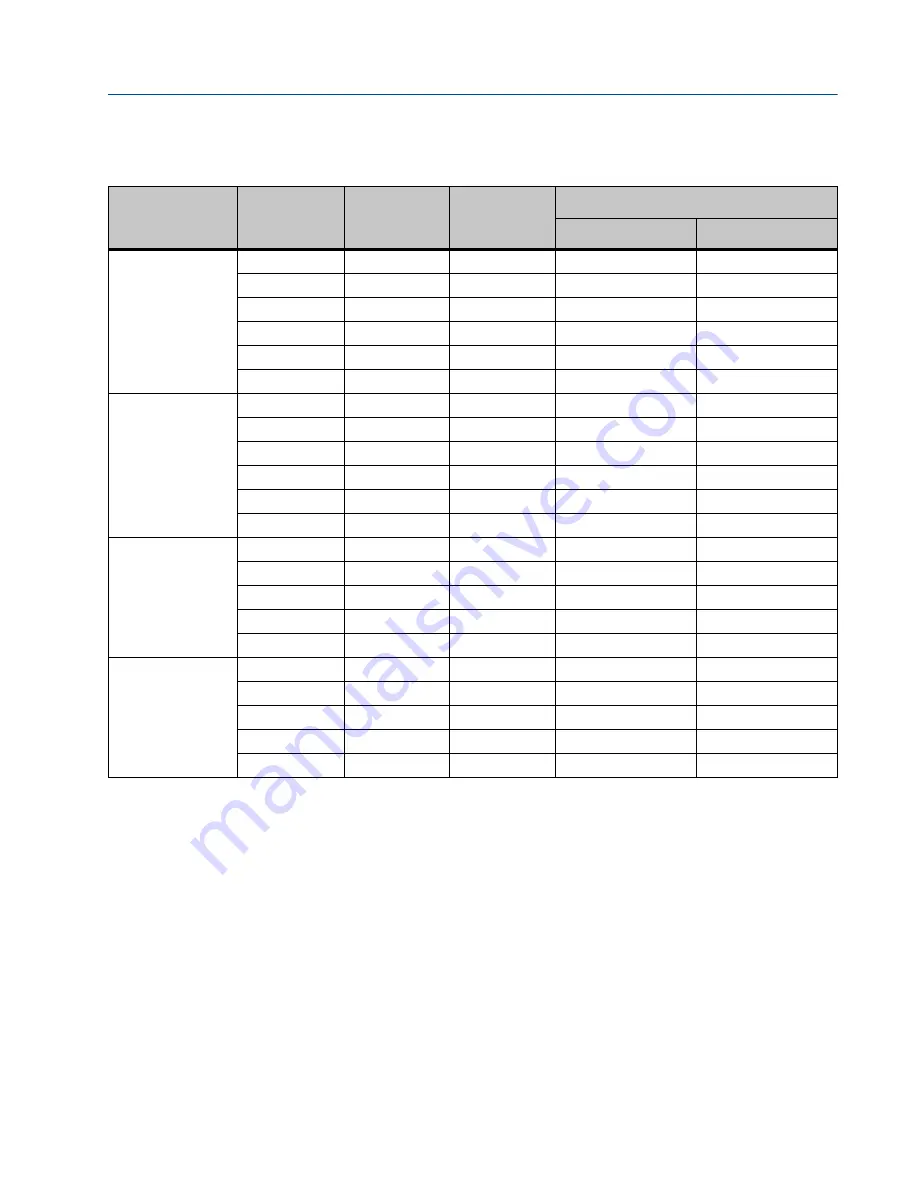
Owner and operator manual
Section 5: Supplemental information
3-9008-001 Rev M
January 2015
Joint assembly procedures
105
10
150
8
1/2”-13
75
95
300
8
1/2”-13
75
95
600
8
1/2”-13
75
95
900
8
5/8”-11
145
180
1500
20
5/8”-11
145
180
2500
28
5/8”-11
145
180
12
150
10
1/2”-13
75
95
300
10
1/2”-13
95
120
600
10
1/2”-13
95
120
900
10
5/8”-11
120
150
1500
20
5/8”-11
145
180
2500
28
5/8”-11
145
180
14
150
11
1/2”-13
75
95
300
11
1/2”-13
75
95
600
11
1/2”-13
95
120
900
22
5/8”-11
145
180
1500
22
5/8”-11
155
195
16
150
12
1/2”-13
75
95
300
12
1/2”-13
75
95
600
12
5/8”-11
145
180
900
28
5/8”-11
145
180
1500
28
5/8”-11
155
195
Table 5-3 Clamping bar screw (11) quantity and torque requirements
Nominal size (in.) ANSI Class
Number of
screws
Screw size
Required torque (ft. - lbs)
Minimum
Maximum
Содержание Daniel Senior Orifice Fitting Series
Страница 2: ......
Страница 12: ...xii List of Tables List of Tables Owner and operator manual January 2015 3 9008 001 Rev M ...
Страница 14: ...xiv List of Figures List of Figures Owner and operator manual January 2015 3 9008 001 Rev M ...
Страница 56: ...42 Orifice Plate Installation Section 2 Installation Owner and operator manual January 2015 3 9008 001 Rev M ...
Страница 137: ......