W Warning information 10 WEEE 49 Weight 16 Index 56 ...
Страница 57: ......