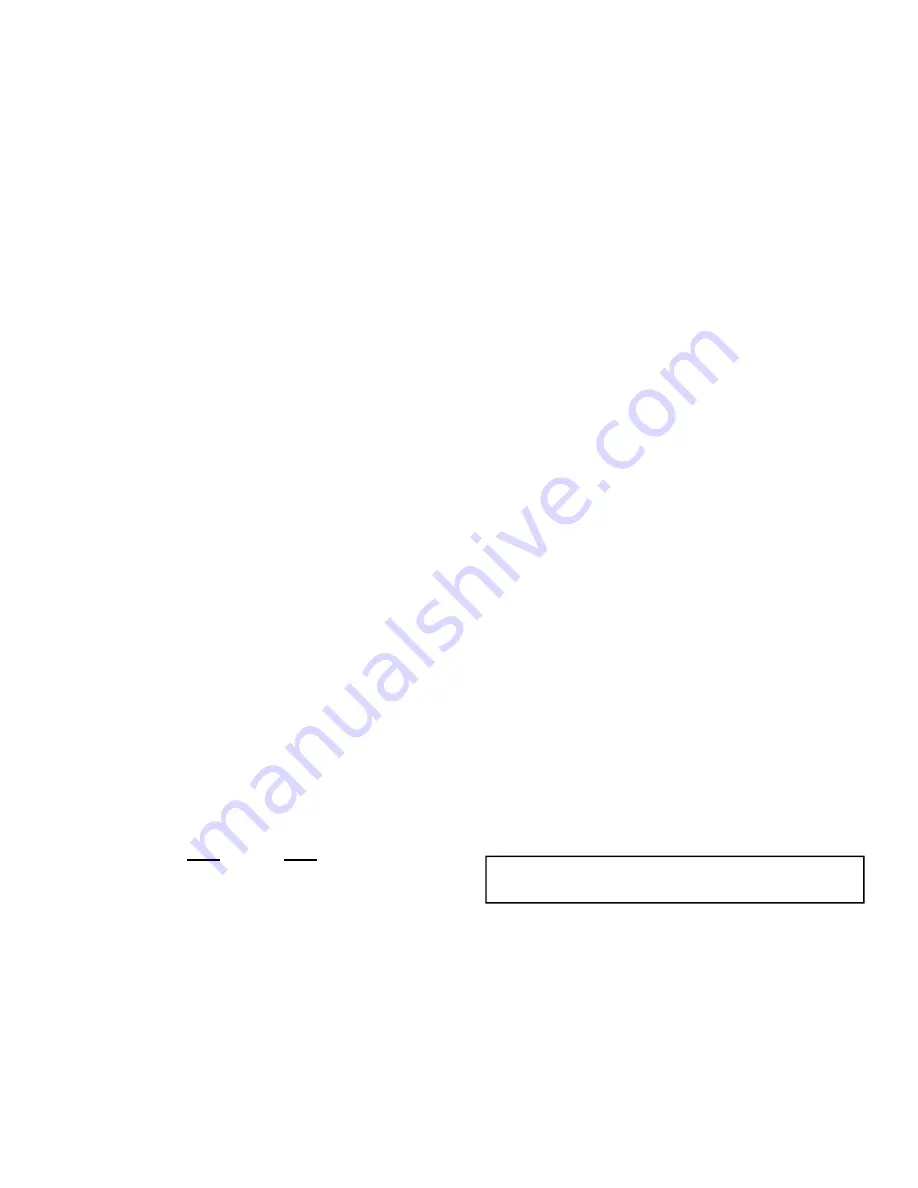
37
Damper Movement
Damper movement from full open to full closed (or vice versa)
takes 2
1
/
2
minutes.
Thermostats
The EconoMi$er IV control works with conventional thermo
-
stats that have a Y1 (cool stage 1), Y2 (cool stage 2), W1 (heat
stage 1), W2 (heat stage 2), and G (fan). The EconoMi$er IV
control does not support space temperature sensors. Connec
-
tions are made at the thermostat terminal connection board lo
-
cated in the main control box.
Occupancy Control
The factory default configuration for the EconoMi$er IV con
-
trol is occupied mode. Occupied status is provided by the black
jumper from terminal TR to terminal N. When unoccupied
mode is desired, install a field-supplied timeclock function in
place of the jumper between TR and N. When the timeclock
contacts are closed, the EconoMi$er IV control will be in occu
-
pied mode. When the timeclock contacts are open (removing
the 24-v signal from terminal N), the EconoMi$er IV will be in
unoccupied mode.
Demand Controlled Ventilation (DCV)
When using the EconoMi$er IV for demand controlled ventila
-
tion, there are some equipment selection criteria which should
be considered. When selecting the heat capacity and cool ca
-
pacity of the equipment, the maximum ventilation rate must be
evaluated for design conditions. The maximum damper posi
-
tion must be calculated to provide the desired fresh air.
Typically the maximum ventilation rate will be about 5 to 10%
more than the typical cfm required per person, using normal
outside air design criteria.
