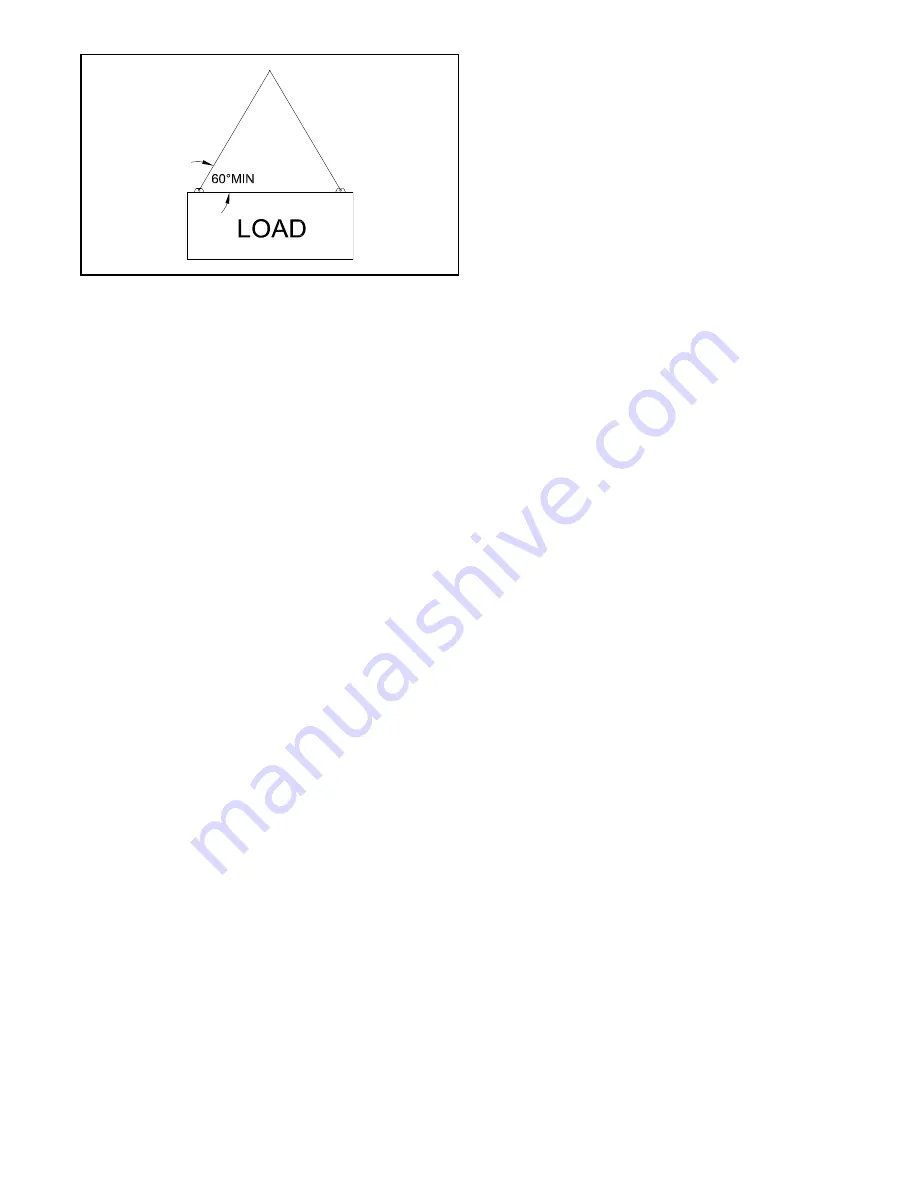
9
The unit should be located in the boiler room
so as to provide ease of venting and adequate
clearance for maintenance, serviceability and
installation of piping.
The tube pull space listed in the Burnham
Commercial product catalog must be provided
at the front of the boiler. The coil pull space must
be maintained at the front of units equipped with
tankless coils. Floor construction should have
adequate load bearing characteristics to bear
the weight of the boiler filled with water. A boiler
foundation is recommended if the boiler room
floor is weak, uneven or if a water condition
exists. These boilers are not for installation on
combustible flooring.
