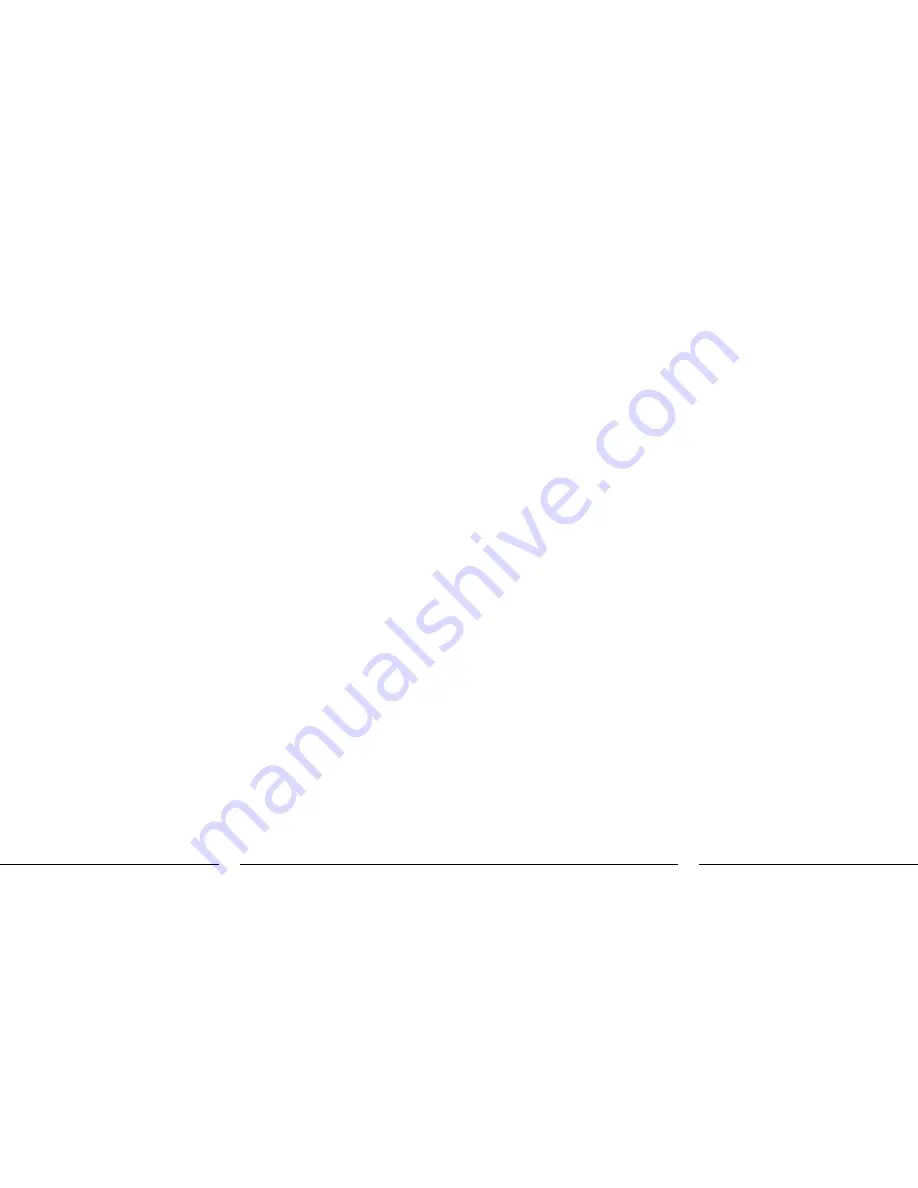
24
25
Initialization and Response Test
The following checklist includes the steps you must follow to ensure proper initialization and
operation of the gyro:
q
After connecting the flight battery to the ESC, be sure that you do not move or sway the
helicopter. Allow it to remain motionless until the red LED on the gyro illuminates solidly,
indicating that the gyro has initialized properly and is ready for use.
Note: It is extremely important that you do not move or sway the helicopter
after powering it on and before the gyro initializes. The gyro must be allowed
adequate time to record the neutral position in order to initialize for proper
operation. If you accidentally move the helicopter after powering it on and before
the gyro initializes, power the helicopter off (by disconnecting the flight battery
from the ESC) then repeat the process to power the helicopter on and to initialize
the gyro properly.
q
Once the gyro has initialized properly, we suggest setting the Throttle Hold (TH HOLD) switch
to the “On” (1) position for added safety during the response test.
q
Before making your first flight, it will be necessary to confirm that the gyro is responding
properly to the movements of the helicopter and providing proper inputs to the tail servo in
order to counteract any unwanted changes in yaw. To do this, view the servo arm (from the
top of the servo) and note the direction the arm rotates when you give a right rudder input on
the transmitter (while the model remains motionless). In the case of the DS75H servo installed
on your Blade 400 model, the servo arm should rotate toward the front of the helicopter.
