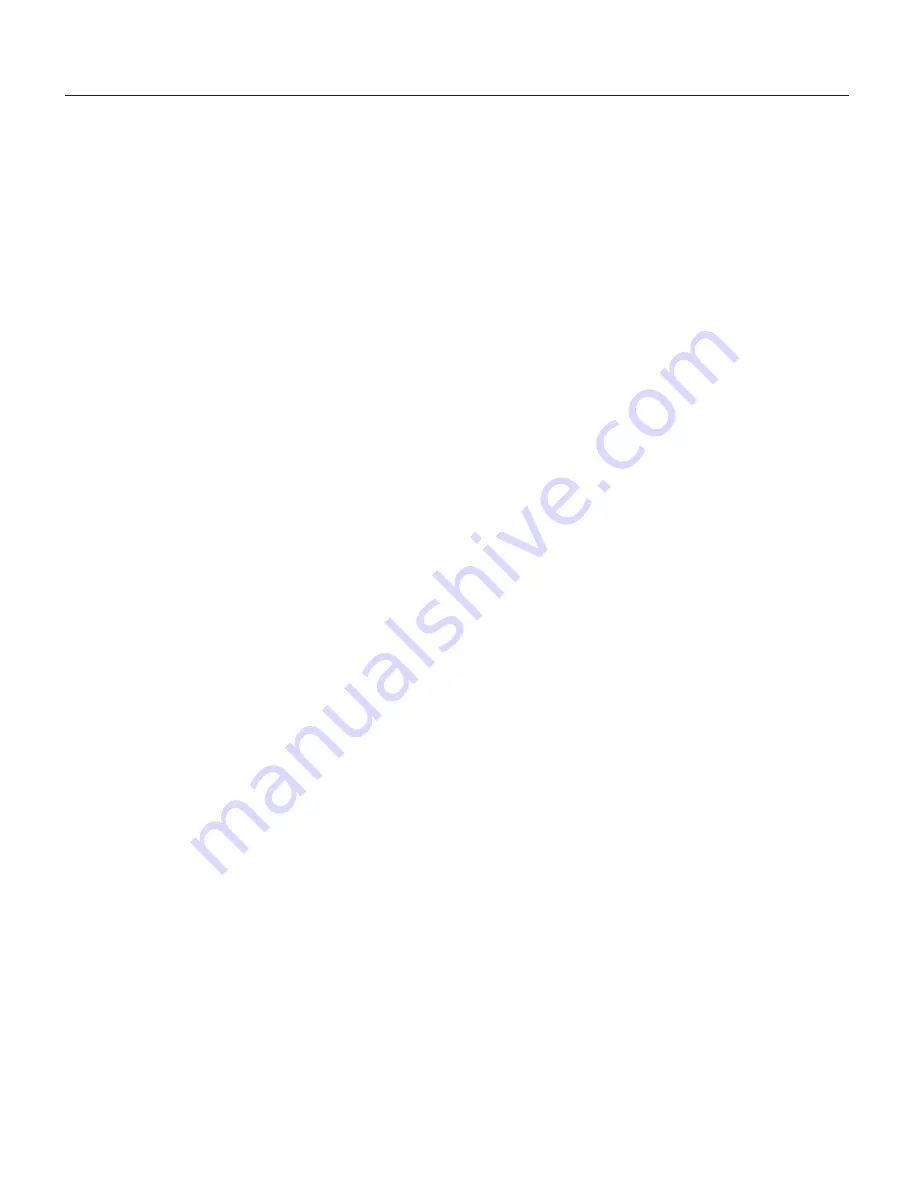
16
response. It is capable of estimating the process parameters with high precision.
2. ADAPTIVE ALGORITHM
In order to implement the adaptive algorithm, the instrument should be in automatic mode. Then
change SMART to ON. In this case the ON will be remembered by the instrument even if the
instrument was switched off.
In order to deactivate the adaptive processes, return the SMART parameter to OFF.
The ADAPTIVE is an on-line algorithm that “observes” the measured value and looks for oscillation
due to a variation of the load or the set point. When a significant pattern is “recognized,” the
decision procedure starts to recalculate the PID parameters of the controller. While the ADAPTIVE
procedure is enabled the PID parameters can only be monitored.
AUTOMATIC STAND-BY: This function avoids overshoot due to temporary process interruptions (PV
goes to zero).
In cases where the main input goes to zero, the controller output quickly reaches the saturation for
integral factor effect; when the process restarts, the controlled output will have an excessive and
dangerous overshoot, (i.e. it will start at full speed).
When the Automatic Stand-By function is activated, the algorithm monitors the controller input and
output: when the input value goes lower than a threshold (specified by the Automatic Stand-By
Pressure Low Limit parameter). When this happens, and the output value reaches the saturation
condition and the control output saves the last value stored when the process was stable.
This freezing of the output of the controller will last for the time specified by the Automatic Stand-By
Recovery Time parameter. If the input does not recover within the specified time, the output value is
forced to zero. If the controller input recovers within the specified time, the algorithm waits for two
and one half times the integral value; after this time has elapsed, the controller will come back
automatically to normal running condition to the output level calculated when the process was
stable.
2.13
C
ONTROL
AND
R
ETRANSMISSION
O
UTPUTS
C
OMMON
S
PECIFICATION
The ATC770 Pressure/Process controller has four digital inputs that can switch between Manual and
Automatic control (DIG1), increase (DIG2) or decrease (DIG3) the control output value and switch
from Automatic to Manual while setting the control output to zero (DIG4).
Digital Input 1 (DIG1) is available at all times. It acts as an Auto/Manual Switch. In the closed
position the Manual mode is accessed. In the open position the Automatic mode is
accessed.
Digital Input 2 (DIG2) is available only when the Group 1 function
A/M is changed from LoCAL to
Содержание ATC770
Страница 19: ...ATC770 Microprocessor Based Pressure Process Controller 19 Fig 2 ATC770 Outline Drawing...
Страница 23: ......
Страница 30: ...30 Fig 6 Remote Set Point Jumper Location Board E...
Страница 84: ...NOTES...
Страница 85: ...NOTES...
Страница 86: ...NOTES...
Страница 88: ...DYNISCO INSTRUMENTS 38 FORGE PARKWAY FRANKLIN MA 02038 ATTN MARKETING DEPT Place Stamp Here...