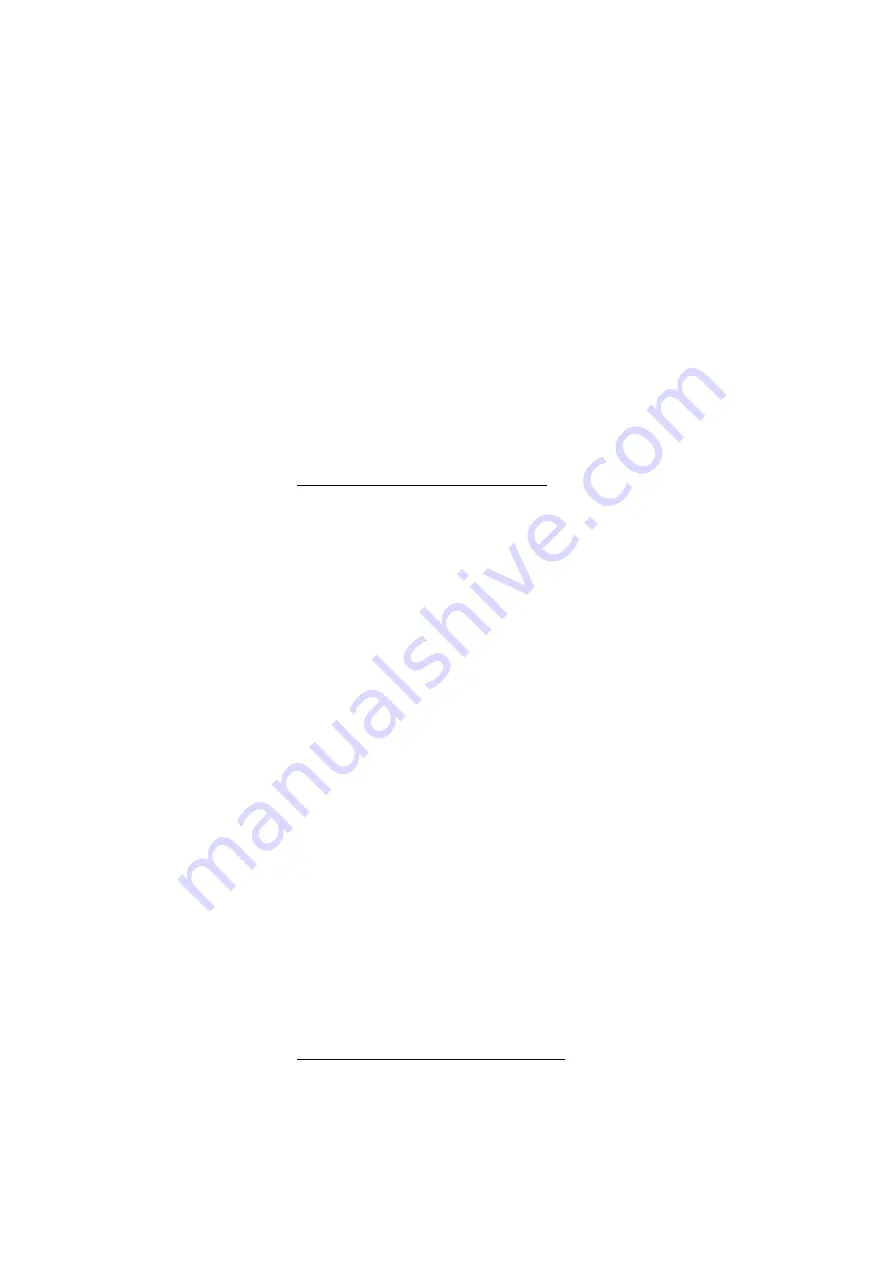
9711IMA-70
Maintenance
15-9
5.
Enter “h0800”, and verify the feed moves toward the RHCP marker. Entering it again should
result in the feed moving closer to the marker.
6.
Manually depress the RHCP limit switch, and enter the same command again. The motor should
not move.
7.
Continue to depress the RHCP limit switch, and enter “h0350”, and verify the feed moves
toward the LHCP marker. (If it does not drive, test the diode on the Motor Termination PCB to
ascertain if it has failed or is installed backwards).
8.
Connect the “Rotary Joint” coax (SMA) to the PCU (so that auto-pol can target polarization).
If the motor does not drive, assure that the feed is not at the LHCP or RHCP limit (limit switch engaged).
Remove the motor from the circular section by removing the mounting plate screws and disengage the
drive sprocket. Listen to the motor and observe the drive sprocket. If the motor is driving (internally) but
the drive sprocket is not turning or the motor is not driving, the motor may be failed.
Refer to drawing 134868 page 2 wiring diagram to check continuity of wiring connections from the
Circular Section Motor Termination PCB through the limit switch(es) to the motor and pot.
Isolate & replace the faulty component.
Reinstall the motor and engage the drive sprocket.
