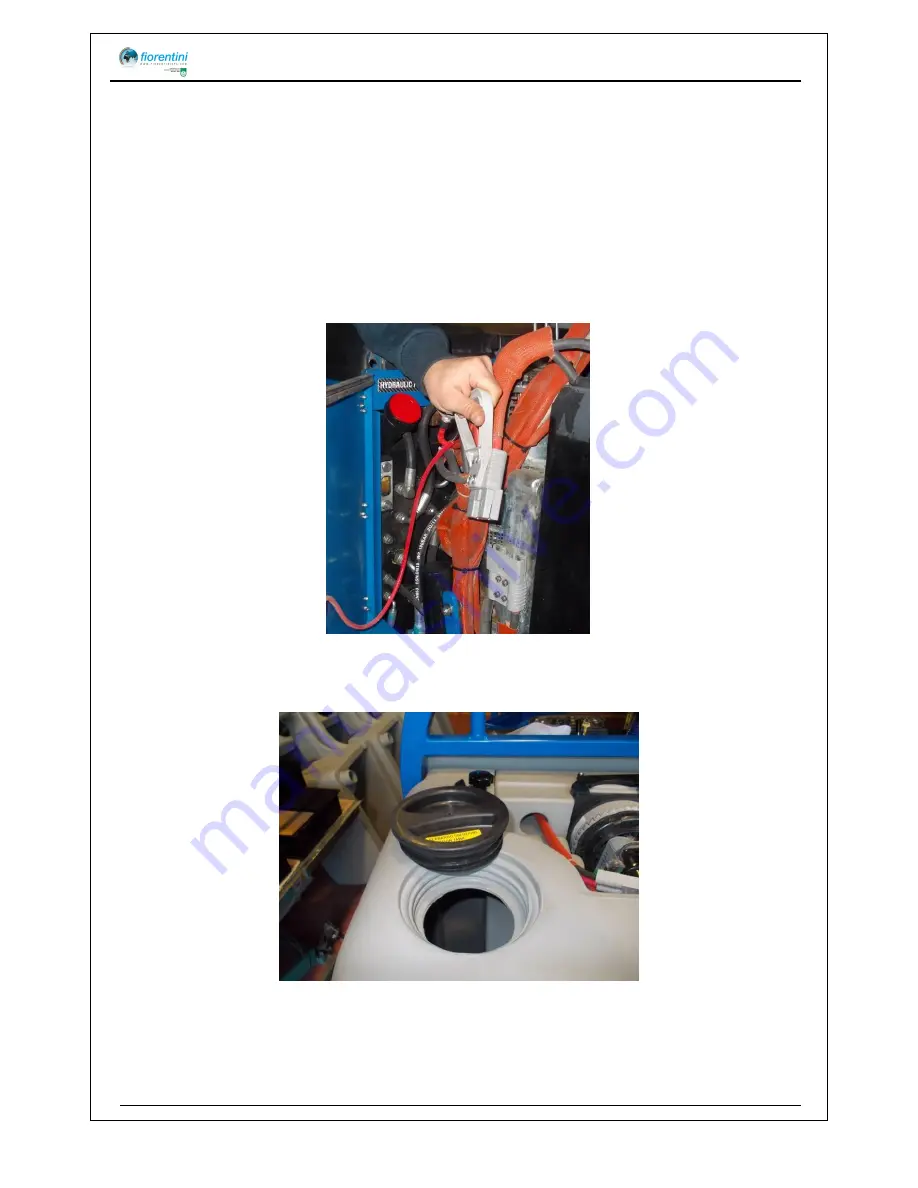
MAINTENANCE
I115SS
Rev. 001
22/12/2014
29/58
4.7.1 PREPARING AND STARTING THE MACHINE
If the cleaning machine battery charger is plugged in, unplug the battery charger connected to the machine
battery and connect the battery plug to the machine power plug (fig 4.6), then fill the machine with water
through the filler plug (detail 1 figure 4.7).
Check the oil level via the special indicator in the top part of the tank. To obtain access to the hydraulic oil
tank, open the machine left side panel (figure 4.8).
The machine can now be powered on by turning the main key switch when the operator is sitting in the
driver's seat.
.
FIGURE 4.6
FIGURE 4.7