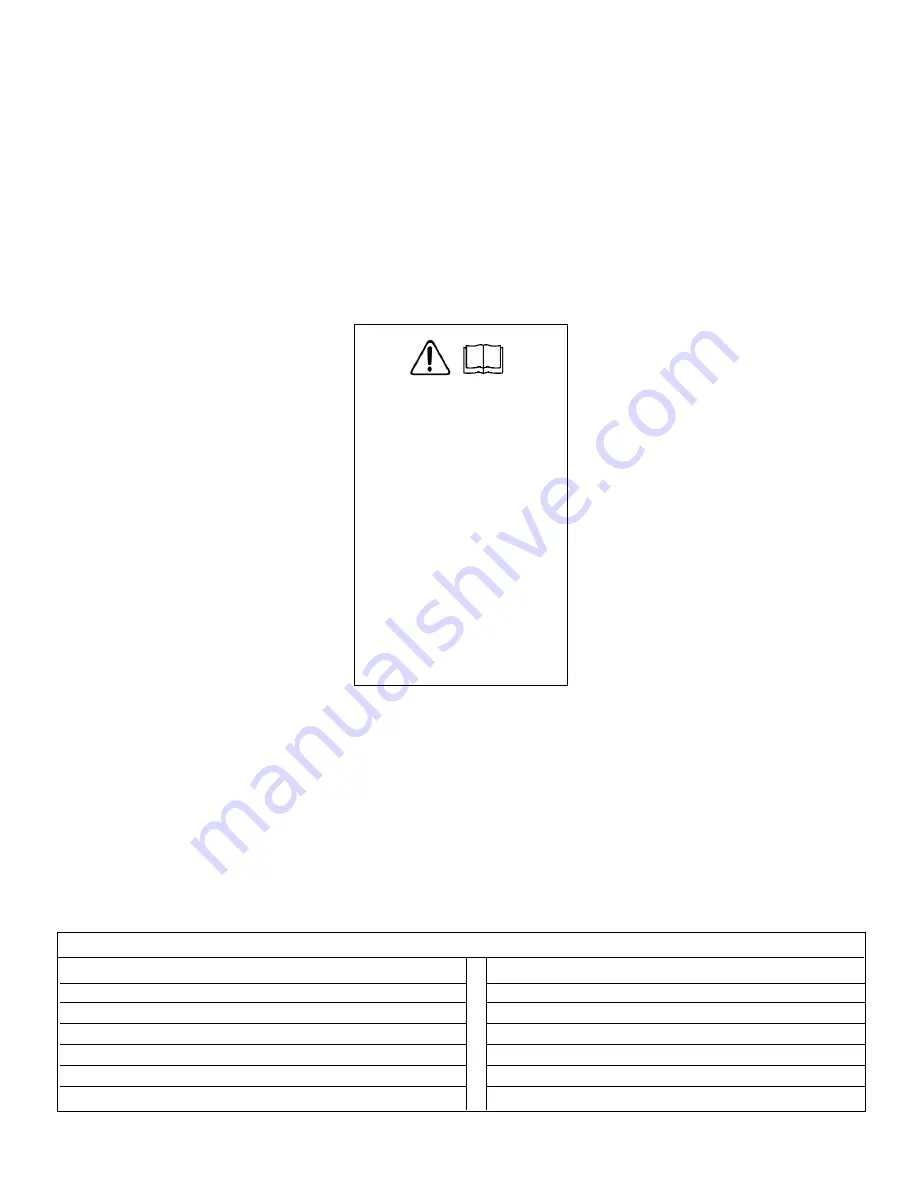
3
3.0 GENERAL DESCRIPTION
The Enerpac Synchronous Lift System is a package that provides
precise positional control of the lifting and lowering of high tonnage
objects. The personal computer based controller receives electronic
signals from load position sensors attached to the load, in the vicinity
of each cylinder. The controller software processes this information
and sends signals to the valves controlling each cylinder. Opening
and/or closing the valves as required, to raise or lower the load
evenly and within the accuracy parameters defined by the operator.
The Enerpac PC Based Synchronous Lift System consists of the
standard components outlined below. Refer to Figure 1 and 2 for
the layout of a typical eight-point lift system.
3.1 Standard Components
A: CONTROLLER (SLCPC-2001)
The CONTROLLER is where the operator
selects the lift parameters and controls up
to twenty-four lift points.
B: CONTROL VALVE MANIFOLD (SLVS-8)
The CONTROL VALVE MANIFOLD
CHART holds the control valve manifold,
which receives the on/off commands from
the controller. The manifold control valves
open and close, controlling the flow into the
cylinders, as they advance, or controlling
flow out of the cylinders as they retract,
keeping the load moving in a controlled
synchronous motion, while maintaining the
accuracy desired by the operator.
