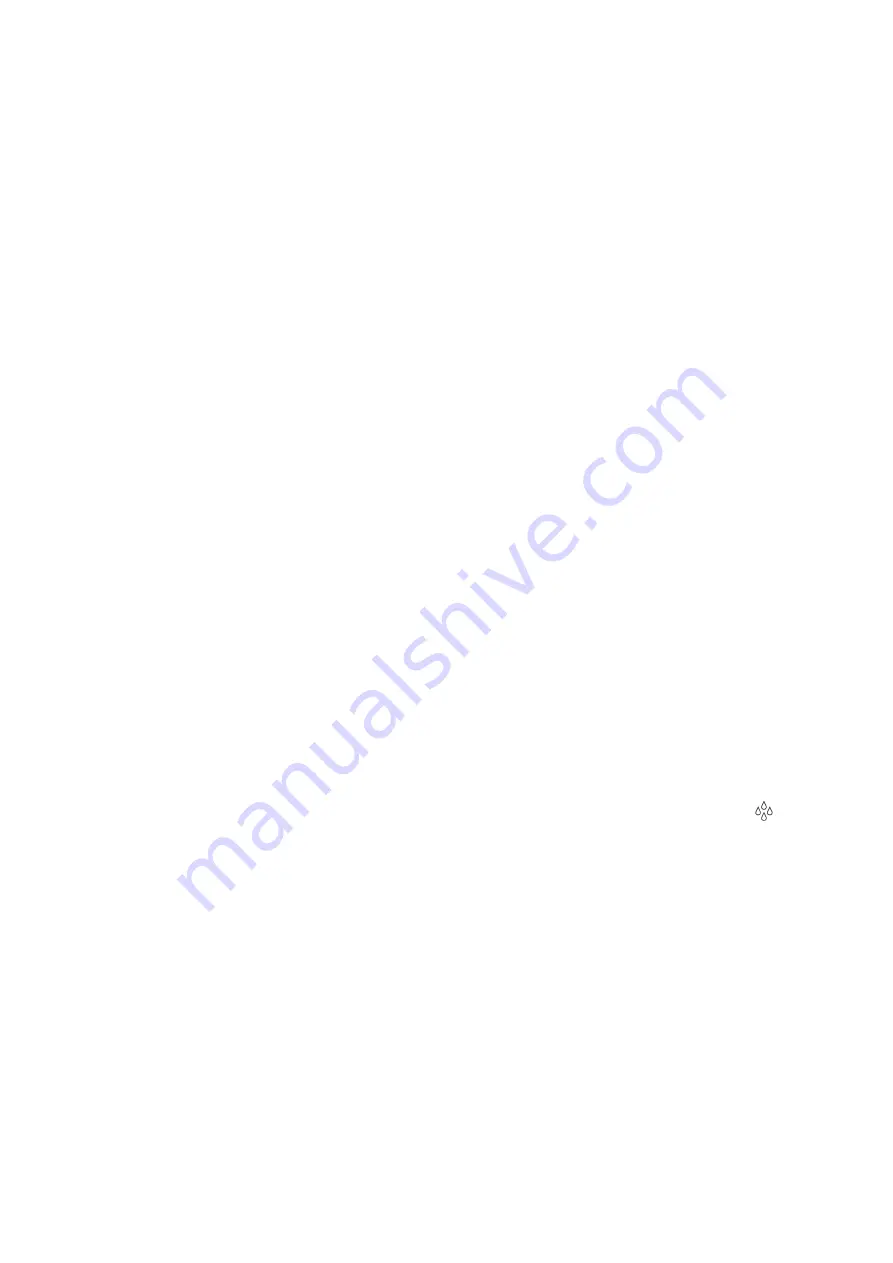
3.
If the oil is contaminated, drain and refill the pump with clean oil as described in
.
7.2.2 Replace the oil
Refer to
Figure: General view of the pump on page 12
:
1.
Operate the pump for approximately ten minutes to warm the oil, then switch off
the pump. This lowers the viscosity of the oil and enables it to be drained from the
pump more easily.
2.
Isolate the pump from the electrical supply and disconnect it from the vacuum
system.
3.
Remove the oil filler plug (4).
4.
Place a suitable block under the pump motor to tilt the pump and place a suitable
container under the oil drain plug (7). Remove the drain plug and allow the oil to
drain into the container.
5.
If the oil drained from the pump is contaminated, pour clean oil into the filler hole
and allow it to drain out of the pump. Repeat this step until the oil reservoir in the
pump has been thoroughly cleaned.
6.
Refit the drain plug, remove the block and reconnect the pump to the vacuum
system.
7.
Fill a suitable container with clean oil and pour the oil into the filler hole until the
oil level reaches the MAX level mark on the bezel of the oil level sight glass (6).
8.
Allow a few minutes for the oil to drain into the pump. If necessary, add more oil.
Refit the filler plug.
7.2.3 Decontaminate the oil
Refer to
Figure: General view of the pump on page 12
:
1.
Look at the condition of the oil in the oil level sight glass (6). If the oil is cloudy or
discoloured, continue with the procedure at Step 2 below.
2.
Close the vacuum system isolation valve.
3.
Turn the mode selector fully anticlockwise to select High Throughput mode . Set
the gas ballast control to low flow (position ‘I’).
4.
Operate the pump until the oil is clear.
7.2.4 Inspect and clean the inlet filter
Refer to
Figure: Inlet filter assembly on page 67
:
1.
Disconnect the vacuum system from the pump inlet port (3) and remove the
centring ring and filter assembly (1) and the O-ring (2). Inspect the centring ring
and the O-ring. If they are clean, continue at Step 5. If they are not clean, continue
at Step 2.
2.
Remove the O-ring from the centring ring and filter assembly. Do not allow the O-
ring to come into contact with the cleaning solution.
3.
Wash the centring ring and filter assembly in a suitable cleaning solution and allow
it to dry.
4.
If necessary, wipe the O-ring with a clean, dry, lint-free cloth.
Page 66
A65901880_D - Maintenance
Содержание nRVi
Страница 1: ...Rotary Vane Pumps nRVi INSTRUCTION MANUAL A65901880_D Original instructions edwardsvacuum com...
Страница 6: ...This page has been intentionally left blank...
Страница 97: ...Page 93 A65901880_D Service...
Страница 98: ...This page has been intentionally left blank...
Страница 99: ...This page has been intentionally left blank...
Страница 100: ...edwardsvacuum com...