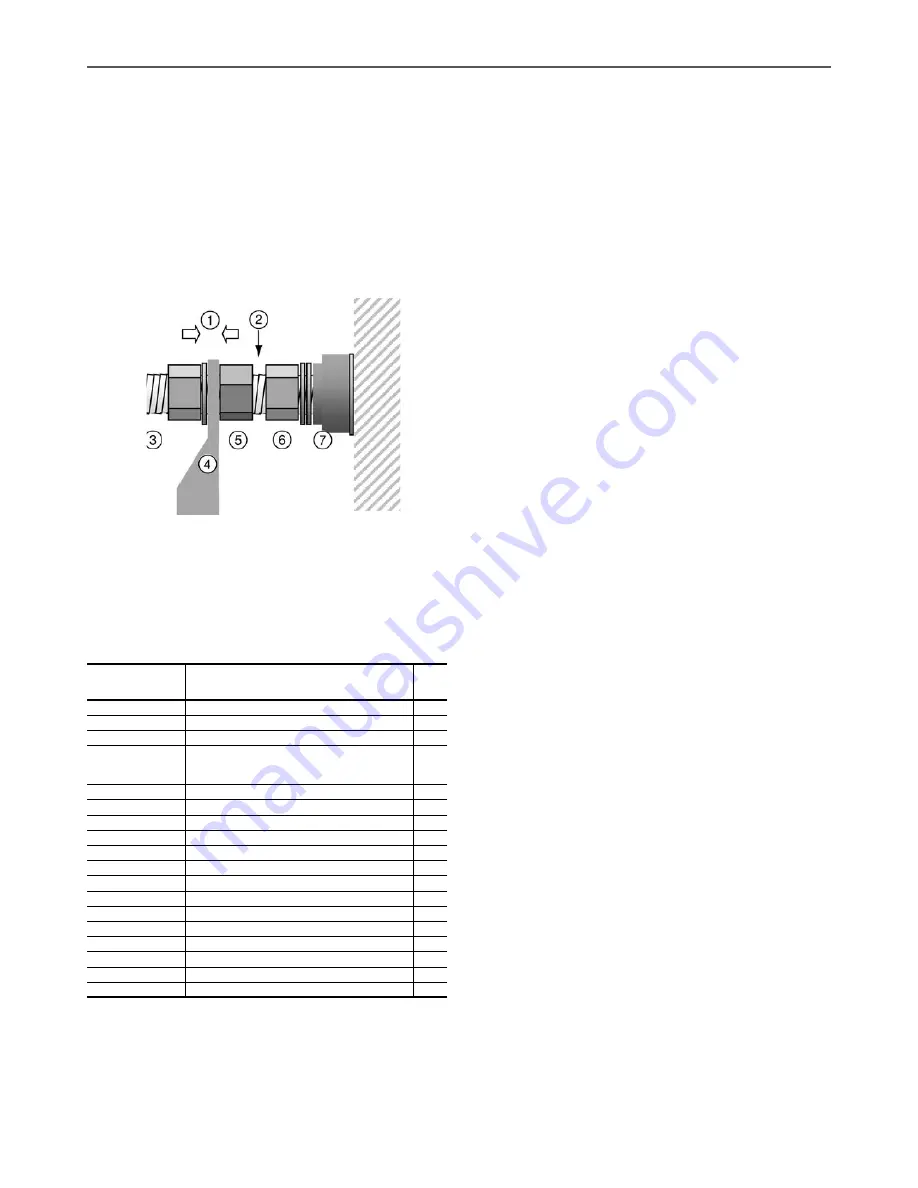
64
13.4.2 - Connection precautions for the compressor power
terminals
These precautions must be applied during an intervention that
requires the removal of the power conductors connected to the
compressor supply terminals.
The tightening nut of terminal (6) supporting the isolator (7) must
never be loosened, as ist ensures terminal tightness and
compressor leak tightness.
The tightening of phase lug (4) must apply the torque between counter
nut (5) and tightening nut (3): During this operation a counter-torque
must be applied at counter nut (5). Counter-nut (5) must not be in
contact with the tightening nut of terminal (6).
