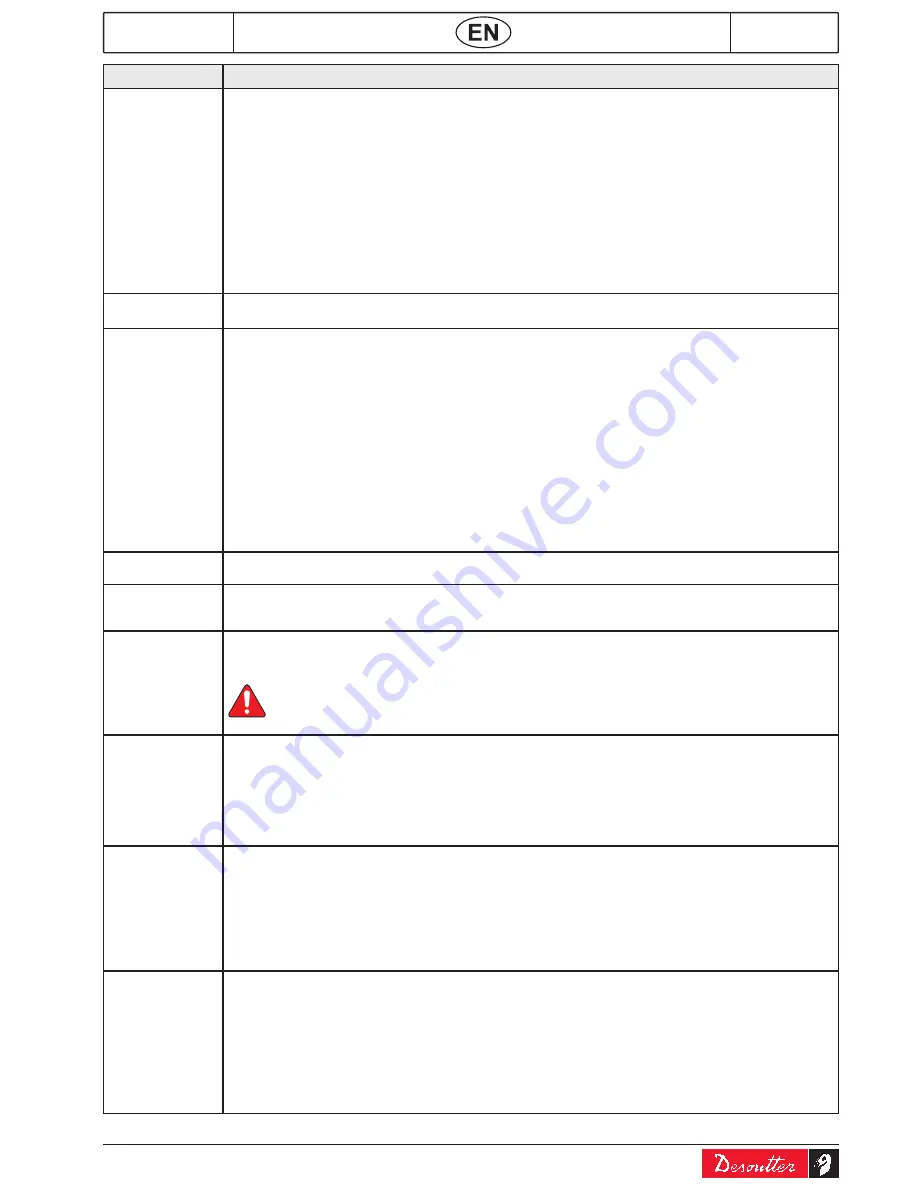
02/2014
65 / 72
6159933910
Issue no: 04
CVIR II
text
Comments
NOt ReADy
List of errors preventing the CVIR II from being ready:
● Over-current: Maximum servo drive current is reached.
● Differential: Earth ground connection opened (the CVIR II does not check earth linkage). This
error is often due to a cable problem.
● Thermal contact: Maximum motor temperature is reached (100°C). This error remains
activated until the motor temperature falls below 80°C.
● SPI link error: The cycle was aborted due to a digital communication problem (SPI) between
the controller and the tool.
● FLEX version error.
● Maximum current (Imax).
● Resolver: Position change or non zero speed detected when the motor start is not activated.
● Temperature: Power components over temperature.
Quickstop 1
● Inform that the input Emergency STOP1 is activated. To run the tool, the controller needs both
Emergency STOP1 & Emergency STOP2 inactive.
svr
The cycle was aborted following a Servo drive error:
● Over-current: The maximum servo drive current is reached.
● Differential: The earth ground connection is opened (the CVIR II does not check earth
linkage). This problem is often due to a cable problem.
● Thermal contact: The maximum motor temperature is reached (100°C). The error is activated
as long as the motor temperature does not fall below 80°C.
● SPI link error: The cycle was aborted due to a communication problem through the digital link
(SPI) between the controller and the tool.
● FLEX version error (FLEX).
● Maximum current (Imax).
● Resolver: Position change or non zero speed detected when the motor start is not activated.
● Temperature: Power components over temperature.
NOTE: All these errors deactivate the READY signal as long as the error exists.
Over current
Maximum servo drive current is reached. In this case, the motor cannot start again.
Overall, it induces a Servo drive error, then a detailed Over-current error.
Differential
Earth tool connection fault (the CVIR II doesn't check earth linkage).
This error is often due to a cable problem. Overall, it induces a Servo drive error, then a detailed
Differential error.
thermal contact
Maximum motor temperature reached (100°C).
The fault is activated as long as the motor temperature doesn't fall below 80°C again. Overall, it
induces a Servo drive error, then a detailed Thermal contact error.
wARNINg: when in MAINteNANCe \ test \ stARt spINDLe mode, this error
does not prevent the motor from working.
general
● Over-current: The maximum servo drive current is reached.
OR
● Differential: The earth ground connection is opened (the CVIR II does not check earth
linkage). This problem is often due to a cable problem.
OR
● Thermal contact: The maximum motor temperature is reached (100°C).
The error is activated as long as the motor temperature does not fall below 80°C.
spI link
The cycle was aborted following a digital (SPI) link fault between the controller and the tool.
This fault removes instantaneously the READY signal of the machine (it is checked every 10ms).
Overall, it induces a Servo drive error, then a detailed SPI error.
● When in the Checking channel menu we get:
- Tool error : Tool link (EEPROM).
- Servo drive error.
● When in START SPINDLE mode the motor is stopped.
● When in TEST and CURRENT CALIBRATION mode: no action.
FLeX version
The FLEX software version is lower than the one necessary for the application version.
This fault can only appear after a software upgrade.
Nevertheless, the delivered software automatically upgrades the FLEX software version.
When this fault occurs:
● It is not possible to start the motor in Normal mode.
● It is possible to start the tool in Test mode.
● It is possible to calibrate the tool manually or automatically.
● It is possible to adjust the resolver offset.
Overall, it induces a Servo drive error, then a detailed FLEX version error.