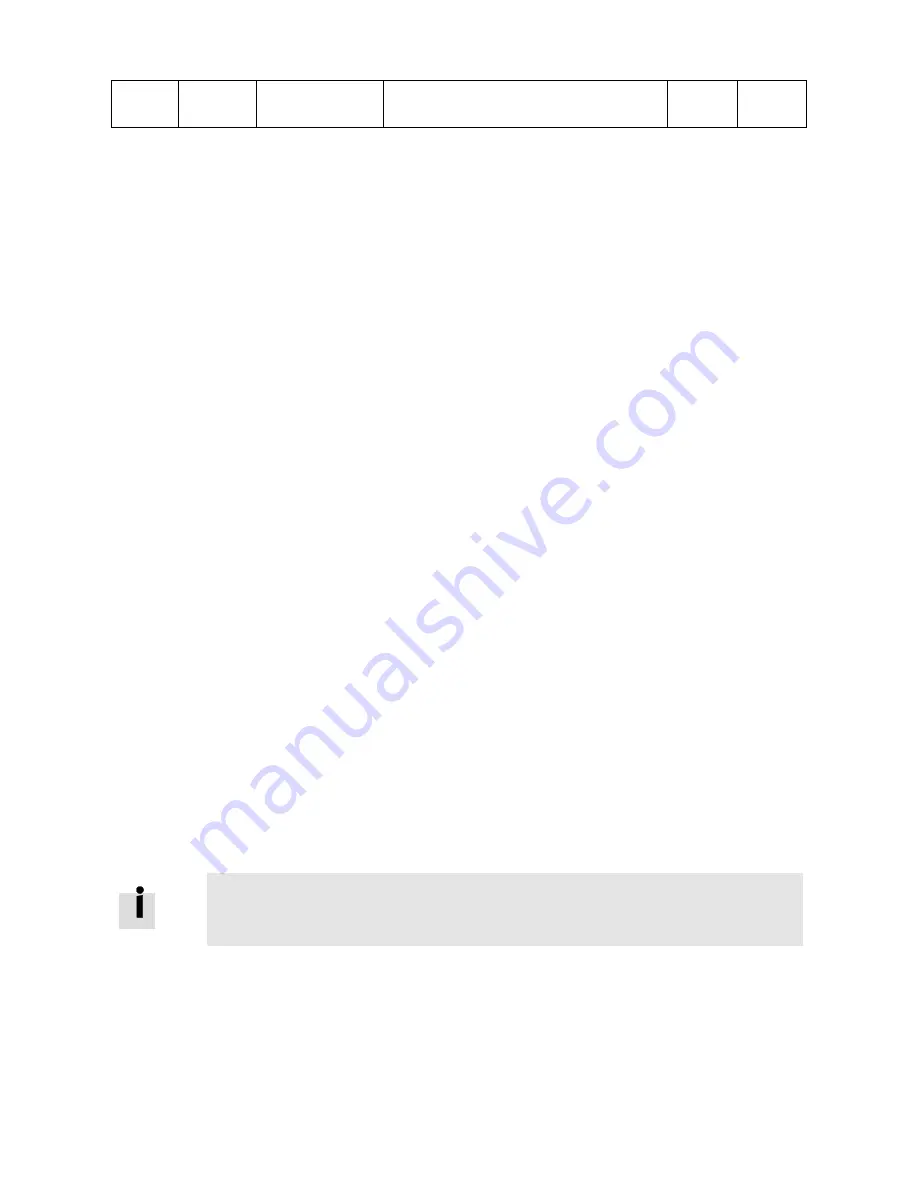
71
d2.25
2FF0.0E
Max_Following_
Error_16
Maximum allowable error, Max_Following_Error
(6065.00) = 100 * Max_Following_Error_16
5242
/
Position loop proportional gain adjustment
Increasing position loop proportional gain can improve position loop bandwidth, thus reducing positioning
time and following error, but setting it too high will cause noise or even oscillation. It must be set according
to load conditions. Kpp = 103 * Pc_Loop_BW, Pc_Loop_BW is position loop bandwidth. Position loop
bandwidth cannot exceed velocity loop bandwidth. Recommended velocity loop bandwidth:
Pc_Loop_BW<Vc_Loop_BW / 4, Vc_Loop_BW.
Position loop velocity feedforward adjustment
Increasing the position loop velocity feedforward can reduce position following error, but can result in
increased overshooting. If the position command signal is not smooth, reducing position loop velocity
feedforward can reduce motor oscillation.
The velocity feedforward function can be treated as the upper controller (e.g. PLC) have a chance to directly
control the velocity in a position operation mode. In fact this function will expend part of the velocity loop
response ability, so if the setting can’t match the position loop proportional gain and the velocity loop
bandwidth, the overshot will happen.
Besides, the velocity which feedforward to the velocity loop may be not smooth, and with some noise signal
inside, so big velocity feedforward value will also amplified the noise.
Position loop acceleration feedforward
It is not recommended that the user adjust this parameter. If very high position loop gain is required,
acceleration feedforward K_Acc_FF can be adjusted appropriately to improve performance.
The acceleration feedforward function can be treat as the upper controller (e.g. PLC) have a chance to
directly control the torque in a position operation mode. in fact this function will expend part of the current
loop response ability, so if the setting can’t match the position loop proportional gain and the velocity loop
bandwidth, the overshot will happen.
Besides, the acceleration which feedforward to the current loop can be not smooth, and with some noise
signal inside, so big acceleration feedforward value will also amplified the noise.
Acceleration feedforward can be calculated with the following formula:
ACC_%=6746518/ K_Acc_FF/ EASY_KLOAD*100
ACC_%: the percentage which will be used for acceleration feedforward.
K_Acc_FF(60FB.03): the final internal factor for calculating feedforward.
EASY_KLOAD(3040.07): the load factor which is calculated from auto-tuning or the right inertia ratio input.
Information
The smaller the K_Acc_FF, the stronger the acceleration feedforward.
Smoothing filter
The smoothing filter is a moving average filter. It filters the velocity command coming from the velocity
generator and makes the velocity and position commands more smooth. As a consequence, the velocity
command will be delayed in the controller. So for some applications likeCNC, it’s better not to use this filter
and to accomplish smoothing with the CNC controller.