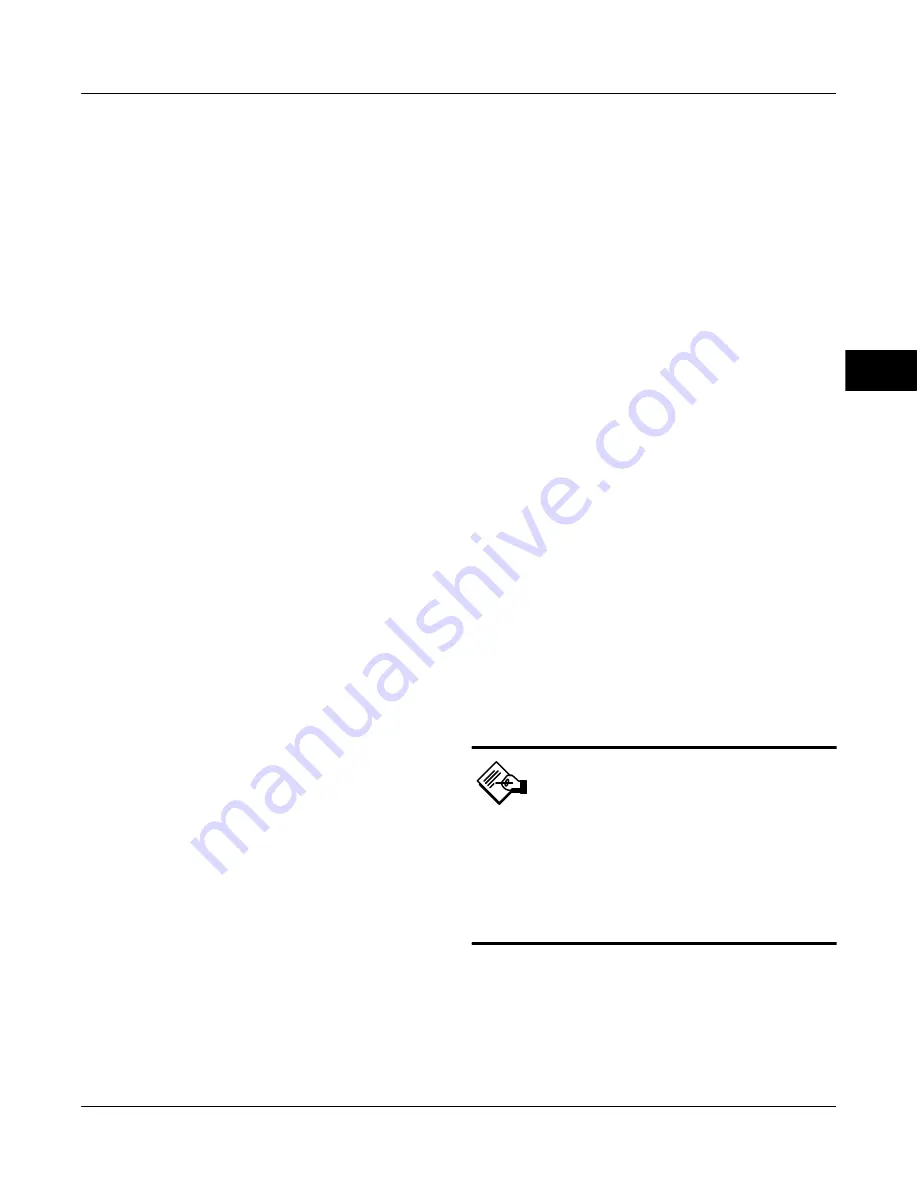
PID Function Block
November 2010
115
Feedforward Calculation
The feedforward value (FF_VAL [40]) is scaled
(FF_SCALE [41]) to a common range for compatibility
with the output scale (OUT_SCALE [11]). A gain value
(FF_GAIN [42]) is applied to achieve the total
feedforward contribution.
Output Tracking
Output tracking is enabled through the control options.
You can set control options in Manual or Out of
Service mode only.
The Track Enable control option must be set to True
for the track function to operate. When the Track in
Manual control option is set to True, the operator
cannot override the tracking function in Manual mode.