A proportional anticipatory strategy should be taken with the
following conditions: a zone with a large area, varied occupan
-
cy, and equipment that cannot exceed the required ventilation
rate at design conditions. Exceeding the required ventilation
rate means the equipment can condition air at a maximum ven
-
tilation rate that is greater than the required ventilation rate for
maximum occupancy. A proportional-anticipatory strategy will
cause the fresh air supplied to increase as the room CO
2
level
increases even though the CO
2
set point has not been reached.
By the time the CO
2
level reaches the set point, the damper will
be at maximum ventilation and should maintain the set point.
In order to have the CO
2
sensor control the economizer damper
in this manner, first determine the damper voltage output for
minimum or base ventilation. Base ventilation is the ventila
-
tion required to remove contaminants during unoccupied peri
-
ods. The following equation may be used to determine the per
-
cent of outside air entering the building for a given damper
position. For best results, there should be at least a 10 degree
difference in outside and return-air temperatures.
T
O
= Outdoor-Air Temperature
OA = Percent of Outdoor Air
T
R
= Return-Air Temperature
RA = Percent of Return Air
T
M
= Mixed-Air Temperature
Once base ventilation has been determined, set the minimum
damper position potentiometer to the correct position.
The same equation can be used to determine the occupied or max
-
imum ventilation rate to the building. For example, an output of
3.6 volts to the actuator provides a base ventilation rate of 5% and
an output of 6.7 volts provides the maximum ventilation rate of
20% (or base plus 15 cfm per person). Use Fig. 65 to determine
the maximum setting of the CO
2
sensor. For example, an 1100
ppm set point relates to a 15 cfm per person design. Use the 1100
ppm curve on Fig. 65 to find the point when the CO
2
sensor output
will be 6.7 volts. Line up the point on the graph with the left side
of the chart to determine that the range configuration for the CO
2
sensor should be 1800 ppm. The EconoMi$er IV controller will
output the 6.7 volts from the CO
2
sensor to the actuator when the
CO
2
concentration in the space is at 1100 ppm. The DCV set point
may be left at 2 volts since the CO
2
sensor voltage will be ignored
by the EconoMi$er IV controller until it rises above the 3.6 volt
setting of the minimum position potentiometer.
Once the fully occupied damper position has been determined,
set the maximum damper demand controlled ventilation poten
-
tiometer to this position. Do not set to the maximum position
as this can result in over-ventilation to the space and potential
high humidity levels.
CO
2
Sensor Configuration
The CO
2
sensor has preset standard voltage settings that can be
selected anytime after the sensor is powered up.
Use setting 1 or 2 for Bryant equipment.
1. Press Clear and Mode buttons. Hold at least 5 seconds
until the sensor enters the Edit mode.
2. Press Mode twice. The STDSET Menu will appear.
3. Use the Up/Down button to select the preset number.
4. Press Enter to lock in the selection.
5. Press Mode to exit and resume normal operation.
The custom settings of the CO
2
sensor can be changed anytime
after the sensor is energized. Follow the steps below to change
the non-standard settings:
1. Press Clear and Mode buttons. Hold at least 5 seconds
until the sensor enters the Edit mode.
2. Press Mode twice. The STDSET Menu will appear.
3. Use the Up/Down button to toggle to the NONSTD menu
and press Enter.
4. Use the Up/Down button to toggle through each of the
nine variables, starting with Altitude, until the desired set
-
ting is reached.
5. Press Mode to move through the variables.
6. Press Enter to lock in the selection, then press Mode to
continue to the next variable.
Dehumidification of Fresh Air with DCV (Demand Controlled
Ventilation) Control
If normal rooftop heating and cooling operation is not adequate
for the outdoor humidity level, an energy recovery unit and/or
a dehumidification option should be considered.
ECONOMI$ER IV PREPARATION
This procedure is used to prepare the EconoMi$er
®
IV for
troubleshooting. No troubleshooting or testing is done by per
-
forming the following procedure.
NOTE: This procedure requires a 9-v battery, 1.2 kilo-ohm resis
-
tor, and a 5.6 kilo-ohm resistor which are not supplied with the
EconoMi$er IV.
1. Disconnect power at TR and TR1. All LEDs should be off.
Exhaust fan contacts should be open.
2. Disconnect device at P and P1.
3. Jumper P to P1.
4. Disconnect wires at T and T1. Place 5.6 kilo-ohm resistor
across T and T1.
5. Jumper TR to 1.
6. Jumper TR to N.
7. If connected, remove sensor from terminals SO and +.
Connect 1.2 kilo-ohm 4074EJM checkout resistor across
terminals SO and +.
8. Put 620-ohm resistor across terminals SR and +.
9. Set minimum position, DCV set point, and exhaust poten
-
tiometers fully CCW (counterclockwise).
(T
O
OA
) + (T
R
x
RA
) = T
M
100
100
x
IMPORTANT: Be sure to record the positions of all
potentiometers before starting troubleshooting.
Содержание 547K
Страница 94: ...94 APPENDIX D WIRING DIAGRAMS Fig I 547K 04 06 Power Wiring Diagram 208 230 1 60 ...
Страница 95: ...95 APPENDIX D WIRING DIAGRAMS Fig J 547K 04 07 Power Wiring Diagram 208 230 3 60 ...
Страница 96: ...96 APPENDIX D WIRING DIAGRAMS Fig K 5047K 04 07 Power Wiring Diagram 460 575 3 60 ...