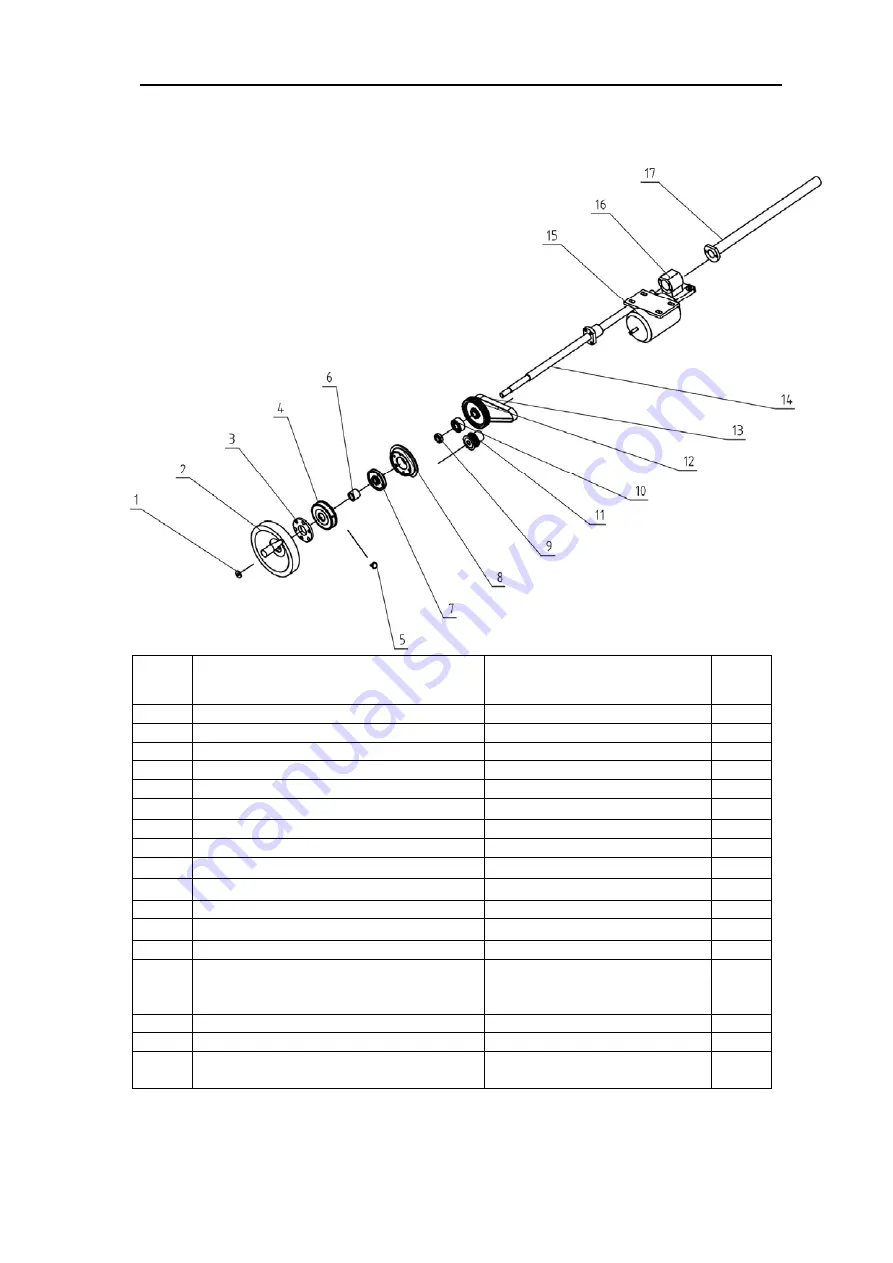
Operating Manual
70
Cross feed structure
No Code
Name
Qt.
1 FSG-4080R-23-313
Washer
1
2 FSG-2050M-23-503
Hand
wheel
1
3 FSG-2050M-23-302
Bearing
cover
1
4 FSG-4080R-23-316
Feed
dial
1
5
M818-10-312
Knurling set screw
1
6
FSG-4080R-23
-
307
Spacer
1
7 FSG-2050M-23-304
Sleeve
1
8 FSG-4080R-23-104
Vernier
dial
plate
1
9
M20
×
1.5/J14-4B
Round nut
1
10
3204A (47
×
20
×
20.6)/GB/T292-94
Bearing
1
11 FSG-2050M-23-106
Small
timing
pulley
1
12
FSG-2050M-23
-
105
Big time pulley
1
13 187L075/GB11616-89
Timing
belt
1
14 FSG-2550R-23-300
FSG-4080R-23-300
FSG-30100R-23-300
Cross lead screw
1
15
KT516
Cross feed motor
1
16
FSG-4080R-23-101
Feed nut bracket
1
17 FSG-30100R-23-301
FSG-4080R-23-310
Cross lead screw safe shield
1
Содержание WSG1640AHD
Страница 1: ...WSG1640AHD SURFACE GRINDING MACHINE OPERATING MANUAL ...
Страница 25: ...Operating Manual 17 In a short starting testing the grinding wheel spindle must rotate clockwise ...
Страница 66: ...Operating Manual 58 Circuit diagram ...
Страница 67: ...Operating Manual 59 ...
Страница 68: ...Operating Manual 60 ...
Страница 69: ...Operating Manual 61 ...
Страница 70: ...Operating Manual 62 ...
Страница 71: ...Operating Manual 63 ...
Страница 72: ...Operating Manual 64 ...
Страница 73: ...Operating Manual 65 ...
Страница 74: ...Operating Manual 66 ...
Страница 79: ...Operating Manual 71 Elevating structure ...
Страница 81: ...Operating Manual 73 HYDRAULIC CYLINDER ...