When Track in Manual is False, the operator can
override the tracking function when the block is in
Manual mode. Activating the track function causes the
block’s actual mode to revert to Local Override.
The TRK_VAL [38] parameter specifies the value to
be converted and tracked into the output when the
track function is operating. The TRK_SCALE [37]
parameter specifies the range of TRK_VAL [38].
When the TRK_IN_D [38] parameter is True and the
Track Enable control option is True, the TRK_VAL [38]
input is converted to the appropriate value and output
in units of OUT_SCALE [11].
Set Point Tracking
You can configure the method for tracking the set
point by configuring the following control options
(CONTROL_OPTS [12]):
SP
−
PV Track in Man—Permits the SP [8] to
track the PV [7] when the actual mode of the block is
Man.
SP
−
PV Track in LO or IMan—Permits the SP
[8] to track the PV [7] when the actual mode of the
block is Local Override (LO) or Initialization Manual
(IMan).
SP
−
PV Track in ROUT—Permits the SP [8] to
track the PV [7] when the actual mode of the block is
RemoteOut (ROUT).
SP Track retained Target—Causes the set point
to track the RCAS or CAS parameter based on the
retained target mode when the actual mode is MAN or
LO.
Act On IR—If this option is true, then when IR
(Initialization Requested) is received on BKCAL_IN
[27], the SP [8] will be adjusted within setpoint limits to
provide bumpless transfer when the cascade is
closed. If the setpoint required to provide bumpless
transfer is outside the setpoint limits, then any
difference added to provide bumpless transfer will be
removed in the BAL_TIME [25].
When one of these options is set, the SP[8] value is
set to the PV [7] value while in the specified mode.
You can select the value that a master controller uses
for tracking by configuring the Use PV for
BKCAL_OUT control option. The BKCAL_OUT [31]
value tracks the PV value. BKCAL_IN [27] on a
master controller connected to BKCAL_OUT [31] on
the PID block in an open cascade strategy forces its
OUT [9] to match BKCAL_IN [27], thus tracking the
PV from the slave PID block into its cascade input
connection (CAS_IN [18]). If the Use PV for
BKCAL_OUT option is not selected, the working set
point (SP_WRK [68]) is used for BKCAL_OUT [31].
You can set control options in Manual or Out of
Service mode only. When the mode is set to Auto, the
SP [8] will remain at the last value (it will no longer
follow the PV [7].
PID Equation Structures for
Enhanced PID Block
Note
Extended parameters are not
available at this time for all host
systems. Refer to your host
system documentation, or
contact your Emerson Process
Management sales office for
additional information.
Configure the STRUCTURECONFIG [71] parameter
to select the PID equation structure. You can select
one of the following choices:
Proportional, integral, and derivative on error
(PID)
4
Содержание FIELDVUE DVC6200f
Страница 42: ...DVC6200f Digital Valve Controller November 2010 30 4 ...
Страница 60: ...DVC6200f Digital Valve Controller November 2010 48 4 ...
Страница 108: ...DVC6200f Digital Valve Controller November 2010 96 4 ...
Страница 122: ...DVC6200f Digital Valve Controller November 2010 110 4 ...
Страница 188: ...DVC6200f Digital Valve Controller November 2010 176 4 ...
Страница 200: ...DVC6200f Digital Valve Controller November 2010 188 4 ...
Страница 216: ...DVC6200f Digital Valve Controller November 2010 204 5 ...
Страница 250: ...DVC6200f Digital Valve Controller November 2010 238 8 ...
Страница 251: ...Principle of Operation November 2010 239 A A Appendix A Principle of Operation Digital Valve Controller Operation 240 A ...
Страница 254: ...DVC6200f Digital Valve Controller November 2010 242 A ...
Страница 284: ...DVC6200f Digital Valve Controller November 2010 272 D ...
Страница 290: ...DVC6200f Digital Valve Controller November 2010 278 E ...
Страница 308: ...DVC6200f Digital Valve Controller November 2010 296 F ...
Страница 312: ...DVC6200f Digital Valve Controller September 2010 300 Notes G Glossary ...
Страница 324: ...DVC6200f Digital Valve Controller November 2010 312 F Index ...
Страница 325: ...This page intentionally left blank ...