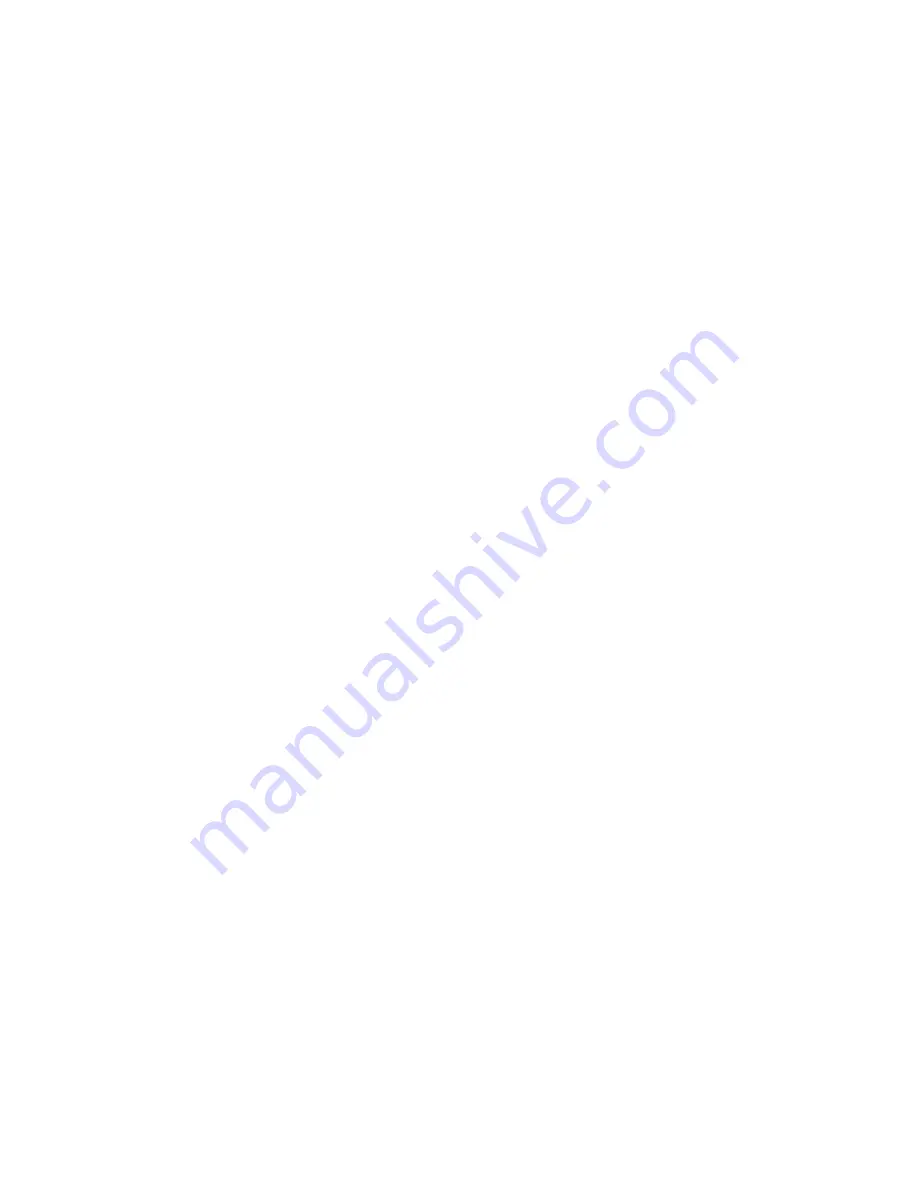
34
•
Service Test
COOL
RHV
(Humidi-MiZer 3-Way
Valve). On Humidi-MiZer equipped units, this item allows
the user to switch the reheat valve from ON to OFF and
vice versa. When
RHV
is switched to the ON position, a 3-
way valve will be energized, allowing refrigerant flow to
enter the reheat coil as if in a dehumidification mode or re
-
heat mode. When
RHV
is switched to the OFF position,
the 3-way valve will be deenergized and the unit will re
-
vert back to normal cooling. Note that this function only
allows manipulation of
RHV
if a compressor on Circuit B
has already been turned ON. To manually exercise this
valve without an active Circuit B compressor, see the sec
-
tion titled
Service Test
HMZR
RHV
. To view the actu
-
al valve position at any time, the user can use the Outputs
menu (
Outputs
COOL
RHV)
.
•
Service Test
COOL
C.EXV
(HMV-1: Condenser EXV
Position). On Humidi-MiZer
®
equipped units, this item al
-
lows the user to exercise the valve that controls refrigerant
flow to the Circuit B condenser. To exercise the valve,
RHV
must first be switched to ON
(Service
Test
COOL
RHV)
and a Circuit B compressor must be
commanded ON. The valve default position is 100% (com
-
pletely open). The user will be able to adjust the valve
from 0 to 100% through this function. The only constraint
on the valve position is that the percentage sum of the by
-
pass valve
(Service Test
COOL
B.EXV)
and condens
-
er valve must equal 100%. For example, if the condenser
modulating valve is only 80% open, then the gas bypass
modulating valve must remain at least 20% open. The ef
-
fect of closing the condenser valve will be to increase the
supply-air temperature (additional reheat capacity). To
view the actual valve position at any time, the user can use
the Outputs menu (
Outputs
COOL
C.EXV).