1. Torque application to tighten the lug
2. Avoid contact between the two nuts
3. Lug tightening nut
4. Flat lug
5. Counter-nut
6. Terminal tightening nut
7. Isolator
13.5 - Tightening torques for the main bolts and screws
Screw type
Use
Value
(N.m)
(N·m)
Metal screw D = 4.8
Condensing module, housing supports
4,2
Screw H M8
Condensing module, compressor fixing
18
Taptite screw M10
Condensing module, chassis - structure fixing,
control box fixings, compressor fixings, oil
separator fixing
30
Taptite screw M6
Piping support, cowling
7
Screw H M8
Piping clip
12
Screw H M6
Piping clip
10
Nut H M10
Compressor chassis
30
Nut H M10
Hydraulic pump chassis
30
Screw H M8
Filter drier cover
35
Screw H M12
Economiser port flange
40
Screw H M16
Oil separator flanges, suction flanges
110
Screw H M16
Heat exchanger water boxes
190
Screw H M20
Suction flanges
190
Nut 5/8 ORFS
Oil line
65
Nut 3/8 ORFS
Oil line
26
Nut H M12/M16
Victaulic collars on suction piping
60/130
Self-locking Nut M16
Compressor fixing
30
ATTENTION: The tightening of the connections at the
compressor terminals requires special precautions. Please
refer to the chapter below.
13.6 - Condenser coil
We recommend, that coils are inspected regularly to check the
degree of fouling. This depends on the environment where the
unit is installed, and will be worse in urban and industrial
installations and near trees that shed their leaves.
For coil cleaning, two maintenance levels are used, based on the
AFNOR X60-010 standard:
13.6.1 - Level 1
13.6.1.1 - Recommendations for maintenance and cleaning
of round tube plate fin (RTPF) condenser coils
-
Regular cleaning of the coil surface is essential for correct
unit operation. Eliminating contamination and removal of
harmful residue will increase the operating life of the coils
and the unit.
-
The maintenance and cleaning procedures below are
part of the regular maintenance and will prolong the life
of the coils.
Removal of fibres that obstruct the surfaces
Fibres and dirt collected on the coil surface must be removed with a
vacuum cleaner. If you do not have a vacuum cleaner, a soft brush
with non-metallic bristles can be used instead. In all cases cleaning
must be done in the direction of the fins, as the coil surface is easily
damaged. The fins bend easily and damage the protective coating
of the coil, if cleaning is done at right angles to the fins. Clean
against the air flow direction.
NOTE: Using a water jet from a spray hose on a polluted surface
will result in fibres and dirt becoming trapped in the coil, making
cleaning more difficult. All fibres and dirt must be removed from
the surface, before using a low-speed rinsing jet.
Periodical cleaning with clean water:
For coils installed in a coastal or industrial environment
periodical cleaning by rinsing with water is beneficial. It is
however essential that rinsing is done with a low-speed water
jet to avoid damaging the fins. Monthly cleaning as described
below is recommended.
ATTENTION
-
Chemical cleaning agents, water containing bleach,
acidic or basic cleaning agents must never be used
to clean the coil exterior or interior. These cleaning
agents may be difficult to rinse off and can accelerate
corrosion at the joint between tube and fins, where
two different materials come into contact.
-
High-speed water from a high-pressure cleaner, spray
hose or compressed air cleaner must never be used
for coil cleaning. The force of the water or air jet will
bend the fins and increase the air-side pressure drop.
This can result in reduced performance or nuisance
shutdowns of the unit.
13.6.1.2 - Recommendations for maintenance and cleaning
of MCHE (microchannel) condenser coils
-
Regular cleaning of the coil surface is essential for correct
unit operation. Eliminating contamination and removal of
harmful residue will increase the operating life of the coils
and the unit.
-
The maintenance and cleaning procedures below are
part of the regular maintenance and will prolong the life
of the coils.
ATTENTION: Do not use chemical cleaners on MCHE
condenser coils. These cleaning agents can accelerate
corrosion and damage the coils.
-
Remove foreign objects and debris attached to the coil
surface or wedged between the chassis and the supports.
13 - STANDARD MAINTENANCE
Содержание AquaForce 30XB series
Страница 69: ......