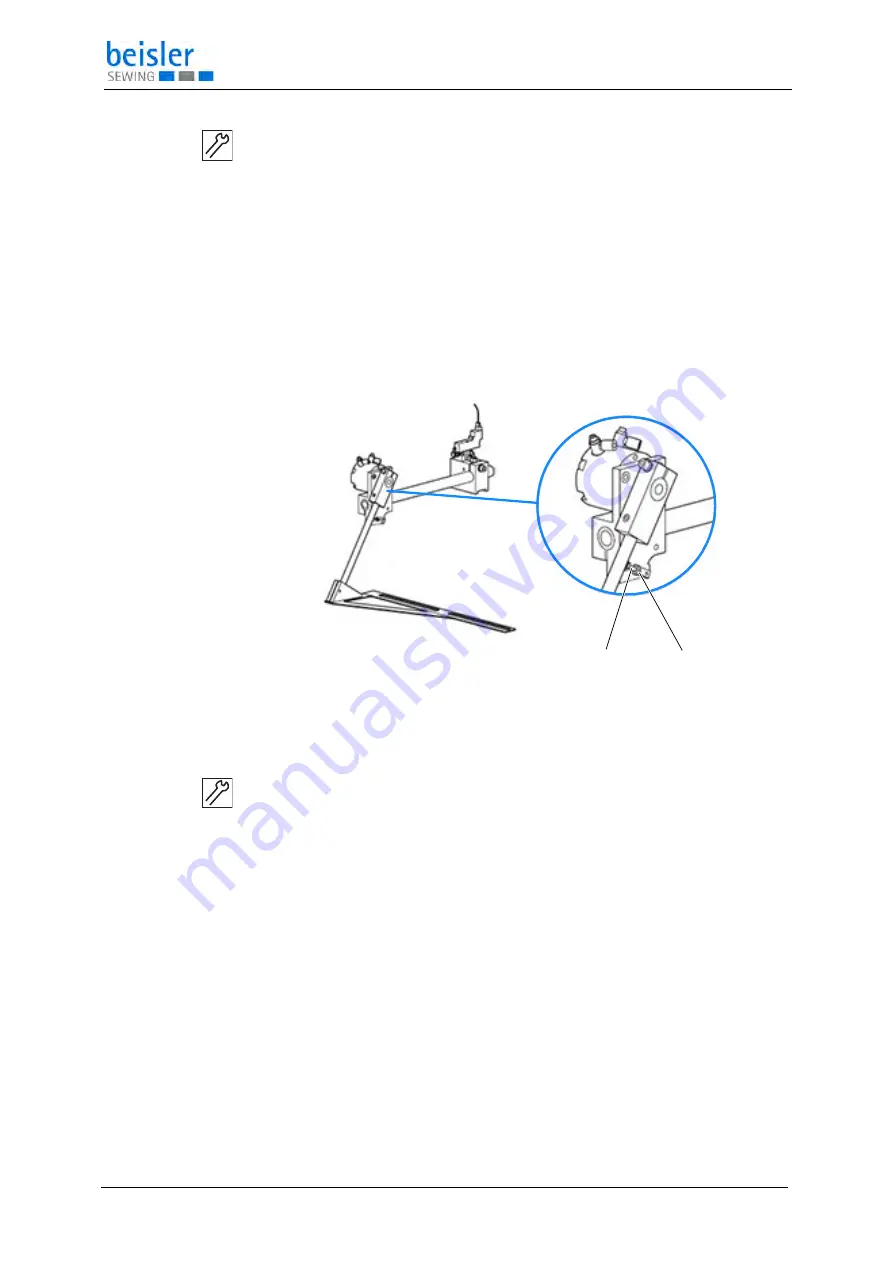
Setting up the machine
30
Service Instructions 2112-5 - 00.0 - 02/2020
To adjust the lower position of the folder:
1. Loosen the counternut (3).
2. Turn the screw (4) at the revolver (1) into position.
3. Check the distance of the folder (5) to the clamp rail (6).
The folder lowers onto the work surface to the left of the clamp slide
without any friction contact.
4. Tighten the counternut (3).
7.5 Aligning the stop for the right fly piece
Fig. 18: Aligning the stop for the right fly piece
The position of the stop determines the line-up position of the right fly
piece on the right trouser component.
To adjust the stop for the right fly piece:
1. Loosen the counternut (2).
2. Turn the screw (1).
3. Tighten the counternut (2).
(1)
- Screw
(2)
- Counternut
①
②
Содержание beisler 2112-5
Страница 1: ...Service Instructions...
Страница 8: ...About these instructions 6 Service Instructions 2112 5 00 0 02 2020...
Страница 40: ...Setting up the machine 38 Service Instructions 2112 5 00 0 02 2020...
Страница 76: ...Programming 74 Service Instructions 2112 5 00 0 02 2020...
Страница 84: ...Maintenance 82 Service Instructions 2112 5 00 0 02 2020...
Страница 86: ...Decommissioning 84 Service Instructions 2112 5 00 0 02 2020...
Страница 88: ...Disposal 86 Service Instructions 2112 5 00 0 02 2020...
Страница 96: ...Technical data 94 Service Instructions 2112 5 00 0 02 2020...
Страница 103: ......