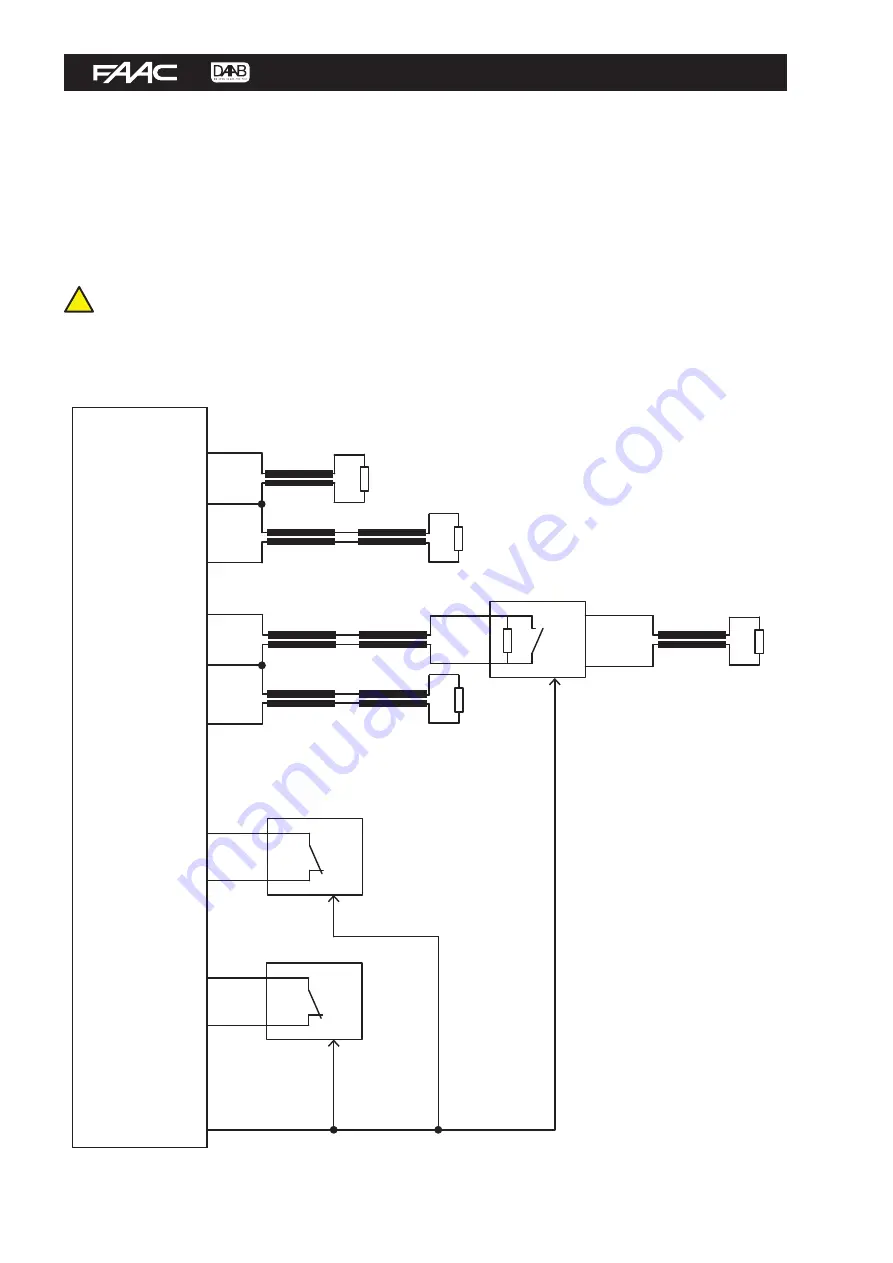
CHANNEL LIST DAAB AUTOMATIC CONTROL UNIT EP104 4.08
4
Channel list edition 1 for EP104 version 4.08
• Connecting a safety edge
The safety edge resistor must be installed in the safety edge so that an open-circuit in the resistor or the cable is interpreted as
actuation of the device. See the wiring diagram below. SE.C1 and SE.01 must be used for a safety edge connected to the half
to which motor 1 is connected, and SE.C2 and SE.O2 to the half to which motor 2 is connected.
The resistor can be between 1.0-8.2 kΩ with a 1% tolerance and a power capability of at least ½ W. FAAC Nordic AB
recommends an impedance of 8.2 kΩ. A safety edge can only be connected in series.
When connecting in series, only one resistor is used in the outermost safety edge, as shown in the wiring diagram below. The
maximum number of safety edges connected in series with an impedance of 8.2 kΩ is six per input.
Note that the impedance used for a safety edge must be checked and entered into the EP104 during commissioning, see
Commissioning below.
!
Other types of impedance safety edge must not be connected directly to the safety edge inputs – they require an external
control unit.
See the instruction manual for these safety edges.
Use only safety edges approved by FAAC Nordic AB.
• Connecting safety edges and photocells
The diagram below illustrates how to connect an external safety edge unit.
1
2
3
5
4
FC-output 28
FC-input 29
Test output 32
EP104
Photocell
External unit for
personal protection
Test input
Safety edge SE.C1
Safety edge SE.C2
Safety edge SE.O1
Safety edge
Test input
8,2k
8,2k
8,2k
8,2k
Photocell
Test input
INP6-output 25
INP6-input 27
8,2k
6
Safety edge SE.O2
Safety edge
Safety edge
Safety edge
Safety edge
Safety edge
Safety edge
Safety edge