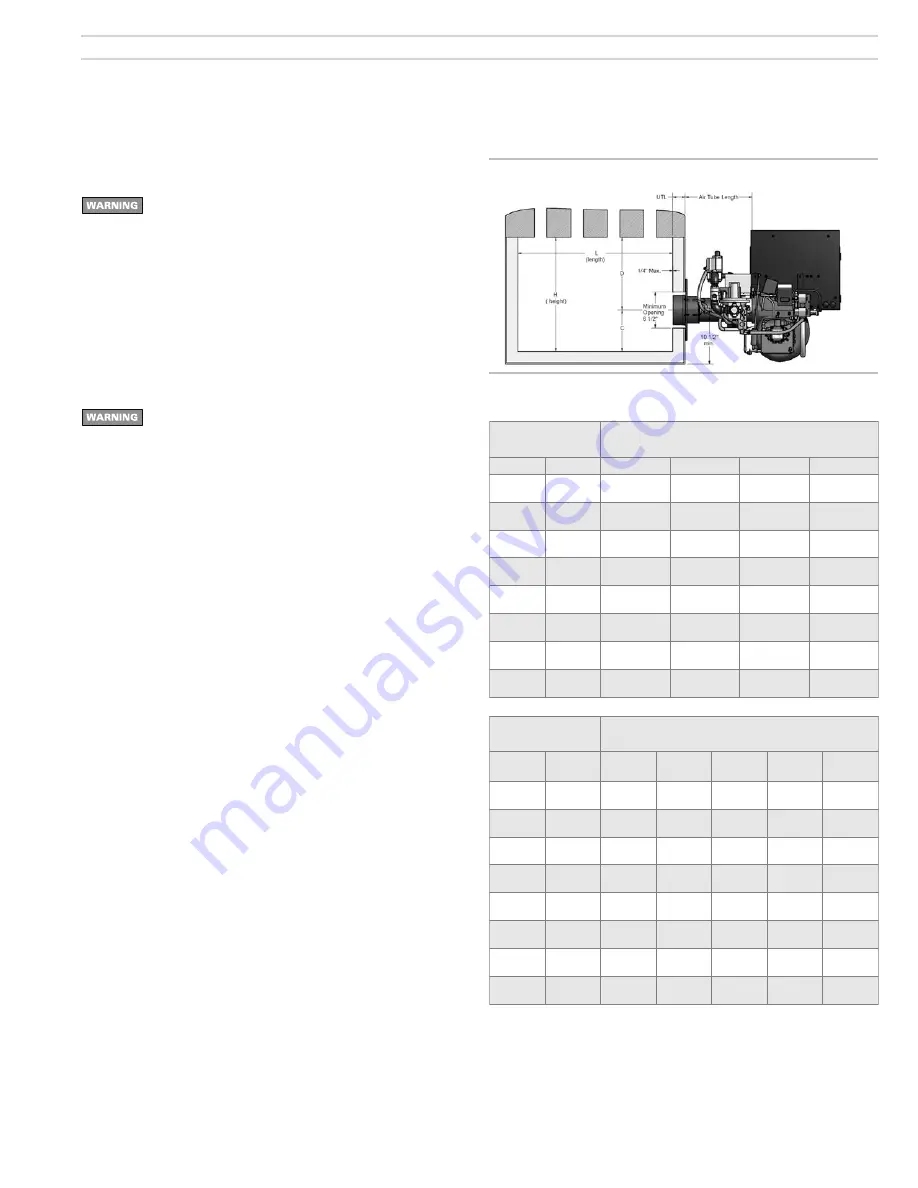
Model 702G/O Advanced gas/oil burners — Instruction manual
Carlin part number MN702GO Rev. 06/23/14
– 9 –
Where appliance instructions differ from this manual, follow the appliance instructions.
2. Prepare site • assemble burner • mount burner
(continued)
Figure 3
Chamber dimensions & tube configurations
Table 2
Minimum combustion chamber dimensions
(see Figure 3)
Prepare burner and components
Do not install or operate the burner if any component is dam-
aged or if burner does not comply with the specifications of
Table 2 and other guidelines in this manual.
Combustion chamber minimum dimensions
1.
For applications that have not been specifically tested (OEM applications),
verify that the combustion chamber provides the minimum dimensions
shown in Table 2 and Figure 3. For specific OEM applications, the
appliance testing ensures suitability of the chamber.
2.
Chamber dimensions may be larger than listed in Table 2, but should
not be excessively large.
Combustion chambers should be sized as recommended in
Table 2. They should be constructed of refractory materials
with the capacity to withstand 2600°F or higher.
It is difficult to include all possible chamber constructions in this
manual. Therefore, you should use the information presented
in this manual combined with commonly practiced techniques
when determining chamber design. If certain conditions are in
question, consult the factory.
Using chamber linings
1.
When using refractory liners or lightweight chambers, use insulating-
type refractory rated 2600°F minimum, or as specified by the appliance
manufacturer.
2.
You must install a target wall liner if flame length is close to the length
of the chamber.
3.
Use a floor liner when possible. The floor liner will improve firing in most
applications. Extend floor liner 3 to 4 inches up the side walls.
4.
Target wall liners — Extend target wall liners at least 3 to 4 inches above
the center of the flame corbel the top 1½ to 2½ inches deep.
5.
Use preformed chamber liners when available. Lining the floor and tar-
get wall water-backed combustion chambers with lightweight insulating
refractory will accomplish the same.
6.
When converting coal-fired units, install a combustion chamber in the
ashpit area, or fill the ashpit with sand up to 2 inches above the “mud
ring” of the boiler (firing through the door). Install a lightweight refractory
liner on the target wall.
Air tube insertion length (UTL)
1.
Usable air tube length (UTL) is the distance from mounting flange to end
of air tube. Verify that the end of the air tube will be flush with, or no more
than ¼ inch short of, the inside of the appliance combustion chamber front
wall when the burner is mounted. See Figure 3 for further information.
High fire input
Refactory combustion chamber applications
(all dimensions in inches)
Oil–GPH
Gas–MBH
“L”
“W”
“C”
“H”
6.00
840
21
15.0
7.5
15
6.50
910
23
15.5
8.0
16
6.90
966
25
16.0
8.0
16
7.80
1092
28
17.0
8.5
17
8.70
1218
31
17.5
9.0
18
9.50
1330
34
18.0
9.0
18
10.40
1456
38
19.0
9.5
19
11.20
1568
43
20.0
10.0
20
High fire input
Refactory combustion chamber applications
(all dimensions in inches)
Oil–GPH
Gas–MBH
“L”
W/ target
“L”
No target
“W”
“C”
“D”
6.00
840
21
25
17.0
8.5
10.5
6.50
910
23
27
17.5
9.0
11.0
6.90
966
25
29
18.0
9.0
11.0
7.80
1092
28
32
19.0
9.5
11.5
8.70
1218
31
35
19.5
10.0
12.0
9.50
1330
34
38
20.0
10.0
12.0
10.40
1456
38
42
21.0
10.5
12.5
11.20
1568
43
47
22.0
11.0
13.0