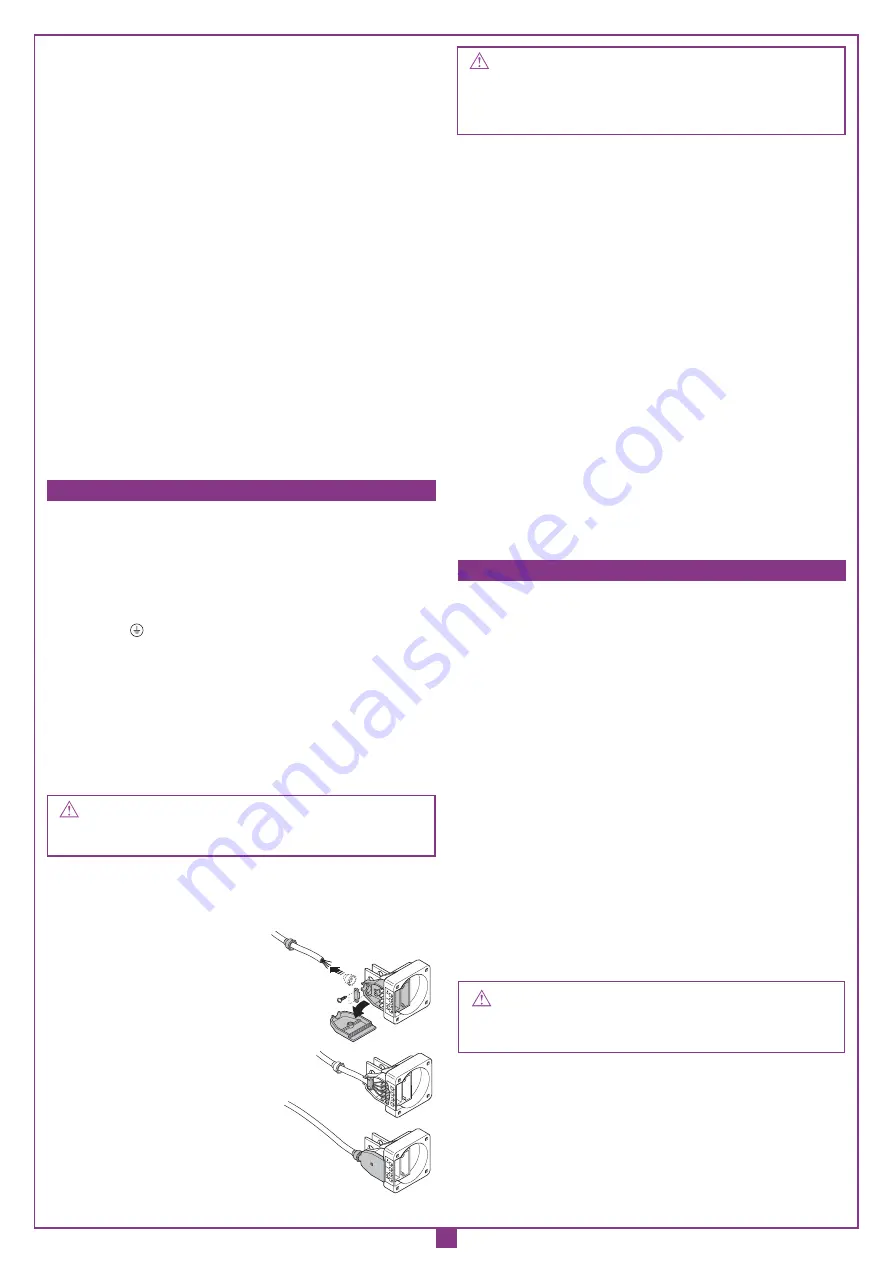
17
12
3
12
3
12
3
IMPORTANT! The geared motor is not fitted with a torque
limiter. Only use an electronic programmer which has a torque
limiter with maximum force at the head of the gate equal to
150N (local standards and regulations in force).
SETTING THE MOTOR TORQUE (see ECU)
When carrying out the installation you are advised to use a Cardin
ECU
fi
tted with a torque limiter.
The Cardin programmers optimise the correct working order of the
"machine" (motorised gates/doors) and guarantee full power maxi-
mum thrust at the start of the opening/closing manoeuvre).
