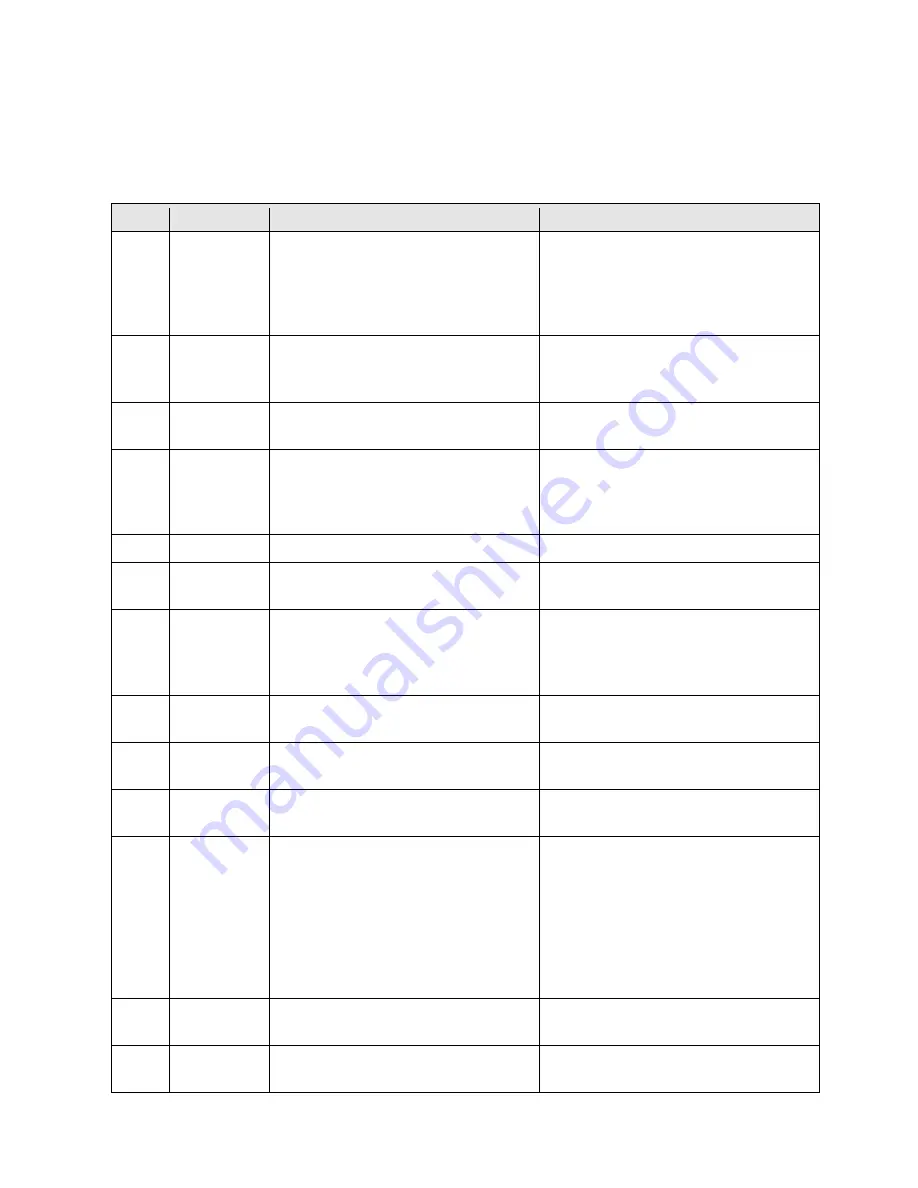
73
Chapter 8
Alarms and troubleshooting
Alarm code numbers flash at the panel when the controller generates an alarm.
If you need more detailed information about errors and error history, please connect the controller to the PC
via RS232 and refer to chapter 5.7.
Table 8-1: Alarm codes of Error_State1
Alarm
Name
Reason
Troubleshooting
FFF.F
Wrong motor
model
The current motor type is different from the
motor type which is saved in the controller.
Method 1: Access EA01 via the KEY, and
confirm motor type, then access EA00, set 2.
Method2: Access EASY_MT_TYPE (0x304101)
via PC software, confirm the value, then save
the parameter.
000.1
Extended Error
Errors occurs in
Error_State2
Press the SET key to enter Error_State2
(d1.16), read the error bit, check the error
meaning in table 8-2.
000.2
Encoder not
connected
The encoder wiring is incorrect or
disconnected.
Use a multimeter to check connection of the
encoder signal cable
000.4
Encoder
internal
Internal encoder erroror the encoder is
damaged.
1.Access panel address d3.51 Encoder_OP by
KEY and set 1.
2.Try to reset the controller error. If error
persists, replace the motor.
000.8
Encoder CRC
Encoder CRC error
Make sure the equipment is well grounded
001.0
Controller
Temperature
The temperature of controller’s power
module has reached the alarm value.
Improve the cooling environment of the
controller.
002.0
Overvoltage
Supply power voltage exceeds the allowable
input voltage range
In case of emergency stop, there is no
external braking resistor or braking.
Check to see if supply power voltage is
unstable and if a suitable braking resistor is
connected.
004.0
Undervoltage
The power voltage input is lower than the
low voltage protection alarm value.
Check to see if supply power voltage is
unstable.
008.0
Overcurrent
Instantaneous current exceeds the
overcurrent protection value.
Check the motor cable for short circuits.
Replace the controller.
010.0
Chop Resistor
The braking resistor is overloaded or it’s
parameters are not set correctly.
Set the resistance and power of the external
braking resistor through d5.04 and d5.05.
020.0
Following Error
The actual following error exceeds the
setting value of Max_Following_Error.
1. Stiffness of control loop is too small.
2.The controller and motor together can’t
match the requirement of the application.
3. Max_Following_Error (d2.25) is too small.
4. feedforward settings are not feasible.
5. Wrong motor wiring.
Check and solve based on the reasons.
040.0
Low Logic
Voltage
Logic power voltage is too low.
Check to see if logic power voltage is unstable.
080.0
Motor or
controller IIt
The brake is not released when the motor
shaft is rotating
Measure the brake terminal voltage is right
and the brake is released when the controller