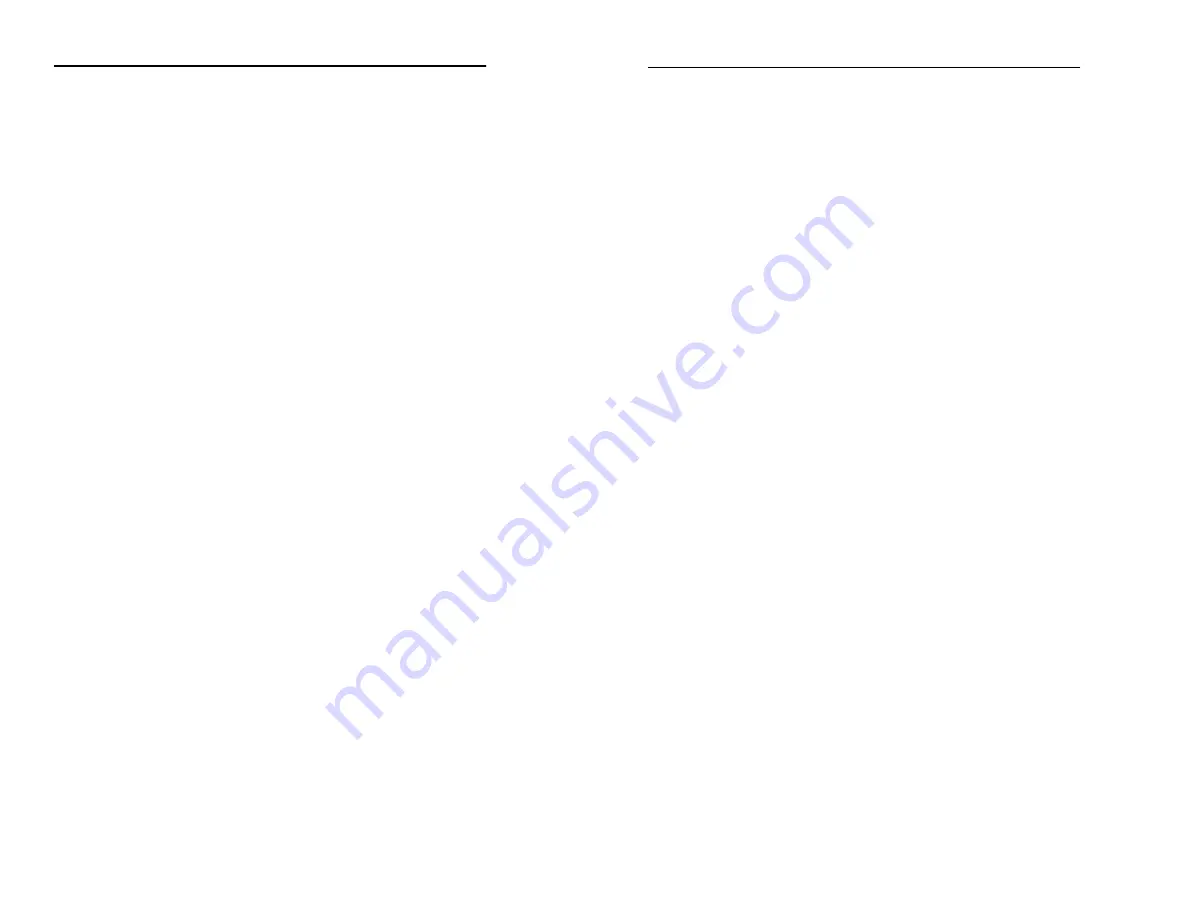
78
JT920/JT920L - SETUP
ASSEMBLE ELECTRIC STRIKE SYSTEM
78
JT920/JT920L - SETUP
ASSEMBLE ELECTRIC STRIKE SYSTEM
ASSEMBLE ELECTRIC STRIKE SYSTEM
Anytime drilling unit is used in an electric jobsite, electric strike
system must be properly set up, tested, and used. In addition to
ESID control module, strike system includes bonding cables,
barriers and protective boots and gloves. Boots and gloves must
meet the following standards:
•
Wear high-top boots with legs of pants tucked completely
inside. Boots must meet the electric hazard protection
requirements of ANSI Z-41, 1991, when tested at 14,000
volts.
•
Gloves must have 17,000 AC maximum use voltage,
according to ASTM specification D120-87.
If working around higher voltage, use gloves and boots with
appropriately higher ratings.
NOTICE:
The strike system does not prevent electric strikes or
detect strikes before they occur.
If alarms are activated, a strike
has already occurred
and equipment is electrified.
Read and follow directions in
SAFETY
. Review safety
procedures before each job.
FCC Statement
The Electric Strike System has been tested and found to comply with the limits for
a Class A digital device, pursuant to Part 15 of the FCC rules. These limits are
designed to provide reasonable protection against harmful interference when the
equipment is operated in a commercial environment. This equipment generates,
uses and can radiate radio frequency energy and, if not installed and used in
accordance with the instructions, can cause harmful interference to radio
communications. Operation of this equipment in a residential area could cause
harmful interference which the user will be required to correct at his own expense.
Changes or modifications not expressly approved in writing by The Charles
Machine Works, Inc. may void the user's authority to operate this equipment.
ASSEMBLE ELECTRIC STRIKE SYSTEM
Anytime drilling unit is used in an electric jobsite, electric strike
system must be properly set up, tested, and used. In addition to
ESID control module, strike system includes bonding cables,
barriers and protective boots and gloves. Boots and gloves must
meet the following standards:
•
Wear high-top boots with legs of pants tucked completely
inside. Boots must meet the electric hazard protection
requirements of ANSI Z-41, 1991, when tested at 14,000
volts.
•
Gloves must have 17,000 AC maximum use voltage,
according to ASTM specification D120-87.
If working around higher voltage, use gloves and boots with
appropriately higher ratings.
NOTICE:
The strike system does not prevent electric strikes or
detect strikes before they occur.
If alarms are activated, a strike
has already occurred
and equipment is electrified.
Read and follow directions in
SAFETY
. Review safety
procedures before each job.
FCC Statement
The Electric Strike System has been tested and found to comply with the limits for
a Class A digital device, pursuant to Part 15 of the FCC rules. These limits are
designed to provide reasonable protection against harmful interference when the
equipment is operated in a commercial environment. This equipment generates,
uses and can radiate radio frequency energy and, if not installed and used in
accordance with the instructions, can cause harmful interference to radio
communications. Operation of this equipment in a residential area could cause
harmful interference which the user will be required to correct at his own expense.
Changes or modifications not expressly approved in writing by The Charles
Machine Works, Inc. may void the user's authority to operate this equipment.
Содержание JT920
Страница 54: ...54 JT920 JT920L SAFETY SAFETY ALERTS 54 JT920 JT920L SAFETY SAFETY ALERTS...
Страница 68: ...68 JT920 JT920L PREPARATION 68 JT920 JT920L PREPARATION...
Страница 75: ...JT920 JT920L TRANSPORTATION 75 TOW JT920 JT920L TRANSPORTATION 75 TOW...
Страница 76: ...76 JT920 JT920L TRANSPORTATION TOW 76 JT920 JT920L TRANSPORTATION TOW...
Страница 128: ...128 JT920 JT920L LUBRICATION DRILLING FLUID PUMP 128 JT920 JT920L LUBRICATION DRILLING FLUID PUMP...
Страница 167: ......
Страница 168: ......
Страница 169: ...JT920 JT920L 169 JT920 JT920L 169...