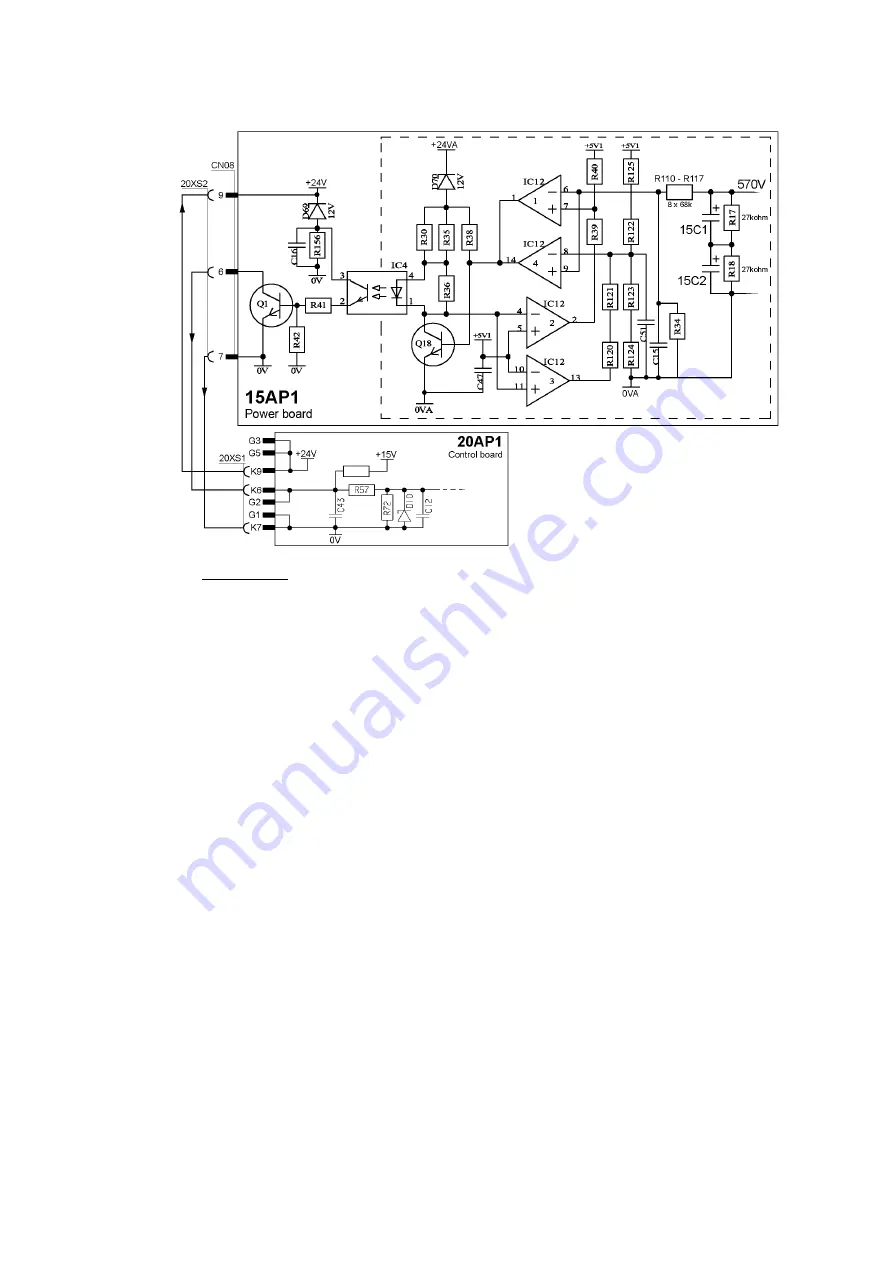
S0740 800 196/E101019/P76
- 20 -
ca41_15_1
15AP1:3
Overvoltage and undervoltage protection
WARNING!
Dangerous voltage. Mains voltage on circuit board 15AP1 when
connected to the 400 V supply.
0 VA on power board 15AP1 is connected to the mains supply.
0 VA is galvanically isolated from 0 V.
The overvoltage and undervoltage protection generates a fault signal if the
voltage across capacitors 15C1 and 15C2 falls outside the permitted interval of
300 - 715 V DC, which is equivalent to a mains voltage of 212 - 505 V AC.
In the event of a fault, the display panel will show fault code 5.
The fault state will not be reset until the DC voltage is within 400 to 650 V.
During normal operating conditions, the voltage between pins CN08:6 and 7
on circuit board 15AP1 is about 0.1 V. Optocoupler IC4 is used for galvanic
isolation of the voltage monitoring circuit from control board 20AP1.
A break in any of the conductors to/from 15AP1, as shown in the diagram
above will result in a fault state.
Содержание Aristo Mig 3001i
Страница 10: ...S0740 800 196 E101019 P76 Mig 3001i 10 ca41_00 ...
Страница 11: ...S0740 800 196 E101019 P76 Placement of the circuit boards Mig 3001i 11 ca41_00 ...
Страница 12: ...S0740 800 196 E101019 P76 Tig 3001i Placement of the circuit boards Tig 3001i 12 ca41_00 ...
Страница 13: ...S0740 800 196 E101019 P76 13 ca41_00 ...
Страница 23: ...S0740 800 196 E101019 P76 15AP1 Component positions 23 ca41_15_1 ...
Страница 35: ...S0740 800 196 E101019 P76 20AP1 Component positions version 1 35 ca41_20_1 ...
Страница 36: ...S0740 800 196 E101019 P76 20AP1 Component positions version 2 36 ca41_20_1 ...
Страница 47: ...S0740 800 196 E101019 P76 Power board 15AP1 measuring points 47 ca41f2pwr ...
Страница 49: ...S0740 800 196 E101019 P76 49 ca41f2pwr Secondary board 15AP2 measuring points ...
Страница 53: ...S0740 800 196 E101019 P76 Soft starting measuring points power board 15AP1 53 ca41f2soft ...
Страница 75: ...S0740 800 196 E101019 P76 75 emptypage ...