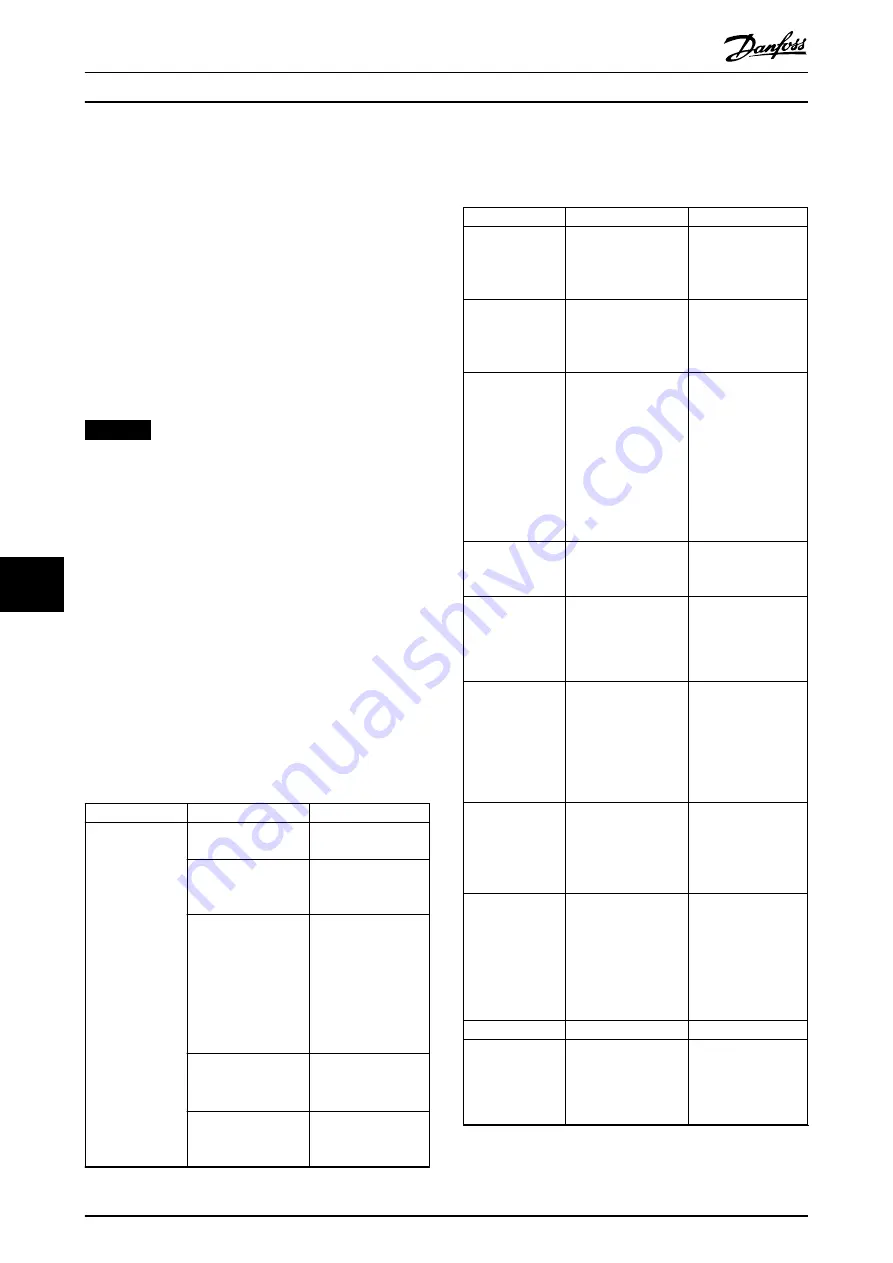
9 Diagnostics
9.1 Faults
If faults occur during servo system operation, check:
•
The LEDs on the servo drive for general problems
relating to communication or device status.
•
The LEDs on the SAB for general problems with
communication, auxiliary supply, or STO voltage.
The error codes can be read using the ISD Toolbox
software, the LCP, or the PLC. The LCP only shows faults
relating to the device it is connected to.
NOTICE
If the fault cannot be eliminated by 1 of the measures
listed in
or
, notify Danfoss Service.
Have the following information available to enable Danfoss
to provide help quickly and effectively:
•
Type number
•
Error code
•
Firmware version
•
System set-up (for example, number of servo
drives and lines).
9.2 Servo Drive
9.2.1 Troubleshooting
First use
to check the possible causes of the fault
and possible solutions. The error codes are listed in
.
Fault
Possible cause
Possible solution
LCP display dark
or has no
function.
Missing input power.
Check the input
power source.
Missing or open fuses
or circuit breaker
tripped.
Check the fuses and
circuit breaker.
No power to the LCP.
•
Check the LCP
cable for proper
connection or
damage.
•
Replace any faulty
LCP or connection
cables.
Incorrect contrast
setting.
Press [Status] +
[
▲
]/[
▼
] to adjust the
contrast.
Display is defective.
Replace the faulty
LCP or connection
cable.
Fault
Possible cause
Possible solution
Servo drive
overheats (high
surface
temperature).
Excessive load.
Check the torques.
Servo drive not
running.
No drive communi-
cation or drive in
error mode.
Check the fieldbus
connection and the
status LEDs on the
servo drive.
Servo drive does
not run or only
starts up slowly or
with difficulty.
•
Bearing wear.
•
Incorrect
parameter
settings.
•
Incorrect control
loop parameters.
•
Incorrect torque
settings.
•
Check the
bearings and
shaft.
•
Check the
parameter
settings.
Drive hums and
draws high
current.
Drive defective.
Contact Danfoss.
Drive stops
suddenly and
does not restart.
•
No drive
communication.
•
Servo drive in
error mode.
Check the fieldbus
connection and the
status LEDs on the
servo drive.
Wrong motor
rotation direction.
Parameter error.
•
Check the
parameter
settings.
•
Change the
rotation direction
if appropriate.
Drive runs
normally, but
does not generate
the expected
torque.
•
Drive defective.
•
Parameter error.
•
Check the
parameter
settings.
•
Contact Danfoss.
Drive screaming.
•
Incorrect
calibration.
•
Faulty current
measurement.
•
Incorrect control
loop parameters.
•
Check the
parameter
settings.
•
Contact Danfoss.
Uneven running.
Defective bearing.
Check the shaft.
Vibration.
•
Defective bearing.
•
Incorrect control
loop parameters.
•
Check the shaft.
•
Check the
parameter
settings.
Diagnostics
VLT
®
Integrated Servo Drive ISD
®
510 System
74
Danfoss A/S © 12/2015 All rights reserved.
MG75K102
9
9
Содержание VLT Integrated Servo Drive ISD 510 System
Страница 2: ......
Страница 101: ...Index Operating Instructions MG75K102 Danfoss A S 12 2015 All rights reserved 99...