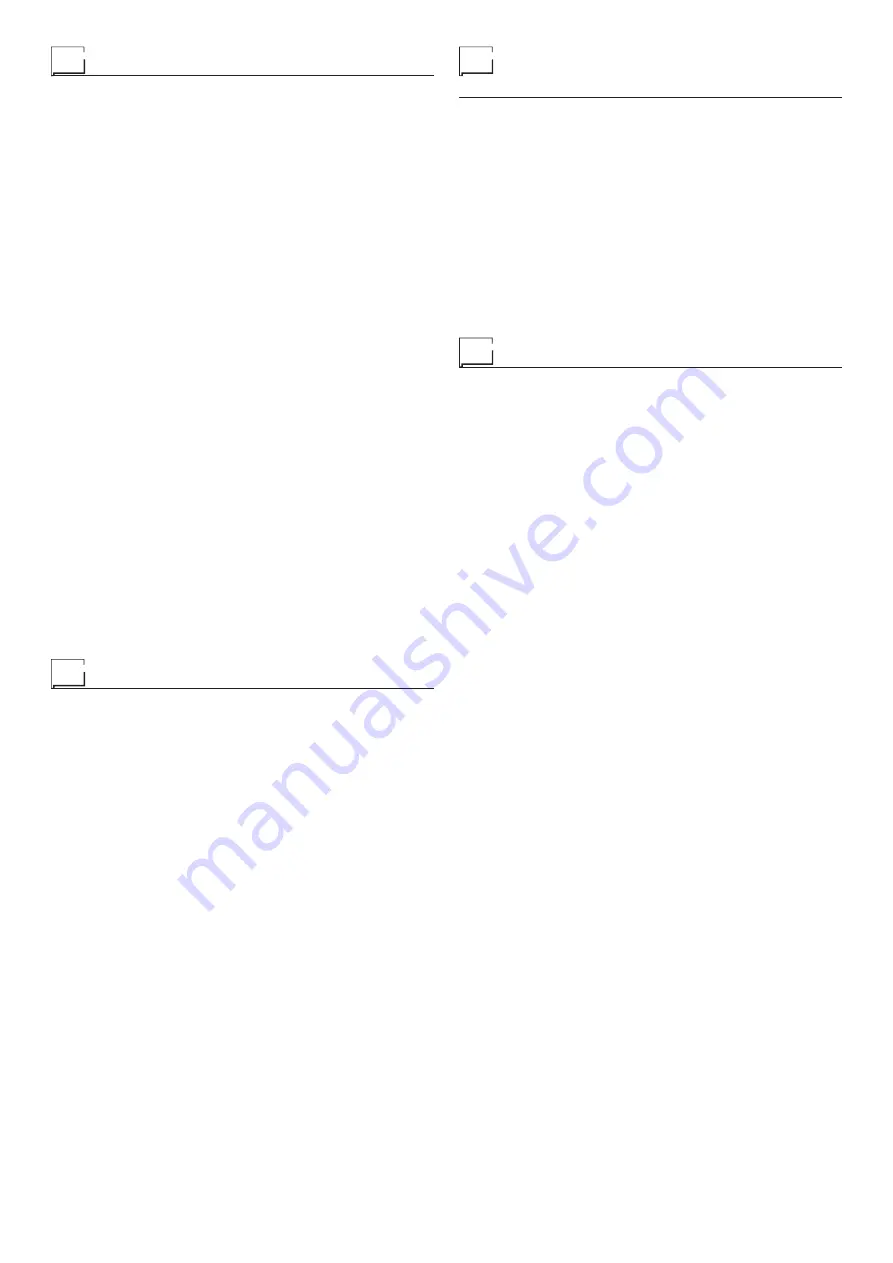
10
Maintenance
ATTENTION: Cut off the power supply to the welding power
source before effecting any internal inspection.
DIX PI GO 2006.M / DIX PI GO 2006.M Puls
IMPORTANT: For fully electronic welding power sources, re-
moving the dust by sucking it into the welding power source by
the fans, is of utmost importance.
In order to achieve correct functioning of the welding power
source, proceed as described:
•
Periodic removal of accumulations of dirt and dust inside the
welding power source using compressed air. Do not point
the jet of air directly at the electrical parts as this could dam-
age them.
•
Periodical inspection for worn cables or loose connections
that could cause overheating.
TORCH
The torch is subjected to high temperatures and is also stressed
by traction and torsion. We recommend not to twist the wire
and not to use the torch to pull the welding power source. As
a result of the above the torch will require frequent mainte-
nance such as:
•
Cleaning welding splashes from the gas diffuser so that the
gas flows freely.
•
Substitution of the contact point when the hole is deformed.
•
Cleaning of the wire guide liner using trichloroethylene or
specific solvents.
•
Check of the insulation and connections of the power cable;
the connections must be in good electrical and mechanical
condition.
SPARE PARTS
Original spares have been specifically designed for our weld-
ing power source. The use of spares that are not original may
cause variations in the performance and reduce the safety lev-
el of the welding power source. We are not liable for damage
due to use of spare parts that are not original.
Optional
AIR AND/OR WATER COOLED UP/DOWN TORCH
This command and works as an alternative:
•
To the ENCODER - SX knob on the welding power source’s
control panel. In “synergic” MIG MAG and “manual” MIG
MAG welding processes, by pressing the two right (+) and
left (-) buttons you can regulate the values for the synergic
welding parameters.
•
To the ENCODER - DX knob on the welding power source’s
control panel. In the JOB welding process, by pressing the
two right (+) and left (-) buttons you can scroll the welding
points set previously.
The pointing out of any difficulties
and their elimination
The supply line is attributed with the cause of the most com-
mon difficulties. In the case of breakdown, proceed as follows:
1) Check the value of the supply voltage.
2) Check that the power cable is perfectly connected to the
plug and the supply switch.
3) Check that the power fuses are not burned out or loose.
4) Check whether the following are defective:
•
The switch that supplies the welding power source
•
The plug socket in the wall
•
The mains switch
NOTE: Given the required technical skills necessary for the
repair of the welding power source, in case of breakdown we
advise you to contact skilled personnel or our technical ser-
vice department.
Replacing the digital interface PCB
Proceed as follows:
•
Unscrew the 4 screws fastening the front rack panel.
•
Remove both the adjustment knobs.
•
Extract wiring connectors from the digital interface PCB.
•
Unscrew the nuts and washers on the support.
•
Remove the digital interface PCB by lifting it out of its sup-
ports.
•
Proceed vice versa to assemble the new digital interface
PCB.
Содержание DIX PI GO 2006.M
Страница 13: ...13 2101AC73...