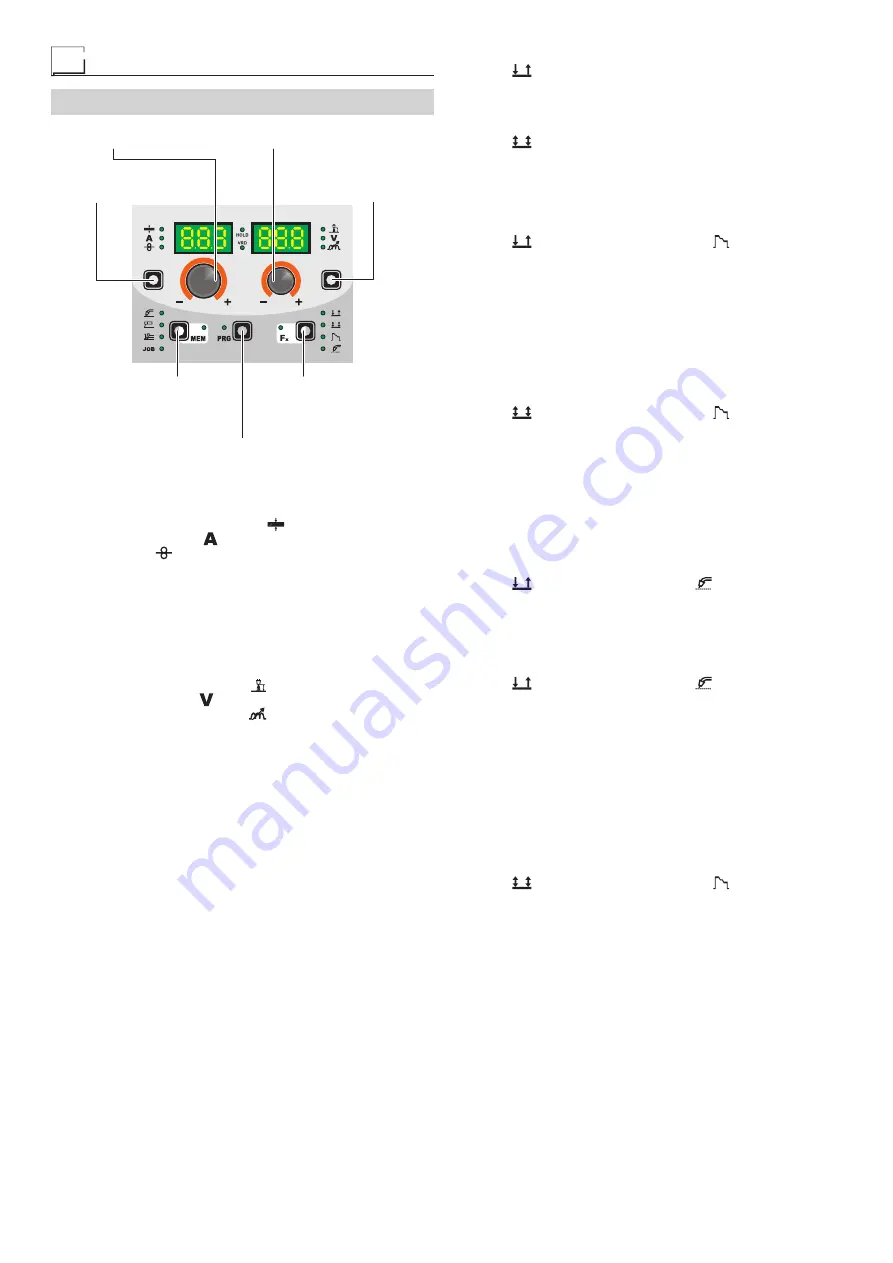
15
Control panel
KEY AND KNOB COMMANDS
▪
ENCODER knob - V
▪
WELDING MODE
SELECTION key
▪
SPECIAL FUNCTIONS
key “Fx”
▪
PROGRAMME SELECTION key
▪
SET-UP MENU Key
▪
ENCODER knob - A
▪
WELDING PROCESS
SELECTION key
▪
SAVE “MEM” key
▪
PARAMETER
SELECTION key - A
▪
PARAMETER
SELECTION key - V
■
PARAMETER SELECTION key - A
This is used to select the following welding parameters:
•
THICKNESS OF WELDED ITEM (
).
•
WELDING CURRENT (
).
•
WIRE SPEED (
).
■
ENCODER knob - A
This is used to set and edit the PARAMETERS - A based on the
corresponding LED switched on and the value highlighted on the
DISPLAY PARAMETERS - A display, required for correct function-
ing of the machine.
