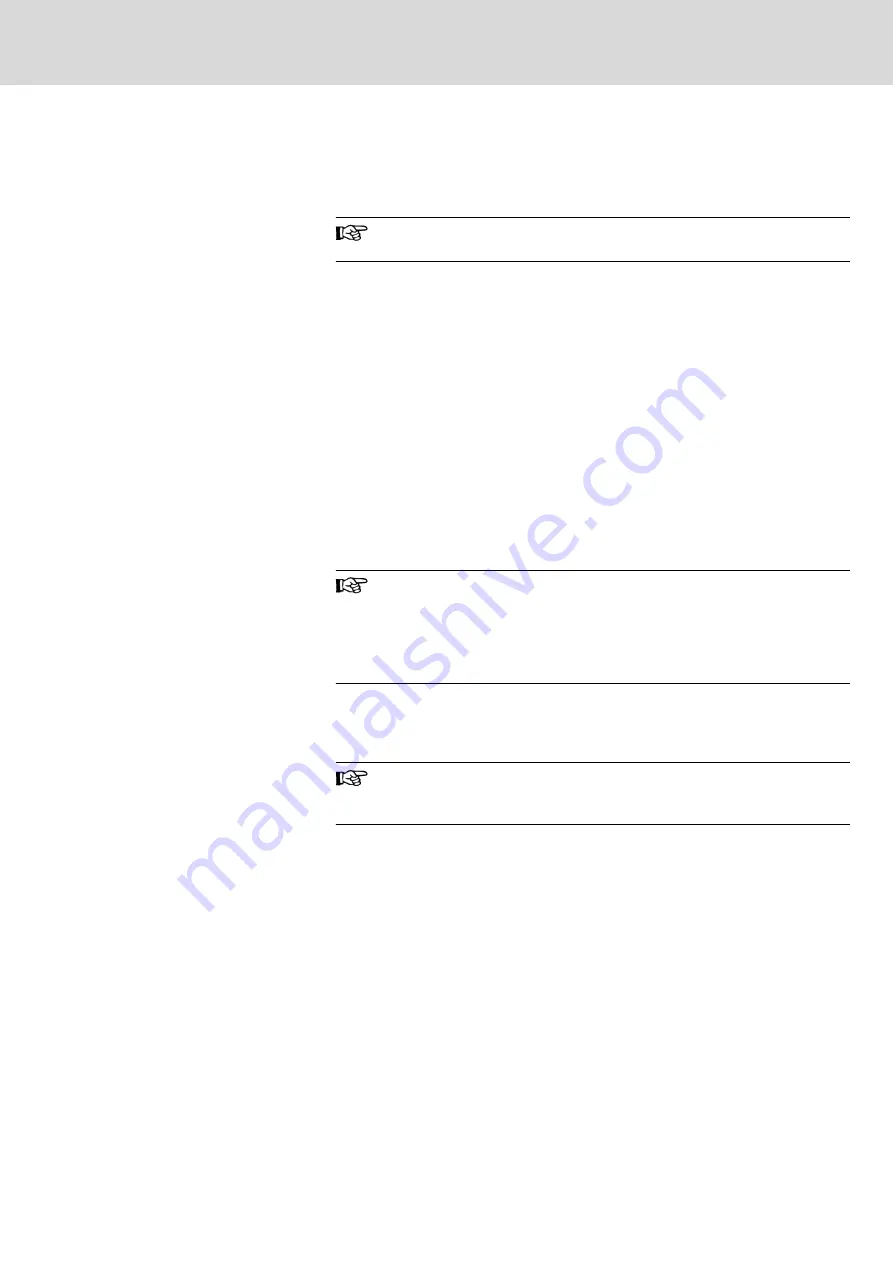
12.8
Mounting motor encoder and covers
After the stator has been fastened to the machine and the rotor to the shaft,
the encoder can be connected.
The motor encoder is not included in the scope of delivery of the
motor and must be provided by the user.
Essentially, the following steps have to be carried out:
1. Mount the motor encoder to the shaft.
2. Close the motor housing and the encoder installation space with the
provided covers.
3. Make the electric connection and the coolant connection according to
chapter 8 "Connection technique" on page 237
.
12.9
Parallel arrangement: Two motors on one shaft in connection
with a controller and an encoder
In a parallel arrangement, the motors are arranged on a shaft to be driven
one after the other.
The advantage of this mounting type is that it doubles the output motor tor‐
que, provided the motors are properly arranged and correctly activated.
The following examples start from the assumption that a radial ca‐
ble outlet is used on the stators. Because of bending radiuses
that have to be retained, an axial cable outlet or connection cable
with wires might require longer distances between two motors. Al‐
so refer to the instructions in
chapter 8.2.2 "Connecting the sta‐
.
Parallel arrangement - rotor as‐
sembly
At a point on their front face, all rotor sleeves are marked with an "S" (south
pole) for the row of magnets above them. This mark is at the same position
on all of the rotors.
If the rotor mark on the front face is covered after installation,
mark the point where the "S" is positioned on the rotor on your
machine for further assembly.
Both rotors have to be positioned on the shaft such that the "S" mark on the
rotors is always positioned on the same side (left or right) and at the same
point in the circumference.
This ensures that the hole pattern (front-face hole circle diameter with threa‐
ded holes) as well as the polarity of the magnets are aligned. This is the only
position in which the resulting motor torque can be transmitted optimally.
MBT High Synchronous Torque Motors
325/409
Installation
R911298798_Edition 08 Bosch Rexroth AG
Содержание rexroth MBT
Страница 1: ...MBT High Synchronous Torque Motors Project Planning Manual R911298798 Edition 08 ...
Страница 18: ...6 409 MBT High Synchronous Torque Motors Bosch Rexroth AG R911298798_Edition 08 ...
Страница 32: ...20 409 MBT High Synchronous Torque Motors Bosch Rexroth AG R911298798_Edition 08 ...
Страница 240: ...228 409 MBT High Synchronous Torque Motors Bosch Rexroth AG R911298798_Edition 08 ...
Страница 298: ...286 409 MBT High Synchronous Torque Motors Bosch Rexroth AG R911298798_Edition 08 ...
Страница 416: ...404 409 MBT High Synchronous Torque Motors Bosch Rexroth AG R911298798_Edition 08 ...
Страница 421: ...Notes MBT High Synchronous Torque Motors 409 409 ...