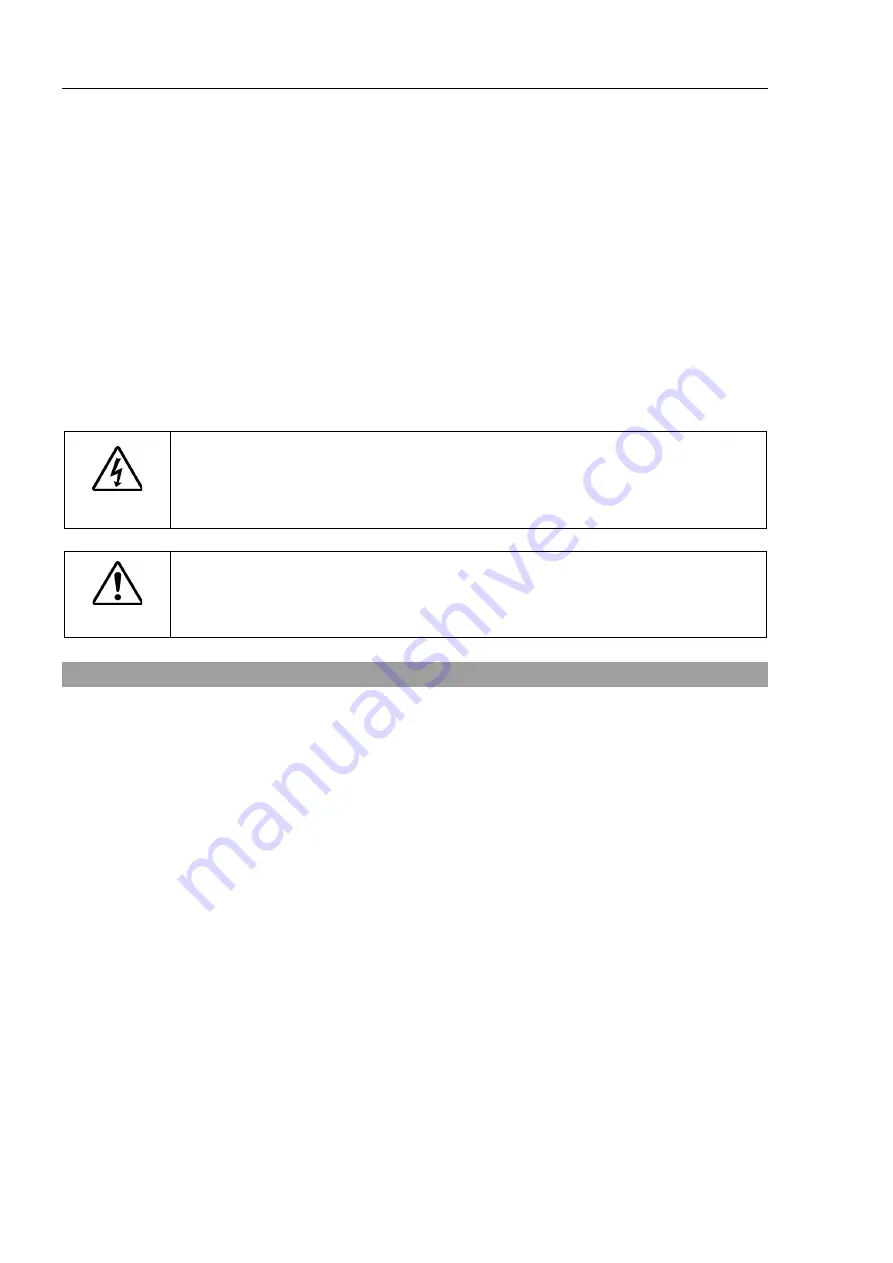
GX4 Manipulator 3. Environments and Installation
30
GX series Rev.2
Special Environmental Conditions
The surface of the Manipulator has general oil resistance. However, if your requirements
specify that the Manipulator must withstand certain kinds of oil, please contact the
supplier of your region.
