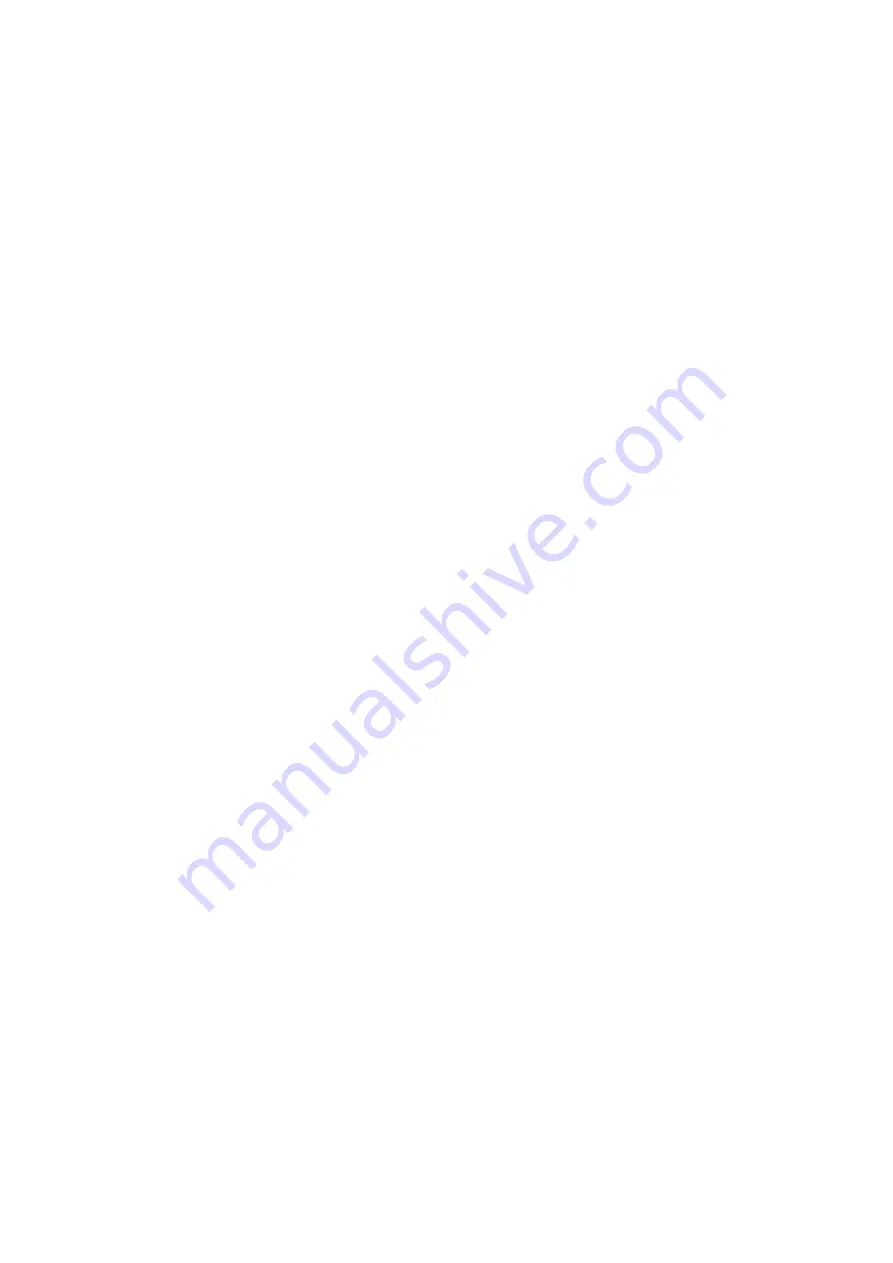
1-42 Safety
022-00029AE Operation and Maintenance Manual
SHIPPING AND TRANSPORTATION
OBEY STATE AND LOCAL OVER-THE-ROAD REGULATIONS
Check state and local restrictions regarding weight, width and length of a load before making any other
preparation for transport.
Hauling vehicle, trailer and load must all be in compliance with local regulations governing intended
shipping route.
Partial disassembly or tear-down of wheel loader may be necessary to meet travel restrictions or particular
conditions at job site.
Refer to “Transportation” on page 5-1, of this Operation and Maintenance Manual for information on
loading and unloading.