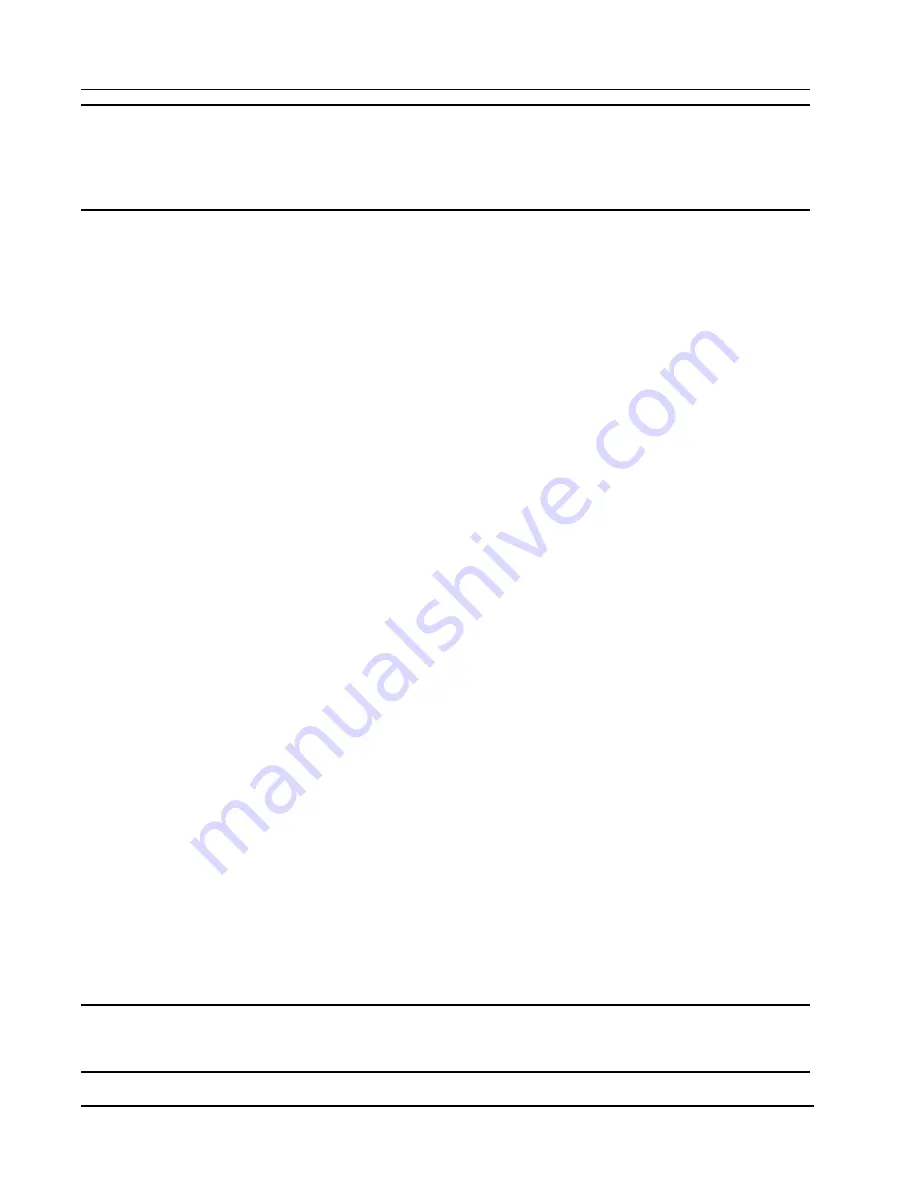
50
Section 2
Scanner
®
2000 microEFM
Important If the process fluid does not present an environmental risk and is stable when depressur
-
ized, it may be used to bleed air from the lines. If the process fluid can contaminate the
environment, or is highly volatile when depressurized as with liquified gases, a different
seal fluid should be used to fill the legs. An ideal seal fluid is one that does not dissolve
in the process fluid.
Bleeding with Process Fluid
g.
Make sure the shut-off valves in the tubing near the meter pressure taps are closed, and the meter is
filled with process fluid.
h. Open the equalizer and bypass/block valves on the block manifold. Make sure the vent valve is
closed.
i. Open one of the shut-off valves near the meter.
j. Slowly loosen the corresponding vent screw on the MVT, and throttle the rate of flow from the vent
with the shut-off valve.
k. When air bubbles are no longer visible around the MVT vent, tighten the MVT vent screw.
l. Repeat steps a through e for the other leg.
Bleeding with a Different Seal Fluid
m. Make sure the shut-off valves in the tubing near the pressure taps are open.
n. Open the equalizer and bypass/block valves on the block manifold. Make sure the vent valve is
closed.
o. Remove the vent screw from one side of the MVT and insert a fitting to allow connection of a hand
pump or funnel. If a funnel is used, attach a length of Tygon tubing that is long enough to elevate the
funnel well above the meter pressure taps to force the fluid up the legs.
p. Connect a hand pump or funnel to the fitting.
q. Estimate the amount of fill fluid required to fill the tubing and push any air bubbles into the meter.
r. Pour fill liquid into the funnel, tapping the tubing occasionally to dislodge any bubbles.
s. When the leg is full of fluid, remove the fitting from the vent of the MVT and quickly replace the vent
screw and tighten.
t. Repeat steps a through g for the other leg.
6.
Perform a manifold leak test as described on
7. Verify the zero offset, if required (and other calibration points, if desired). See the ModWorX™ Pro Soft
-
ware User Manual, Part No. 9A-30165025, for complete instructions. See also
or Differential Pressure), page 56, Static Pressure Calibration and Verification, page 56
sure Calibration and Verification, page 57
CAUTION Do not put the Scanner into operation until the valves are positioned properly so that
pressure is supplied to both sides of the MVT. For instructions on proper valve positions,
see
Placing the Scanner into Operation, page 58
.
Содержание Scanner 2000 microEFM
Страница 1: ...NUFLO Scanner 2000 microEFM Hardware User Manual Manual No 9A 30165023 Rev 10 ...
Страница 26: ...26 Section 1 Scanner 2000 microEFM ...
Страница 104: ...A 18 Appendix A Scanner 2000 microEFM ...
Страница 106: ...B 2 Appendix B Scanner 2000 microEFM ...
Страница 188: ...E 10 Appendix D Scanner 2000 microEFM ...
Страница 190: ...R U S S I A 603 5569 0501 ms kl c a m com ...