Rapid change in temperature and humidity can cause condensation inside the
Manipulator.
If your requirements specify that the Manipulator handles food, please contact the
supplier of your region to check whether the Manipulator will damage the food or not.
The Manipulator cannot be used in corrosive environments where acid or alkaline is used.
In a salty environment where the rust is likely to gather, the Manipulator is susceptible
to rust.
WARNING
■
Use an earth leakage breaker on the power of the Controller to avoid electric
shock and circuit breakdown caused by short circuit.
Prepare the earth leakage breaker that pertains the Controller you are using. For
details, refer to the Controller manual.
CAUTION
■
When cleaning the Manipulator, do not rub it strongly with alcohol or benzene. It
may lose luster on the coated face.
3.2 Base Table
A base table for anchoring the Manipulator is not supplied. Please make or obtain the
base table for your Manipulator.
The shape and size of the base table differs depending on the use of the robot system.
For your reference, we list some Manipulator table requirements here.
The base table must not only be able to bear the weight of the Manipulator but also be
able to withstand the dynamic movement of the Manipulator when it operates at
maximum acceleration/deceleration. Ensure that there is enough strength on the base
table by attaching reinforcing materials such as crossbeams.
The torque and reaction force produced by the movement of the Manipulator are as
follows:
Max. Horizontal torque
:
500 Nm
Max. Horizontal reaction force :
2000 N
Max. Vertical reaction force
:
1000 N
The threaded holes required for mounting the Manipulator base are M8.
Use mounting bolts with specifications conforming to ISO898-1 property class: 10.9 or
12.9. For dimensions, refer to “
2.2 Part Names and Outer Dimensions
” and “
3.3
Mounting Dimensions
”.
Содержание SCARA GX Series
Страница 1: ...Original instructions Rev 2 EM221R5129F SCARA Robots GX series Manual ...
Страница 2: ...GX series Manual Rev 2 ...
Страница 12: ......
Страница 86: ...GX4 Manipulator 5 Motion Range 76 GX series Rev 2 ...
Страница 88: ......
Страница 188: ......
Страница 202: ......
Страница 211: ...Appendix B Time and Distance of Free Running in Emergency GX series Rev 2 201 GX4 A25 J3 Standard Boost ...
Страница 213: ...Appendix B Time and Distance of Free Running in Emergency GX series Rev 2 203 GX4 A30 J3 Standard Boost ...
Страница 215: ...Appendix B Time and Distance of Free Running in Emergency GX series Rev 2 205 GX4 A35 J3 Standard Boost ...
Страница 217: ...Appendix B Time and Distance of Free Running in Emergency GX series Rev 2 207 GX8 A45 J3 Standard Boost ...
Страница 219: ...Appendix B Time and Distance of Free Running in Emergency GX series Rev 2 209 GX8 A55 J3 Standard Boost ...
Страница 221: ...Appendix B Time and Distance of Free Running in Emergency GX series Rev 2 211 GX8 A65 J3 Standard Boost ...
Страница 224: ...Appendix C Time and Distance of Free Running When Safeguard Is Opened 214 GX series Rev 2 GX4 A25 J3 Standard Boost ...
Страница 226: ...Appendix C Time and Distance of Free Running When Safeguard Is Opened 216 GX series Rev 2 GX4 A30 J3 Standard Boost ...
Страница 230: ...Appendix C Time and Distance of Free Running When Safeguard Is Opened 220 GX series Rev 2 GX8 A45 J3 Standard Boost ...
Страница 232: ...Appendix C Time and Distance of Free Running When Safeguard Is Opened 222 GX series Rev 2 GX8 A55 J3 Standard Boost ...
Страница 234: ...Appendix C Time and Distance of Free Running When Safeguard Is Opened 224 GX series Rev 2 GX8 A65 J3 Standard Boost ...
Страница 236: ...Appendix D Accuracy Range of Arm Length Offset 226 GX series Rev 2 GX8 series GX8 A45 GX8 A55 GX8 A65 ...