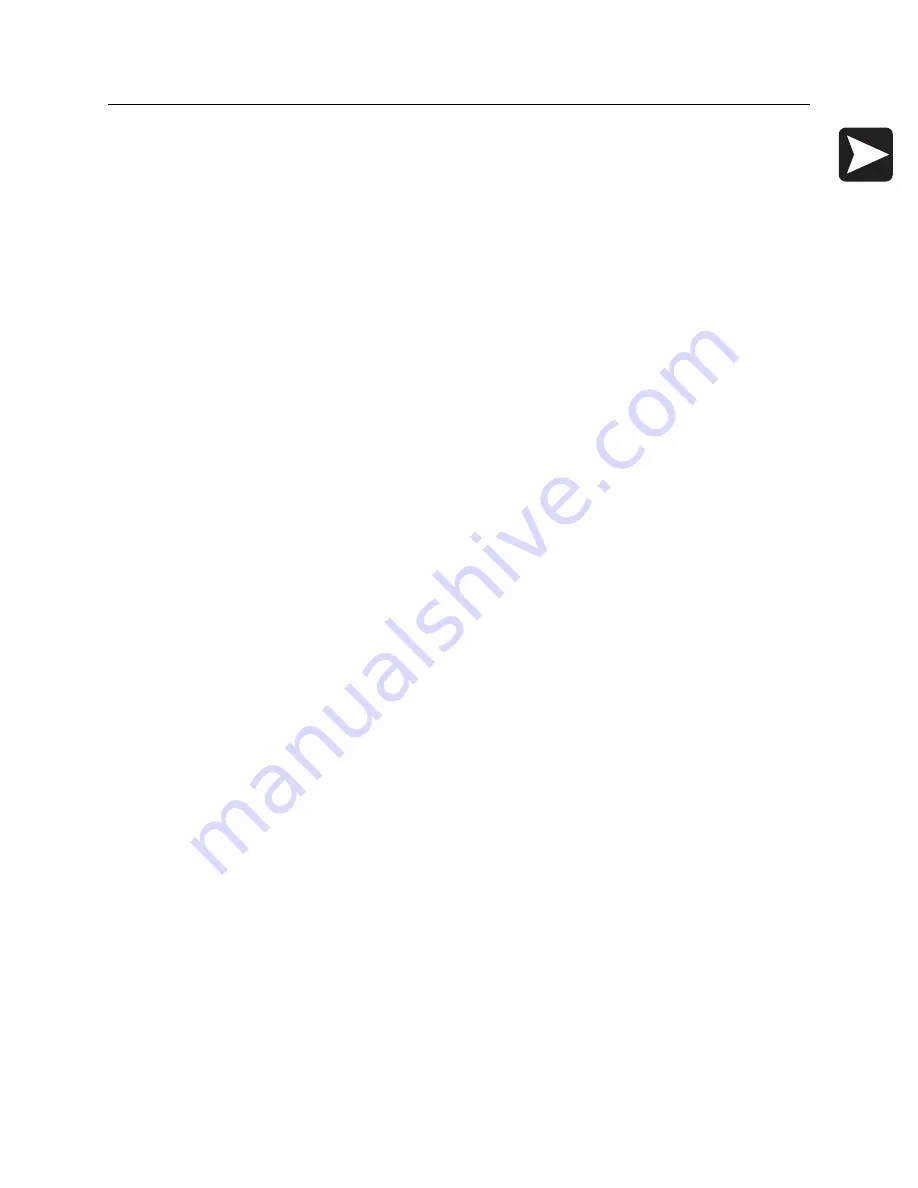
JT1220 Mach 1 Operator’s Manual
Foreword - 5
CMW
Foreword
This manual is an important part of your equipment. It provides safety information and operation
instructions to help you use and maintain your Ditch Witch equipment.
Read this manual before using your equipment. Keep it with the equipment at all times for future reference.
If you sell your equipment, be sure to give this manual to the new owner.
If you need a replacement copy, contact your Ditch Witch dealer. If you need assistance in locating a
dealer, visit our website at www.ditchwitch.com or write to the following address:
The Charles Machine Works, Inc.
Attn: Marketing Department
PO Box 66
Perry, OK 73077-0066
USA
The descriptions and specifications in this manual are subject to change without notice. The Charles
Machine Works, Inc. reserves the right to improve equipment. Some product improvements may have
taken place after this manual was published. For the latest information on Ditch Witch equipment, see your
Ditch Witch dealer.
Thank you for buying and using Ditch Witch equipment.
Содержание JT1220 Mach 1
Страница 1: ...JT1220 Mach 1 Issue 2 1 Operator s Manual 054 114 CMW...
Страница 19: ...Safety 18 JT1220 Mach 1 Operator s Manual Emergency Procedures CMW...
Страница 75: ...Prepare 74 JT1220 Mach 1 Operator s Manual Check Supplies and Prepare Equipment CMW...
Страница 107: ...Conduct a Bore 106 JT1220 Mach 1 Operator s Manual Remove Pullback Device CMW...