■
PARAMETER SELECTION key - V
This is used to select the following welding parameters:
•
ARC LENGTH ADJUSTMENT (
).
•
WELDING VOLTAGE (
).
•
ELECTRONIC INDUCTANCE (
).
■
ENCODER knob - V
This is used to set and edit the PARAMETERS - V based on the
corresponding LED switched on and the value highlighted on the
DISPLAY PARAMETERS - V display, required for correct function-
ing of the machine.
■
PROGRAMME SELECTION key
It can be used to select the individual welding PROGRAM for MIG-
MAG and MMA welding processes.
■
SET-UP MENU Key (T > 3 s)
This provides access to the SET-UP menu, which in turn provides
access to a series of functions, suitable for an expert operator.
■
WELDING PROCESS SELECTION key
It can also be used to select the following welding processes:
•
MIG-MAG / PULSED MIG / Double PULSED MIG.
•
MMA.
•
TIG.
•
JOB.
■ SAVE “MEM” key (T ≥ 2 s)
It allows the saving of the parameters in the JOB.
It also allows one to view / change the parameters previously saved
in the JOB.
WARNING: No LED switches on when this key is activated!
■
WELDING MODE SELECTION key
This is used to select the following welding modes (only for MIG
welding processes) and each time the key is pushed the welding
machine moves on to select the next welding mode in the follow-
ing order:
TWO STROKE (2T)
2T LED (
) switched on
Pressing the TORCH TRIGGER starts the welding cycle, which
will stop when it is released.
FOUR STROKE (4T)
4T LED (
) switched on
1) Pressing and releasing the TORCH TRIGGER will start the
welding cycle.
2) Pressing and releasing the TORCH TRIGGER will start the
welding cycle.
CRATER 2T
2T LED (
) switched on - CRATER LED (
) switched on
1) When the TORCH TRIGGER is pushed the arc ignites and the
parameters assume the values for the “initial crater” for a time
set by means of the CRATER START TIME (F10) function.
After that the parameter values become those for “welding” for
a time defined by the CRATER START SLOPE (F11) function.
2) When the TORCH TRIGGER is released the parameters take
on the “final crater” values for a time set by means of the CRA-
TER END TIME (F15) function, for a period of time set using
the CRATER END SLOPE (F12) function.
CRATER 4T
4T LED (
) switched on - CRATER LED (
) switched on
1) When the TORCH TRIGGER is pushed the arc ignites and the
parameters assume the values for the “initial crater”.
2) When the TORCH TRIGGER is released the parameters
take on the “welding” values for a time set using the CRATER
START SLOPE (F11) function.
3) When the TORCH TRIGGER is pushed again the parameters
take on the “final crater” values for a time defined using the
CRATER END SLOPE (F12) function.
4) Releasing the TORCH TRIGGER will end the welding cycle.
SPOT WELDING 2T
2T LED (
) switched on - SPOT LED (
) switched on
This is used so that on pressing the TORCH TRIGGER spot weld-
ing is done for a time period set beforehand (in seconds), after
which the arc switches off automatically (SPOT WELD TIME F07
function).
STITCH WELDING 2T
2T LED (
) switched on - SPOT LED (
) flashing
To begin stitch welding:
1) Press the TORCH TRIGGER to start the welding current and
wire feed.
At this point the welder will perform automatically a succession
of a welded tracts followed by a pause, respecting the times
set in the functions STITCH WELD TIME (F05) and STITCH
WELD PAUSE (F06).
This procedure stops automatically only when the TORCH
TRIGGER is released.
2) When the TORCH TRIGGER is pushed again the torch be-
gins a new interval welding cycle.
SWITCH
4T LED (
) switched on - CRATER LED (
) flashing
1) When the TORCH BUTTON is pushed, the arc is ignited and
the welding parameters take on the values for the
initial cra-
ter
.
2) When the TORCH BUTTON is released, the current goes to
that for
welding
at a time defined by the CRATER START
SLOPE function (F11).
3) When the TORCH BUTTON is pressed and released within
1 second, the current goes to that defined by the (F19) and
(F20) “SWITCH” functions. By repeating this operation, you
can switch an infinite number of times between the
cycle
lev-
el and
welding
level.
4) When the TORCH BUTTON is pushed again and held down
for more than 1 second, after a time defined by the CRATER
END SLOPE (F12) function, the welding parameters taken on
the values for the
final crater
. When the TORCH BUTTON is
released the welding cycle ends.
Содержание DIX PI GO 2006.M
Страница 13: ...13 2101AC73...