Then, yaw the nose of the helicopter quickly to the left, while again noting the direction
the tail servo arm rotates. The arm should rotate in the same direction as it did for a right
rudder command (toward the front of the helicopter). If the servo arm rotates in the opposite
direction, switch the position of the Reverse switch located on the side of the gyro. The switch
should be set to the Normal (NOR) position. Then, repeat the steps above to confirm that the
gyro is now providing proper inputs to the tail servo.
q
After confirming that the gyro is providing proper inputs to the tail servo, power off the helicopter
and be sure to review the following sections of the manual BEFORE proceeding with the first
flight.
Gyro Mode and Gain Adjustments:
• The G110 offers a Dual Remote Gain Adjustment feature. This, along with the DX6i’s Gyro
Sensitivity feature, allows the gyro mode (Standard Rate or Heading Lock) and gain values to
be set remotely in the transmitter. This means that the Gain Setting Adjustment Pot located on the
gyro itself will not be active and will not be used for adjusting gain values.
• The gain values for the gyro are adjusted in the Gyro Sensitivity (GYRO) menu of the transmitter.
And because the switch (SW) selection choice has been set to the Gyro (GYRO) switch, the two
available gain values can be selected using this switch during flight. When the Gyro switch is
toggled in the upward (0) position, the gain value will be equivalent to the Rate (RATE) set on the
first (0:) line. When the Gyro switch is toggled in the downward (1) position, the gain value will
be equivalent to the Rate (RATE) set on the second (1:) line. Please see the manual for the DX6i for
any additional information you may require.
• When the Rate for either Gyro switch position is set to 0%, it is equivalent to an approximately
100% gain value in the Standard Rate (non-Heading Lock) mode.
When the Rate for either Gyro switch position is set to 25%, it is equivalent to an approximately
50% gain value in the Standard Rate (non-Heading Lock) mode.
When the Rate for either Gyro switch position is set to 50%, it is equivalent to an approximately
0% gain value in the Standard Rate (non-Heading Lock) mode.
• When the Rate for either Gyro switch position is set to 75%, it is equivalent to an approximately
50% gain value in the Heading Lock mode.
When the Rate for either Gyro switch position is set to 100%, it is equivalent to an approximately
100% gain value in the Heading Lock mode.
In the case of the Blade 400 3D, it is generally preferred to fly with the gyro set to the Heading
Lock mode. This means that the Rate for either Gyro switch position should not typically be set to
below approximately 60% (an approximately 20% gain value in the Heading Lock mode).
• While you can set and select between two different Modes and Rates using the Gyro switch,
two slightly different Rates have been set for the same Mode (Heading Lock) from the factory.
The Rate/value is slightly higher when the Gyro switch is set in the upward (0) position than it
is in the downward (1) position. After your first few flights you can experiment with different
values in each position to find the values that work best depending on your flying style and
flying conditions. For example, it may be desirable to use a higher gain value when flying in the
Normal flight mode, and/or a lower gain value when flying in windy conditions. The DX6i also
allows you the option to set gain values for each specific flight mode. This can be accomplished
by setting the gyro switch (SW) selection to Flight Mode (F. MODE) (please see the manual for the
DX6i for more information.)
• During your first flight, establish a stable hover and apply some short and quick rudder inputs
while observing the reaction of the tail when the control stick is returned to its neutral position. If
there is any tendency for the tail to twitch quickly (oscillate) from side to side, it will be necessary
to lower the Rate used for the selected Gyro switch position.
The goal when adjusting the Rate for one or both of the Gyro switch positions is to find the highest
gyro gain value (Rate) at which the tail of the helicopter will not oscillate in nearly all areas of
flight, including fast forward flight and descents. In some cases it may not be possible to use
the same Rate for hovering (in the Normal flight mode for example) and fast forward flight/
aerobatics (in the Stunt flight mode for example). By setting two different Rates for each Gyro
switch position, it will allow you to select the best Rate (using the Gyro switch) depending on the
flight mode you are using and the type of flying you are doing at any given time. This can be
particularly helpful when flying in windy conditions, as it may sometimes be necessary to switch to
a lower Rate in flight to prevent significant tail oscillation when performing certain maneuvers.
Trim Adjustments
• During flight, it may be necessary to make some small adjustments to the rudder trim in order to
prevent the nose/tail of the model from “drifting” to the left or right when the rudder stick is in the
neutral position. Typically, only a small amount of adjustment may be necessary.
Note: It is always best to avoid sudden temperature and environmental condition changes
when using a gyro. For example, it is best to not fly a model on a very hot (or cold) day
immediately after removing it from an air-conditioned (or heated) vehicle. It is also best to keep
the gyro out of direct sunlight and away from any heat-generating sources on the model.
To help the gyro better acclimate to temperature and environmental conditions at the flying field,
it is best to let your Blade 400 3D model stand for approximately 10–15 minutes before flying,
allowing the temperature of the gyro sensor to stabilize. If you do not allow the temperature to
stabilize, you may experience radical trim changes that require significant adjustments of the
rudder trim during flight.
Содержание Blade 400 3D
Страница 24: ...46 47 NOTES NOTES ...