The programmer also guarantees that the effective torque fed to the
system will be that selected by the operator in the ECU. The choice
of settings depends on the weight and size of the gate leaf/door and
the different environmental conditions on-site.
You are reminded that the standards and regulations in force
unequivocally require that the torque be set to a level suitable
for the system.
Correctly choosing the torque will guarantee maximum security
and long life for the mechanical components.
SETTING THE MECHANICAL TRAVEL LIMIT (
fi
g.3 pag.3)
The model 200/BL202C is
fi
tted with adjustable mechanical travel
limits "7" and "10". Loosen the fastening screws and move the
rings "7" and "10" to the desired opening and closing positions
then tighten them carefully.
Releasing the gate should only be carried out when the motor
has stopped because of blackouts.
To release the gate use the plastic key supplied with the appliance.
It should be stored in an easily accessible place, at home or on
the appliance itself using the key slot (pos.5
fi
g.12).
To release the gears
- open the lock mechanism cover by pressing on the sides (fig
12a-12b);
- insert the release key and turn it through about 30 degree
(
fi
g. 12c). The gears will be released and the lock cylinder will
rise;
- if you wish leave the gears released, just close the lock cylinder
cover (
fi
g. 12e).
To lock the gears
- remove the key (fig.12d), close the cover and press down with
the palm of your hand until the gears are locked;
- keep the key in a safe place.
Note: To make the operation easier the gate can be moved slightly
if required.
Don't force the locking mechanism, if you encounter
resistance move the gate slightly to allow the cogs to
slot together more easily within the geared motor.
gate), fasten the 4 screws "2" positioned on the geared motor
(tighten them well down) and insert the plastic end cap "5"
using the four supplied screws (
fi
g.2 pag.3).
• Rotate the never ending screw (part. 4 fig. 3) until it reaches
15mm from the end of the closing direction travel distance.
• Fix the arm to the rear mooring bracket "6" using the retaining
pin "1" (
fi
g.3 pag.3).
• Move the arm to its normal operating position, rest the head
against the gate and mark the position of the front bracket
"6".
Note: Make sure the operator is perfectly level (using a spirit
level).
- position the front holding bracket (
fi
g.14 pag.7)
• The front bracket may be
fi
xed in the following positions:
- on the gate frame or on a horizontal cross beam,
- if this is not possible,
fi
x a reinforcing plate to the gate structure
and then fasten the front bracket onto the reinforcing plate.
• Insert the retaining pin of the never ending screw "4" into the
front bracket "9" and fasten down using the supplied screw
and washer "8" (
fi
g.3 pag.3).
• With the motor released move it manually to the fully open
position and check that all the components work correctly.
• If you are using 200/BL202C with a gate from 1,8 to 3m in
width an electric locking device must be fitted to ensure that
the gate is blocked when it is closed.
Before connecting the appliance make sure that the voltage and
frequency rated on the data plate conform to those of the mains
supply.
• The appliance works off a single phase 230V 50Hz power supply
(see wiring diagram).
• The geared motor must be earthed, to this end use the binding
post marked which can be found on the wiring box.
• Do not use cables with aluminium conductors; do not solder the
ends of cables which are to be inserted into the binding posts;
use cables which are marked T min 85°C and are resistant to
atmospheric agents.
• The power cable must have enough slack to make sure it is not
pulled tight during normal operation.
• Insert a shunt box (
fi
tted with cable clamps) near each motor.
• The power cable must not be wound around any of the appli-
ances components and must not be cemented into the wall.
An all pole circuit breaker with a minimum of 3mm between
the contacts must be installed between the electronic program-
mer and the mains supply.
• Connect the supplied capacitor between the live wires 2 and
3 of the geared motor (
fi
g. 19-21 pag. 9-11).
Power cable rubber sealing cap
1) Fit the sealing cap on to the power
cable and slide it down enough to
allow you to connect the cable to the
terminal board.
2) Fasten down the cable using the cable
clamp.
3) Close the cover and slide the sealing
cap up over the cable entry opening.
This action is extremely important and will
guarantee a protection grade of IP44.
ELECTRICAL CONNECTION
(
fi
g. 19-21 page 9-11)
MANUAL RELEASE MECHANISM
(
fi
g.12, page 6)