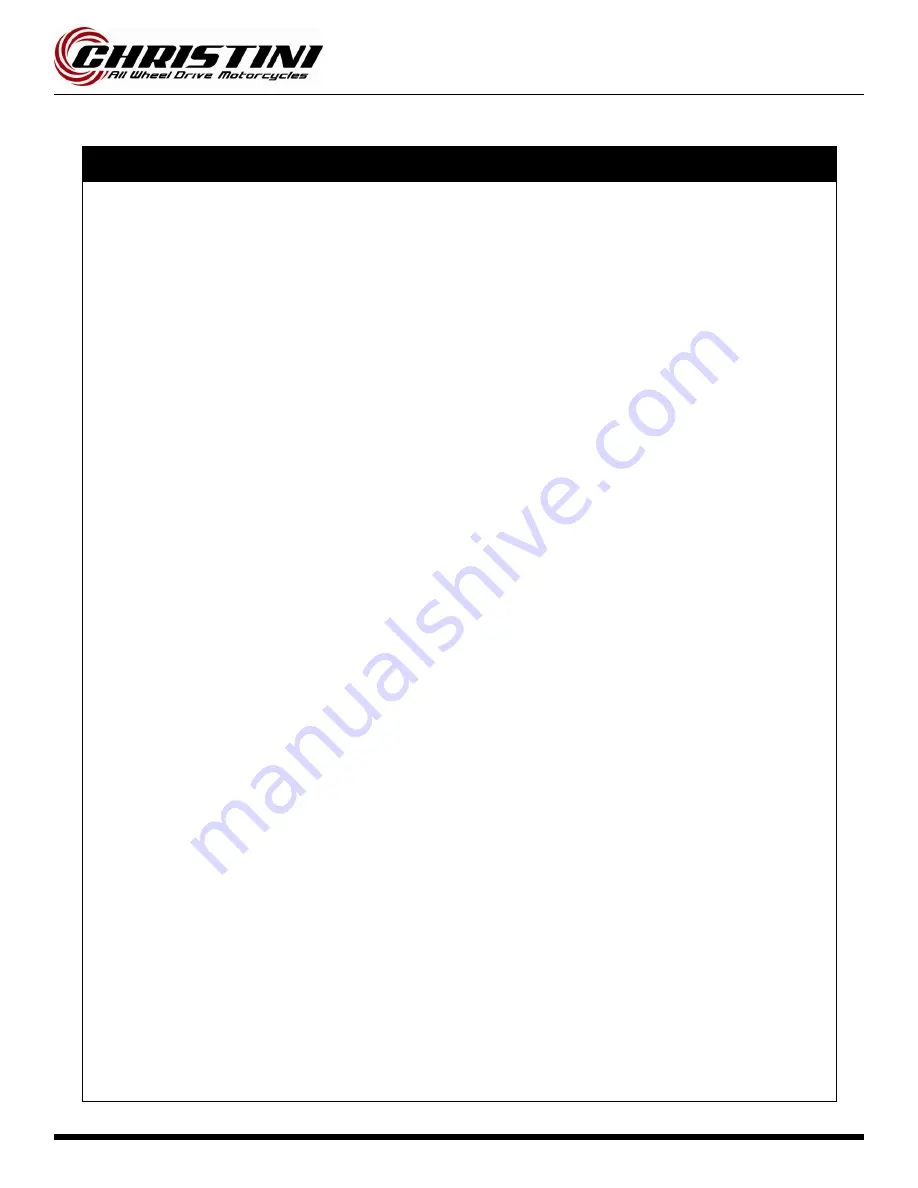
Page 4
AWD Service
Required tools
41
AWD detailed illustration
42
Routine maintenance schedule
44
AWD clutch test
45
AWD sprag test
46
AWD chain removal
47
AWD engagement switch
51
Front wheel removal
56
Front wheel service
58
Fork removal and installation
65
Dropout service
67
Fork spline bearing service
76
Boot Replacement
81
Triple clamp removal
83
Triple clamp service
85
Main drive shaft removal
100
Head tube bearing service
101
Triple Clamp Installation
104
Gearbox removal
108
Gearbox service
109
AWD clutch removal
114
AWD clutch Service
115
Troubleshooting
119
Warranty
120
Main drive shaft installation
103
Table of Contents
Содержание AWD 250
Страница 2: ......
Страница 6: ...Page 5 Specifications ...
Страница 38: ...Page 37 Troubleshooting ...
Страница 39: ...Page 38 Troubleshooting ...
Страница 40: ...Page 39 Wiring Diagram ...
Страница 41: ...Page 40 AWD Service AWD Service Section AWD Service Section AWD Service Section AWD Service Section ...
Страница 43: ...Page 42 AWD Detail Illustration ...
Страница 48: ...Page 47 Cover and Chain Removal ...
Страница 49: ...Page 48 Cover and Chain Removal ...
Страница 52: ...Page 51 AWD Engagement ...
Страница 59: ...Page 58 Front Wheel Service ...
Страница 68: ...Page 67 Dropout Service ...
Страница 77: ...Page 76 Fork Spline Bearing Service ...
Страница 86: ...Page 85 Triple Clamp Service ...
Страница 87: ...Page 86 Triple Clamp Service ...
Страница 102: ...Page 101 Head Tube Bearing Service Picture above shows a head tube not welded to the frame for reference ...
Страница 110: ...Page 109 Gear Box Service ...
Страница 111: ...Page 110 Slide clutch basket off output gear Remove output seals from gear box Remove output snap ring Gear Box Service ...
Страница 116: ...Page 115 Clutch Service ...
Страница 124: ......