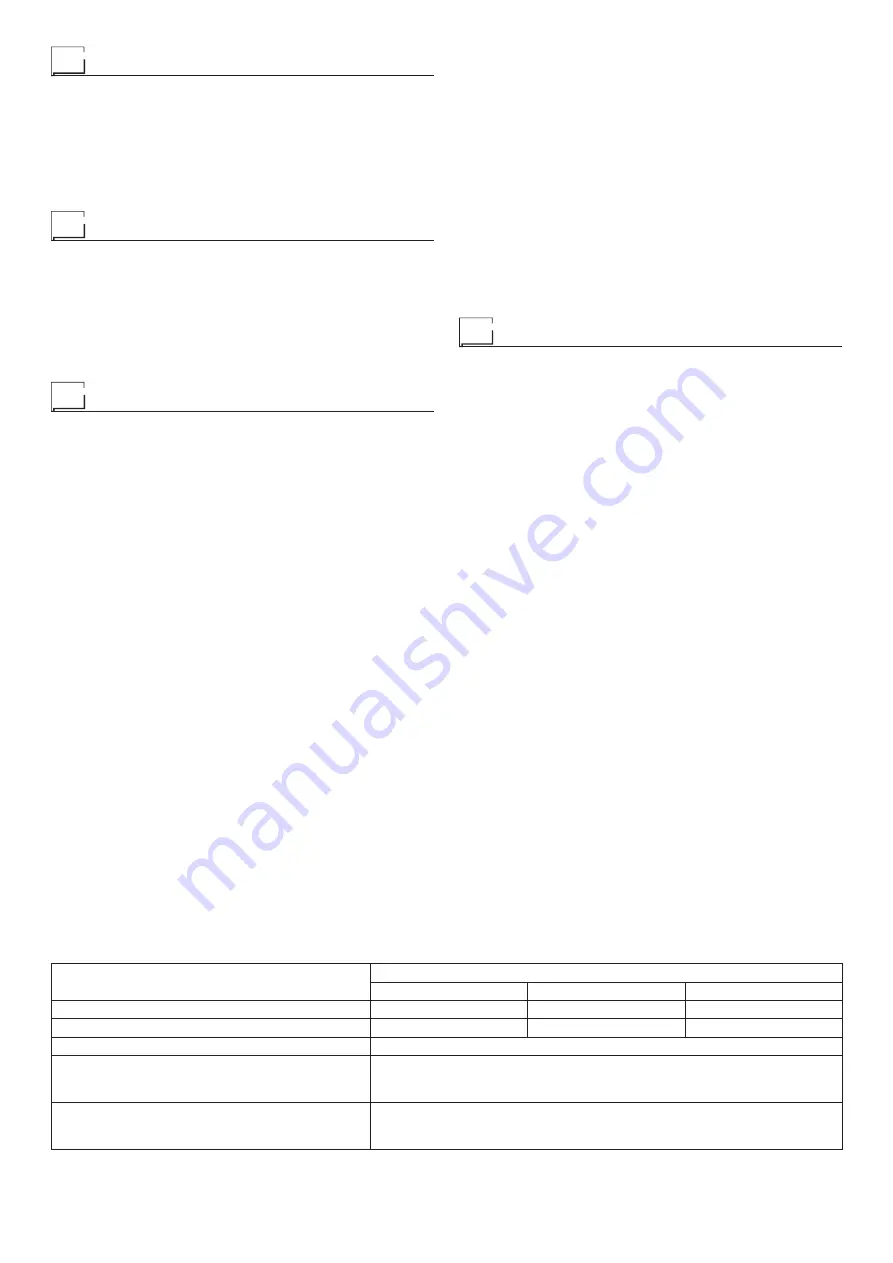
4
How to lift up the system
Strap the system safely and securely in the slings working from
the bottom, then lift up from the ground.
This welding power source has a robust handle built into the
frame for moving the welding power source.
NOTE: These hoisting and transportation devices conform to
European standards. Do not use other hoisting and transpor-
tation systems.
Opening the packaging
Perform the following operations on receiving the welding pow-
er source:
•
Remove the welding power source and all accessories and
components from the packaging.
•
Check that the welding power source is in good condition;
otherwise immediately inform the retailer or distributor.
•
Check that all the ventilation grilles are open and that there
is nothing to obstruct the correct air flow.
Installation and connections
The installation site for the system must be carefully chosen
in order to ensure its satisfactory and safe use. The user is re-
sponsible for the installation and use of the system in accord-
ance with the producer’s instructions contained in this manual.
Before installing the system the user must take into consider-
ation the potential electromagnetic problems in the work area.
In particular, we suggest that you should avoid installing the
system close to:
•
Signalling, control and telephone cables.
•
Radio and television transmitters and receivers.
•
Computers and control and measurement instruments.
•
Security and protection instruments.
Persons fitted with pace-makers, hearing aids and similar weld-
ing power source must consult their doctor before going near a
welding power source in operation. The welding power source’s
installation environment must comply to the protection level of
the frame.
The welding unit is characterized by the following classes:
•
IP 23 S protection class indicates that the welding power
source can be used in both interior and exterior environ-
ments.
•
The “S” usage class indicates that the welding power source
can be employed in environments with a high risk of electri-
cal shocks.
This system is cooled by means of the forced circulation of air,
and must therefore be placed in such a way that the air may
be easily sucked in and expelled through the apertures made
in the frame.
Assemble the system in the following way:
•
Assemble the trolley.
•
Fixing the cooling unit to the trolley.
•
Fixing of the welding power source to the trolley and the cool-
ing unit (electrical and plumbing connections).
•
Connect up the welding power source to the mains.
•
Connect up the wire-feeder/generator interconnection cable.
•
Connect up the welding cables.
Instructions for fitting the individual components / optional ex-
tras are contained in the relevant packaging.
Connection to the electrical supply
Connection of the welding power source to the user line
(electrical current) must be performed by qualified per-
sonnel.
Before connecting the welding power source to the mains
power supply, make sure that rated voltage and frequen-
cy correspond to those provided by the mains power sup-
ply and that the welding power source’s power switch is
turned to “O”.
Use the welding power source’s own plug to connect it up to
the main power supply. Proceed as follows if you have to re-
place the plug:
•
3 conducting wires are needed for connecting the welding
power source to the supply.
•
The fourth, which is YELLOW GREEN in colour is used for
making the “GROUND” connection.
Before connecting the welding power source to the mains
power supply, make sure that rated voltage and frequen-
cy correspond to those provided by the mains power sup-
ply and that the welding power source’s power switch is
turned to “O”.
Table 2 shows the capacity values that are recommended for
fuses in the line with delays.
NOTE: Any extensions to the power cable must be of a suita-
ble diameter, and absolutely not of a smaller diameter than the
special cable supplied with the welding power source.
Table 2
Model
DIX PI GO 2006.M / DIX PI GO 2006.M Puls
MIG/MAG
TIG
MMA
Power input (I
2
Max)
kVA
10
8,5
11
Delayed fuse (I
eff)
A
16
10
16
Duty cycle @ 35% (40°C)
A
250
Mains cable
Length
Section
m
mm
2
4
2,5
Ground cable
Length
Section
m
mm
2
3 - 4
35
Содержание DIX PI GO 2006.M
Страница 13: ...13 2101AC73...