C: DISPLACEMENT SENSOR (SLSS-500,
1000, or 2000)
The SENSOR contains electronics to
detect load displacement.
D: SENSOR CABLE (SLSC-50 and SLEC-50)
The SENSOR CABLE transmits sensor
feedback signals to the CONTROLLER.
E: CHECK VALVE PACKAGE (SCK-1)
The PILOT OPERATED CHECK VALVE (SCK-1) provides
additional safety margin for load holding in the event of a
ruptured hose or a power failure.
The PILOT OPERATED
CHECK VALVE (SCK-1) is designed to be used with double-
acting HYDRAULIC CYLINDERS.
F: ELECTRO-BOX (SLEB-8, SLEB-16, or SLEB-24)
The ELECTRO-BOX receives valve control output voltages from
the CONTROLLER and distributes them to the appropriate
CYLINDER CONTROL VALVES, causing them to open or close,
as necessary, to control the lifting or lowering functions.
G: HYDRAULIC PUMP
The HYDRAULIC PUMP provides flow to the HYDRAULIC
CYLINDERS allowing them to advance or retract. The manifold
mounted DIRECTIONAL CONTROL VALVE is operated by the
CONTROLLER.
H: HYDRAULIC CYLINDER
The
HYDRAULIC CYLINDER
lifts or lowers the load.
I:
PRESSURE RELIEF VALVES
The adjustable PRESSURE RELIEF VALVES control maximum
system pressure in the advance and retract circuits.
J: DIRECTIONAL CONTROL VALVE
The manifold mounted DIRECTIONAL CONTROL VALVE
controls the advance and retract flows of the hydraulic fluid and
is under system control.
K: FLOW CONTROL VALVE
The FLOW CONTROL VALVE controls the
advance and retract speed of the
HYDRAULIC CYLINDERS.
L: PRESSURE TRANSDUCER
The PRESSURE TRANSDUCER allows
the operator to monitor system pressures.
M: VELOCITY FUSE (VF-1)
The VELOCITY FUSE provides additional
safety margin for load holding in the event of
a ruptured hose or a power failure. The
VELOCITY FUSE is designed to be used
with single-acting HYDRAULIC CYLINDERS.
N: SUCTION VALVE
The SUCTION VALVE is used to help
assist the return of hydraulic fluid back
from the HYDRAULIC CYLINDER into the
reservoir of the HYDRAULIC PUMP.
NOTE:
These are the major components required to operate
a two to eight point lifting system. Additional components will
be required for additional lift points. Contact Enerpac for
assistance in selecting components.
4.0
ELECTRICAL COMPONENT SPECIFICATIONS
(see tables)
IMPORTANT: The ENERPAC
PC BASED SYNCHRONOUS
LIFT SYSTEM is a precision
position control system,
which can be used in a wide
variety of applications.
Make certain that user
supplied components are
compatible. All operators
should read and thoroughly
understand this operating
manual before using the
equipment.
ELECTRO-BOX: SLEB-8, 16, or 24
Operating Temperature Range: 32 °F to 140 °F (0 °C to 60 °C)
Storage Temperature Range: 32 °F to 140 °F (0 °C to 60 °C)
Power Requirements: 120/230VAC 1 phase, 50/60 Hz., 750VA
Physical Dimensions: 36" (914,4 mm) x 24" (609,0 mm) x 7" (177,8 mm)
Weight: 150 lbs. (68 kg)
SENSOR: SLSS-500, 1000, or 2000
Measuring Range: 0-78.74" (0-2000 mm) of cord extension
Accuracy: ±.1% of stroke (±.040" or 1 mm for full extension)
Operating Temperature Range: 32 °F to 140 °F (0 °C to 60 °C)
Storage Temperature Range: 0 °F to 140 °F (-17 °C to 60 °C)
Physical Dimensions: 3.6" (93 mm) x 1.9" (50 mm) x 1.9" (50 mm)
Weight: 1.7 lbs. (0.8 kg) max.
ELECTRICAL COMPONENT SPECIFICATIONS
Содержание SLVS-8
Страница 99: ...99 L2543 O 08 01...
Страница 100: ...100...
Страница 101: ...101...
Страница 102: ...102...
Страница 103: ...103...
Страница 104: ...104...
Страница 105: ...105...
Страница 106: ...106 F E A C B D G...
Страница 107: ...107...
Страница 108: ...108...
Страница 109: ...109...
Страница 110: ...110...
Страница 111: ...111...
Страница 112: ...112...