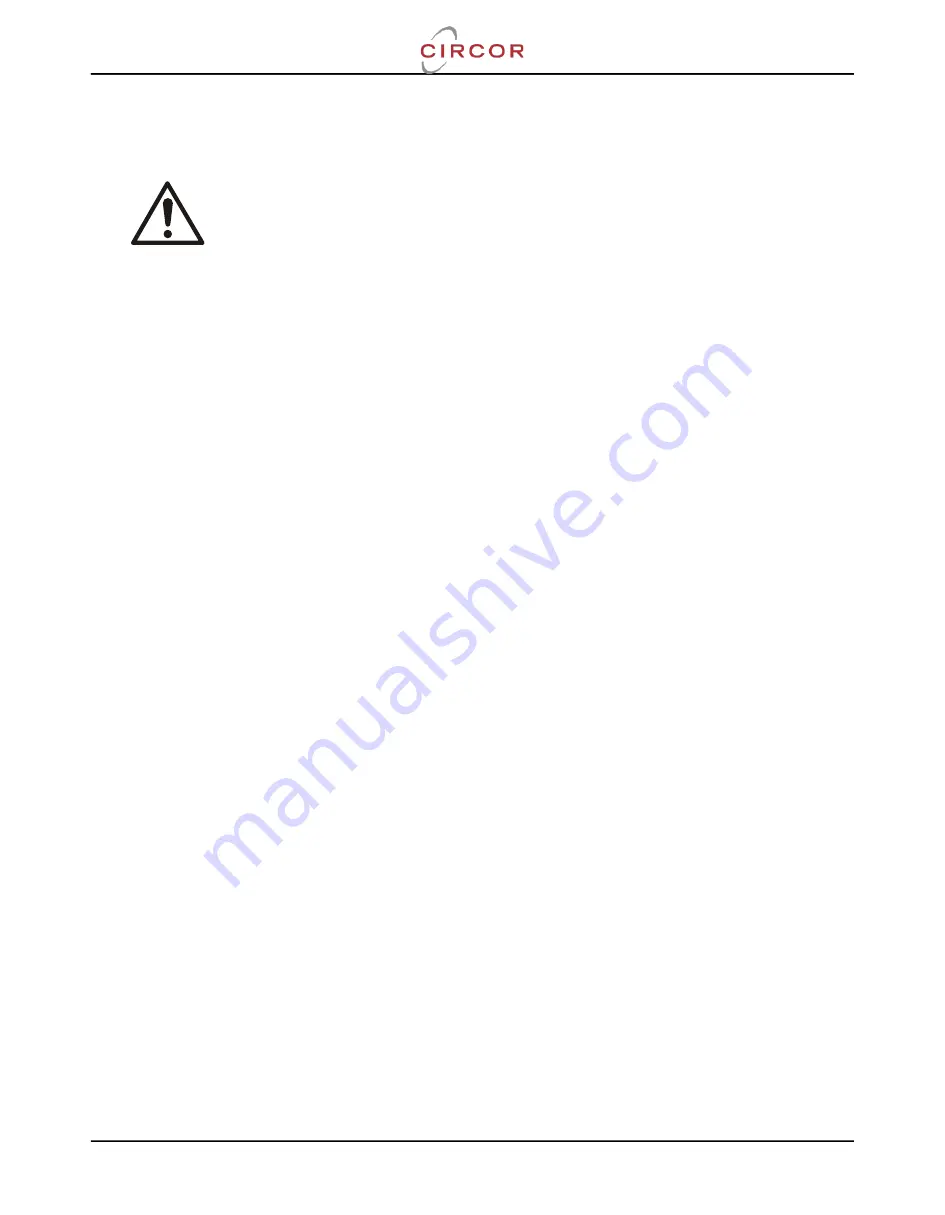
Product Description
54
TT Twin-Screw Pump -
Installation, Operation & Maintenance Manual
Make the final alignment of the pump and driver
WARNING:
•
Failure to disconnect and lock out driver power may result in serious physical injury or
death. Always disconnect and lock out power to the driver before performing any
installation or maintenance tasks.
•
Electrical connections must be made by certified electricians in compliance with all
international, national, state, and local rules.
•
Refer to driver/coupling/gear manufacturer's installation and operation manuals (IOM) for
specific instructions and recommendations.
•
Misalignment can cause decreased performance, equipment damage, and even
catastrophic failure leading to serious injury. Proper alignment is the responsibility of the
installer and the user of the unit. Check the alignment of all drive components prior to
operating the unit.
•
Follow the coupling installation and operation procedures from the coupling manufacturer
You must check the final alignment after the pump and driver are at operating temperature.
For initial alignment instructions, see the Installation chapter.
1. Run the unit under actual operating conditions for enough time to bring the pump,
driver, and associated system to operating temperature.
2. Shut down the pump and the driver.
3. Remove the coupling guard.
4. Check the alignment while the unit is still hot. See Pump-to-driver alignment in the
Installation chapter.
5. Reinstall the coupling guard.
6. Restart the pump and driver.