Retest steps 1-6 above to verify that drive capability is restored. The feed assembly does not need to be
re-calibrated as long as the potentiometer has not been replaced, disengaged or removed from its
mounting location.
15.4.5.
Linear Feed Drive Test Procedure:
Use ProgTerm to enter the commands below.
1.
Disconnect the “Rotary Joint” coax (SMA) from the PCU (this prevents auto-pol from overriding
your drive commands).
2.
Enter “g0030”, and verify the feed moves toward the CCW marker. Entering it again should
result in the feed moving closer to the marker.
3.
Manually depress the CCW limit switch, and enter the same command again. The motor should
not move.
4.
Continue to depress the CCW limit switch, and enter “g0210”, and verify the feed moves toward
the CW marker. (If it does not drive, test the diode on the Motor Termination PCB to ascertain
if it has failed or is installed backwards).
5.
Enter “g0210”, and verify the feed moves toward the CW marker. Entering it again should result
in the feed moving closer to the marker.
6.
Manually depress the CW limit switch, and enter the same command again. The motor should
not move.
7.
Continue to depress the CW limit switch, and enter “g0030”, and verify the feed moves toward
the CCW marker. (If it does not drive, test the diode on the Motor Termination PCB to ascertain
if it has failed or is installed backwards).
8.
Connect the “Rotary Joint” coax (SMA) to the PCU (so that auto-pol can target polarization).
If the motor does not drive, assure that the feed is not at the CW or CCW limit (limit switch engaged).
Remove the motor from the linear section by removing the mounting plate screws and disengage the
drive sprocket. Listen to the motor and observe the drive sprocket. If the motor is driving (internally) but
the drive sprocket is not turning or the motor is not driving, the motor may be failed.
Refer to drawing 134868 page 2 wiring diagram to check continuity of wiring connections from the
Circular Section Motor Termination PCB through the limit switch(es) to the motor and pot.
Isolate & replace the faulty component.
Reinstall the motor and engage the drive sprocket.
Retest steps 1-6 above to verify that drive capability is restored. The feed assembly does not need to be
re-calibrated as long as the potentiometer has not been replaced, disengaged or removed from its
mounting location.
15.4.6.
Circular Feed Calibration Procedure:
This section of the feed drives the polarizer to the LHCP, Linear or RHCP position to select the correct TX
polarization MODE. When Linear mode is selected the bottom (linear) section will actively be driven to
the correct linear position for the satellite you have targeted.
The feed assembly does
NOT
need to be re-calibrated as long as the potentiometer has not been
replaced, disengaged or removed from its mounting location.
For connection setup & operation of ProgTerm refer to PC Computer Setup (ProgTerm) paragraph above.
EAR Controlled - ECCN EAR99
Содержание SEA TEL 9711IMA-70
Страница 6: ...9711IMA 70 vi This Page Intentionally Left Blank EAR Controlled ECCN EAR99...
Страница 10: ...9711IMA 70 Table of Contents x This Page Intentionally Left Blank EAR Controlled ECCN EAR99...
Страница 14: ...Introduction 9711IMA 70 1 4 This Page Intentionally Left Blank EAR Controlled ECCN EAR99...
Страница 54: ...Configuring a Computer for the MXP 9711IMA 70 4 6 This Page Intentionally Left Blank EAR Controlled ECCN EAR99...
Страница 58: ...Setup Tracking Receiver VSAT 9711IMA 70 6 2 This Page Intentionally Left Blank EAR Controlled ECCN EAR99...
Страница 60: ...Setup Azimuth Trim 9711IMA 70 7 2 This Page Intentionally Left Blank EAR Controlled ECCN EAR99...
Страница 74: ...Setup Targeting 9711IMA 70 10 4 This Page Intentionally Left Blank EAR Controlled ECCN EAR99...
Страница 78: ...Setup Satellite Configuration 9711IMA 70 11 4 This Page Intentionally Left Blank EAR Controlled ECCN EAR99...
Страница 84: ...Quick Start Operation 9711IMA 70 12 6 This Page Intentionally Left Blank EAR Controlled ECCN EAR99...
Страница 122: ...9711IMA 70 Technical Specifications 9711IMA 70 17 10 This Page Intentionally Left Blank EAR Controlled ECCN EAR99...
Страница 124: ...Drawings 9711IMA 70 18 2 This Page Intentionally Left Blank EAR Controlled ECCN EAR99...
Страница 132: ...EAR Controlled ECCN EAR99...
Страница 133: ...EAR Controlled ECCN EAR99...
Страница 134: ...EAR Controlled ECCN EAR99...
Страница 159: ...EAR Controlled ECCN EAR99...
Страница 160: ...EAR Controlled ECCN EAR99...
Страница 165: ...EAR Controlled ECCN EAR99...
Страница 177: ...EAR Controlled ECCN EAR99...
Страница 178: ...EAR Controlled ECCN EAR99...