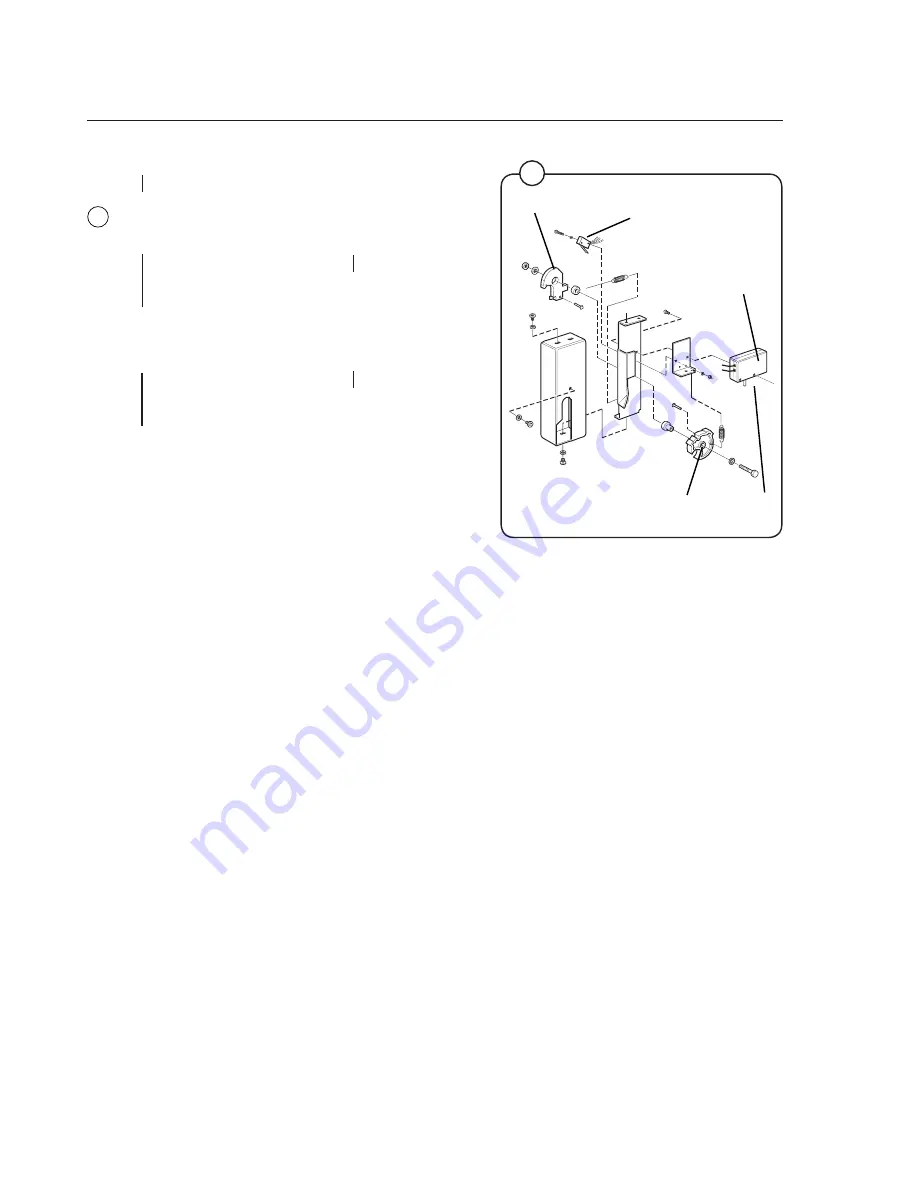
2
Troubleshooting
10
10
4128
Continued from previous page
4. Disassemble the door lock and verify the function of
S3 using an ohm meter.
Correct function
Incorrect function
Replace S.
5. Inspect the cabling between X5 and S3 using an ohm
meter.
Cabling OK
Incorrect cabling
Remedy or replace the
cables.
Inspect the mechanical function of the door lock.
Replace any defective components or replace the door
lock.
Switch cam
Microswitch S
Lock solenoid and
microswitch S4
Lock pin
Lock plate
Содержание W4400H
Страница 1: ...Service Manual W4400H W3600H W3850H W31100H Clarus Control 438 9206 51 06 22 ...
Страница 2: ......
Страница 6: ... ...
Страница 14: ...14 ...
Страница 18: ...18 ...
Страница 64: ...64 ...
Страница 72: ...72 ...
Страница 146: ...146 ...
Страница 164: ...164 ...
Страница 166: ...166 ...
Страница 185: ......
Страница 186: ...www electrolux com professional Share more of our thinking at www electrolux com ...