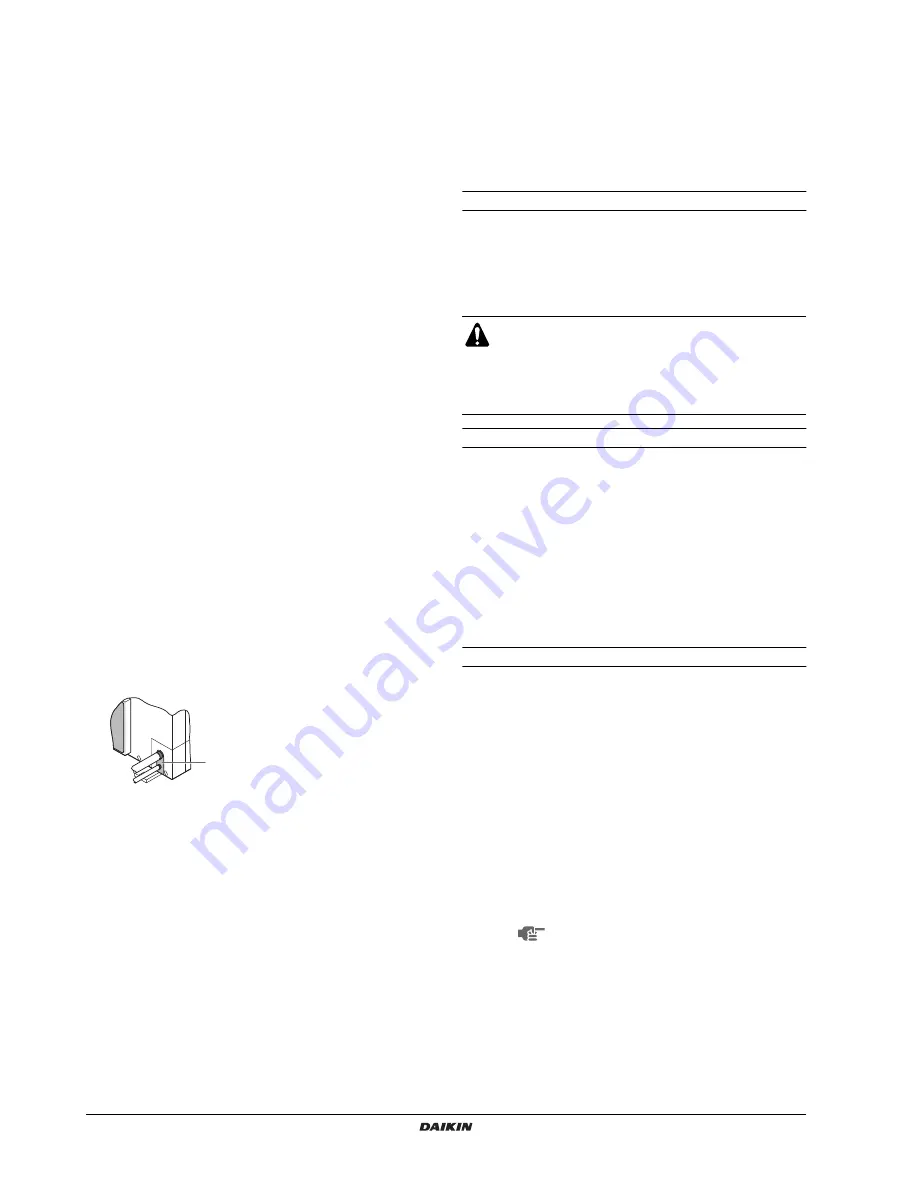
Installation manual
9
ERSQ+ERRQ011~Y1
Outdoor unit for air to water heat pump
4PW49635-1A
7.
P
IPING
CONNECTION
WORK
7.1.
Refrigerant piping
■
Field pipes can be installed in four directions.
Figure - Field pipes in four directions
(See figure 5)
When connecting the piping in the lateral direction (on the rear),
remove the piping cover (rear) in reference to
figure 7
.
■
To install the connecting pipe to the unit in a downward direction,
make a knockout hole by penetrating the center area around the
knockout hole using a Ø6 mm drill.
(See figure 5)
.
■
Cutting out the two slits makes it possible to install as shown in
figure 5
.
(Use a metal saw to cut out the slits.)
■
After knocking out the knock-out, it is recommended to apply
repair paint to the edge and the surrounding end surfaces to
prevent rusting.
7.2.
Preventing foreign objects from entering
Plug the pipe through-holes with putty or insulating material (field
supply) to stop up all gaps, as shown in the figure.
Insects or small animals entering the outdoor unit may cause a short
circuit in the electrical box.
7.3.
Leak test and vacuum drying
When all piping work is complete and the outdoor unit is connected to
the indoor unit, it is necessary to (a) check for any leakages in the
refrigerant piping and (b) to perform vacuum drying to remove all
moisture in the refrigerant piping.
If there is a possibility of moisture being present in the refrigerant
piping (for example, rainwater may have entered the piping), first
carry out the vacuum drying procedure below until all moisture has
been removed.
General guidelines
■
All piping inside the unit has been factory tested for leaks.
■
Use a 2-stage vacuum pump with a non-return valve which can
evacuate to a gauge pressure of –100.7 kPa (5 Torr absolute,
–755 mm Hg).
■
Connect the vacuum pump to both the service port of the gas
stop valve and the liquid stop valve to increase efficiency.
Setup
(See figure 6)
Leak test
The leak test must satisfy specification EN 378-2.
1
Vacuum leak test
1.1 Evacuate the system from the liquid and gas piping to
–100.7 kPa (5 Torr).
1.2 Once reached, turn off the vacuum pump and check that
the pressure does not rise for at least 1 minute.
1.3 Should the pressure rise, the system may either contain
moisture (see vacuum drying below) or have leaks.
2
Pressure leak test
2.1 Break the vacuum by pressurizing with nitrogen gas to a
minimum gauge pressure of 0.2 MPa (2 bar).
Never set the gauge pressure higher than the maximum
operation pressure of the unit, i.e. 4.0 MPa (40 bar).
2.2 Test for leaks by applying a bubble test solution to all piping
connections.
2.3 Discharge all nitrogen gas.
1
Drill
2
Center area around knockout hole
3
Knockout hole
4
Slit
5
Connecting pipe liquid (field supply)
6
Bottom frame
7
Front plate
8
Pipe outlet plate
9
Screw front plate
10
Pipe outlet plate screw
A
Forward
B
Backward
C
Sideways
D
Downward
1
Piping cover (rear)
1
Putty or insulating material (field
supply)
1
■
Do not purge the air with refrigerants. Use a vacuum
pump to evacuate the installation. No additional
refrigerant is provided for air purging.
■
Make sure that the gas stop valve and liquid stop
valve are firmly closed before performing the leak test
or vacuum drying.
1
Pressure reducing valve
2
Nitrogen
3
Siphon system
4
Vacuum pomp
5
Valve A
6
Gas line stop valve
7
Liquid line stop valve
8
Stop valve service port
9
Charge hose
Make sure to use a recommended bubble test
solution from your wholesaler.
Do not use soap water, which may cause
cracking of flare nuts (soap water may contain
salt, which absorbs moisture that will freeze
when the piping gets cold), and/or lead to
corrosion of flared joints (soap water may contain
ammonia which causes a corrosive effect
between the brass flare nut and the copper flare).
Содержание ERSQ011AAV1
Страница 22: ...4PW49635 1A Copyright Daikin...