•
Service Test
COOL
B.EXV
(HMV-2: Bypass EXV Po
-
sition). On Humidi-MiZer equipped units, this item allows
the user to exercise the valve that controls discharge gas
bypass around the Circuit B condenser. To exercise the
valve,
RHV
must first be switched to ON
(Service
Test
COOL
RHV)
and a Circuit B compressor must be
commanded ON. The valve default position is 0% (com
-
pletely closed). The user will be able to adjust the valve
from 0 to 100% through this function. The only constraint
on the valve position is that the percentage sum of the by
-
pass
valve
and
condenser
valve
(
Service
Test
COOL
C.EXV)
must equal 100%. For example, if
the condenser modulating valve is only 80% open, then the
gas bypass modulating valve must remain at 20% open.
The effect of opening the bypass valve will be to increase
the supply air temperature (additional reheat capacity).
To
view the actual valve position at any time, the user can use
the Outputs menu (
Outputs
COOL
B.EXV).
Heating
The Heat Test Mode submenu will offer automatic fan start-up
if not a gas-fired heat unit. On gas heat units, the IGC (integrat
-
ed gas controller) feedback from the gas control units will
bring the fan on as required.
Within this submenu, control of the following is possible:
•
Service Test
HEAT
HT.ST
(Requested Heat Stage).
When this item is non-zero, the currently configured heat
type will energize the corresponding heat relay pattern that
reflects the requested stage. In addition, the upper limit
will be clamped to reflect the maximum configured num
-
ber of stages. When non-zero, the heat relays will be
“read-only” and reflect the currently selected pattern.
•
Service
Test
HEAT
HT.1-10
,
Service
Test
HEAT
HIR
(Manual Heat Relay Control). If the “Heat
Stage Request” item is set to zero, it will be possible to
individually control the heat relays, including the heat in
-
terlock relay.
•
Service Test
HEAT
H1.CP
(Modulating Heat Capaci
-
ty). If configured for modulating gas or SCR electric heat,
the user will be able to manually control the capacity of the
modulating heat section (0 to 100%). The requested heat
stage must be greater than or equal to 1 or heat relay 1
must be on before the control will accept a modulating
heat capacity request. If neither case is true, the control
will overwrite the modulating heat request back to 0%.
•
Service Test
HEAT
HTC.C
(
Ht Coil Command Posi
-
tion). If configured for hydronic heat type, the user will be
able to manually control the positioning of the actuator,
which controls hot water (0 to 100%).
SERVICE COMPONENT TESTS
Auto-component testing is the automated testing procedure of
a component or a group of components. Auto-component test
-
ing can be used during commissioning of a unit to verify that
components are functioning properly. It can also be used as a
diagnostics routine for troubleshooting.
Control Description (Overview)
The 40/50N Series large rooftop unit is capable of performing
auto-component tests. The auto-component tests appear in Navi
-
gator under the Service Test menu (
Service Test
AC.DT
):
The unit must be in Service Test mode to perform the auto-
component tests (
Service Test
TEST
ON
).
Starting another test before a currently running test has com
-
pleted will cancel the running test and reset all outputs before
starting the newly requested test.
Setting Service Test mode to “OFF” while running an auto-com
-
ponent test will cancel the running test and reset all outputs.
For a complete description of notices, alerts, and alarms refer
-
enced, see the Alarms and Alerts section.
Auto-component tests will have a status indicated by:
1. Not Run
2. Running
3. Pass
4. Fail
The results of all auto-component tests will default to “NOT
RUN.”
After power cycling the MBB, the results of all auto-compo
-
nent tests will default to “NOT RUN.”
If the required conditions for the test are not met, the test will
not be allowed to run. Note that there may be no indication for
the possible reasons why a test might not run.
For each auto-component test, if the verification criteria is met,
test status will display “PASS” and if the verification criteria is
not met, test status will display “FAIL.”
For each auto-component test, the following information is
grouped in one screen: test status, component status, and val
-
ues of response parameters.
Auto-Component Test Control Descriptions
The compressor auto-component test requires the following
conditions:
1. Unit is not shut down due to failure (A152).
CP.TS
Compressor Auto-Test
DS.TS
Dig Scroll Auto-Test
EX.TS
EXVS Auto-Component Test
CD.TS
Charge Tst without Lqd Sens.
ML.TS
MLV/HGBP Auto-Test
SF.TS
Supply Fan Auto-Test
RSLT
Comps Auto-Test Results
Содержание WeatherExpert 48N2
Страница 135: ...135 Fig 18 48 50N Typical Power Schematic Nominal 075 Ton Unit Shown ...
Страница 136: ...136 Fig 19 48 50N Typical Power Schematic Nominal Ton 90 150 Units Shown ...
Страница 137: ...137 Fig 20 48 50N Main Base Board Input Output Connections ...
Страница 138: ...138 Fig 21 48 50N RXB EXB CEM Input Output Connections a48 9307 ...
Страница 139: ...139 Fig 22 48 50N EXV SCB Input Output Connections a48 9308 ...
Страница 140: ...140 Fig 23 48N Typical Modulating Gas Heat Unit Control Wiring ...
Страница 141: ...141 Fig 24 50N Typical Electric Heat Unit Control Wiring ...
Страница 144: ...144 Fig 27 48N Typical Gas Heat Section Wiring Nominal Ton 120 to 150 Units ...
Страница 145: ...145 Fig 28 48 50N Typical Power Component Control Wiring 460 v ...
Страница 146: ...146 Fig 29 48 50N Component Control Wiring 575 v Nominal Ton 075 to 150 Units ...
Страница 147: ...147 Fig 30 48 50N Component Arrangement Power Box ...
Страница 148: ...148 Fig 31 48 50N Component Arrangement Control Box ...
Страница 168: ...168 Fig 47 Sensor and Ignition Position Fig 48 Combustion Blower Details SENSOR DETAILS IGNITION DETAILS ...
Страница 240: ...240 APPENDIX D VFD INFORMATION CONT Fig G VFD Bypass Wiring Diagram WHEN USED ...