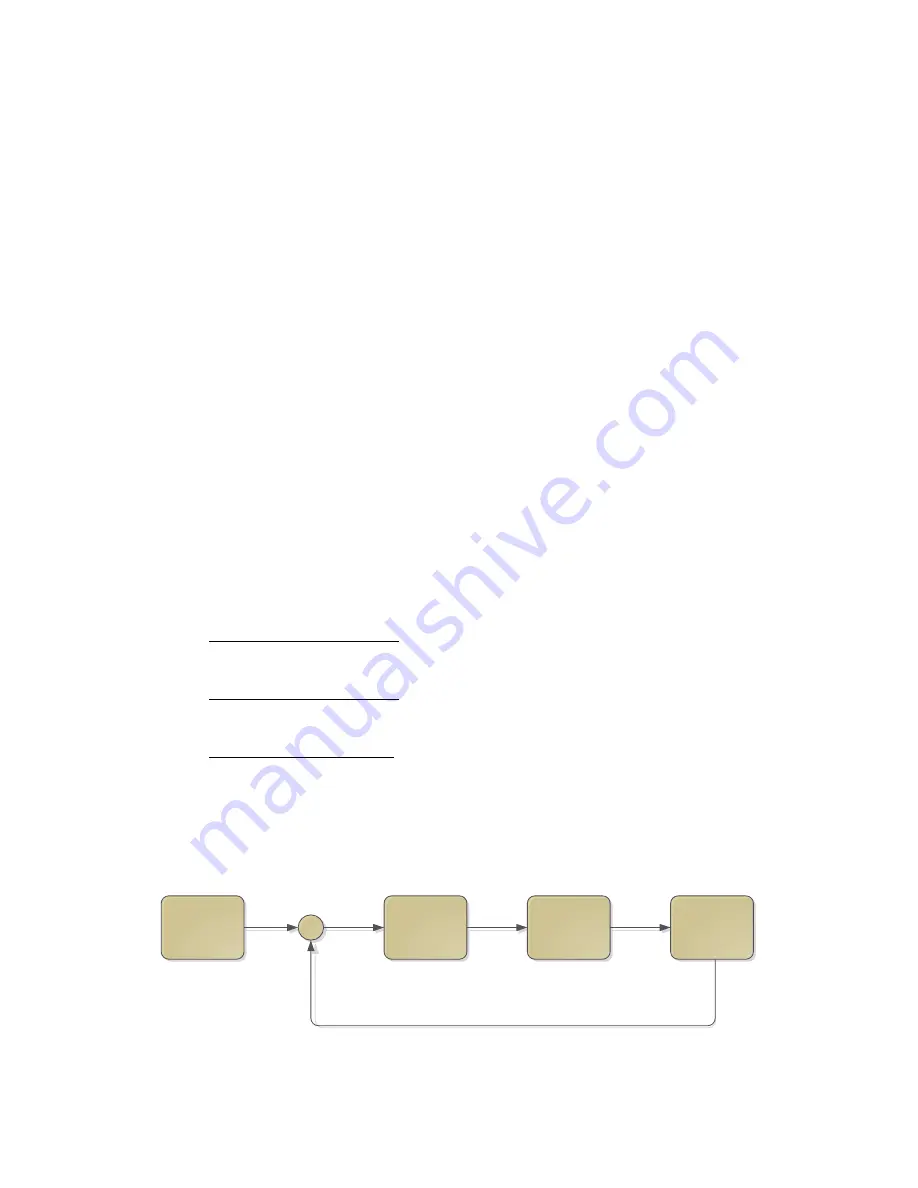
24
/ 55
stabilizes the DC link voltage. After that, the output side will measure the actual output state
(voltage levels) and will start the control algorithms and PWM.
This state can evolve to Standby state when a Not enable signal is received, to Ready state
when a Not run signal is received or to Alarm state if an error condition is detected.
Please, note that, while the power supply is in Run state, it is not possible to change the
connection mode from independent channels to parallelized channels.
4.2.6.
Alarm
In this state, the power supply is stopped and kept in a safe condition: the DC link is discharged
and the PWM signals are stopped.
The Alarm state can be reached by any fault detected during the normal operation of the
power supply, for instance, an emergency stop activation (see
Alarms
chapter for further
detail).
The only possible transition from Alarm state is to Initialization state. Once in Alarm state a
Reset signal is required from the customer after clearing the fault condition. If the fault
condition has not been cleared the power supply state will be kept in Alarm (for example,
when heatsink overheating has occurred and the temperature is still high).
4.3.
Operation modes
The DC Programmable power supply has 3 operation modes:
-
Constant Current mode (CC): the power supply regulates the output current to the
setpoint defined by the user.
-
Constant Voltage mode (CV): the power supply regulates the output voltage to the
setpoint defined by the user.
-
Constant Power mode (CP): the power supply regulates the output power to the
setpoint defined by the user.
4.3.1.
Current mode
The current mode is based on a PID controller with dynamic saturation limits which depend on
the current limit configured. Find below the current regulation block diagram:
PID
PWM
Converter
Current feedback
Current
setpoint