B. Installation Clearance
Minimum clearances to combustible walls shall
be as follows:
1. Models 4FH-63A thru 180: 6
"
sides, rear and
above
2. Models 4FH-209A thru 3075A: 18
"
sides, rear,
and above
3. Minimum recommended service clearances:
18
".
See boiler submittal drawings for tube pull
clearance requirements.
If desiccant package was ordered, be sure
to remove from the boiler furnace using the
rear access, and from the waterside using the
manhole cover.
4. FLUE OUTLET, STACK, AND BREECHING
The maximum weight limit on the boiler flue outlets
is as follows:
1. Series 4FH: 250 lb
2.
All stack/economizer weights exceeding the limits
above will need to be independently supported.
Stack design: The stacks shall be installed in
compliance with NFPA 54, ANSI Standard
Z223.1, state and local codes, using a category
III product for positive, non-condensing
appliances. The boiler flue outlets are generally
sized for the correct stack diameter, but there
are exceptions to this.
The 4FH Series boilers are equipped with a flue
outlet stub to accept a slip-on stack connection.
The boilers are optimally designed to run with a flue
outlet pressure of .10-.30”wc pressure. The stack
design, taking into account the draft effect and all
friction losses, should arrive at 0.0
"
wc +/- .10
"
wc
pressure at the inlet. Horizontal runs should be kept
to a minimum. This will ensure the boiler will meet
the maximum capacity, and will light off and have
stable and consistent combustion.
On installations where a natural draft stack is used,
causing high breeching drafts, the boiler locking
blade damper (on boilers equipped with one) may
require adjusting, or one may need to be installed at
the boiler breeching. In multiple boiler installations,
or in installations where the breeching draft may vary
considerably, automatic draft controls in combination
with a motorized damper may be required.
5. COMBUSTION AIR REQUIREMENTS
All boiler rooms must be adequately vented to
provide enough combustion air to the boiler for proper
tuning and operation, to prevent oxygen depletion,
possible carbon monoxide formation, possible
accumulation of fuel fumes, and possible equipment
explosions. A free flow of combustion air will aid the
proper operation of the burner and allow for proper
venting of the boiler. The instructions below must be
followed to properly size make-up air openings in the
boiler room. Consult NFPA-54 National Fuel Gas Code,
NFPA-31 Installation of Oil Burning Equipment for more
detailed explanations, and local codes for additional
guidance for boiler rooms below grade and other
specific situations.
Two general methods may be used:
1. When one permanent opening is used: The
opening shall commence within 12
"
of the top
of the enclosure (boiler room) and the opening
shall communicate directly with the outdoors,
or through a vertical or horizontal duct with the
outdoors. The opening shall have a minimum
free area of 1 sq in per 3,000 BTU/hr total input
of all equipment in the enclosure, and not less
than the sum of the areas of all equipment vent
connectors.
2. When two permanent openings are used: One
opening location shall begin within 12
"
of the
top of the enclosure, and the other opening
location shall begin within 12
"
of the bottom of
the enclosure. When communication is directly
with the outdoors, or through vertical ducts, each
opening shall have a minimum free area of 1 sq
in per 4,000 BTU/hr total input of all equipment
in the enclosure. Where communicating with the
outdoors through horizontal ducts, each opening
shall have a minimum free area of 1 sq in per
2,000 BTU/hr total input of all equipment in the
enclosure.
Содержание 4FHL-107A
Страница 14: ...14 FIGURE 4 TS 71 130 D INSTALLATION INSTRUCTIONS FIGURE 3 TS 71 176 B...
Страница 15: ...15 TS 71 131 D FIGURE 5 TS 3 101 4 INSTALLATION INSTRUCTIONS FIGURE 6...
Страница 26: ...26...
Страница 27: ...27...