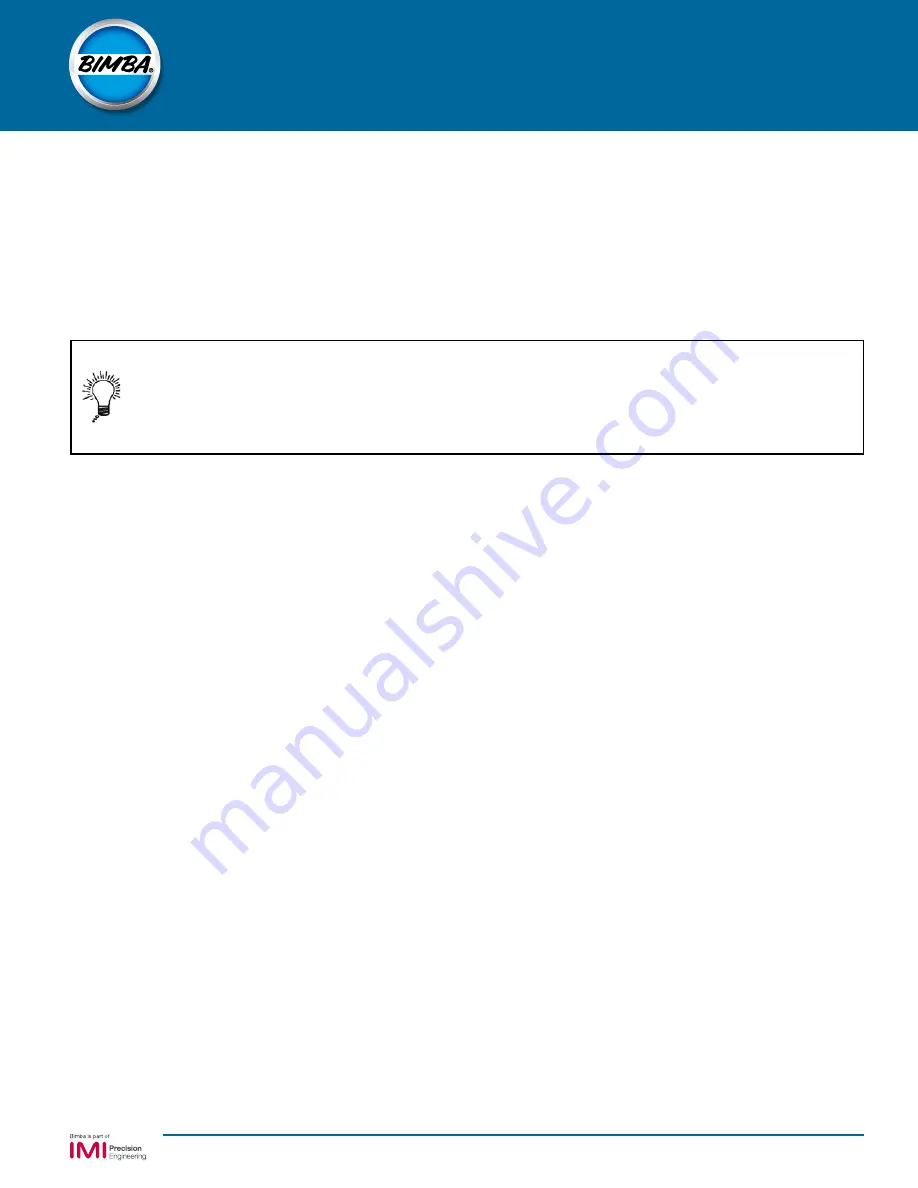
16
User Manual
Model PCS
Pneumatic Motion Control System
12. COMMAND THE BIMBA ACTUATOR TO ITS ZERO POSITION
We will command the PCS to move to different positions by adjusting the command signal input to TB4. First
command the PFC cylinder or the PTF rotary actuator to retract to the zero position by setting the analog
command input signal to 0 volts or 4 mA, depending on the setting of jumper J01. Either the cylinder will move
to its hard stop (either internal or external) or it will move to a point short of that stop.
13. PRELIMINARY “ZERO” ADJUSTMENT
PFC and PFCN cylinders and PTF rotary actuators greater than 180 degrees of rotation
(See below for PTF’s less than 180 degrees)
Adjust the Zero setting so that it coincides with the desired retracted or rotational position hard stop. First note
the two red and green LEDs on the PCS printed circuit board. If the PCS wants to move the actuator towards
the actuator zero position, but cannot due to a mechanical limitation, the red LED will stay on continuously
flicker. Look at the LEDs and make the adjustments described in one of the two following paragraphs.
If the Red LED is On
- (The Zero setting is currently set beyond the desired retracted or rotational position).
Adjust the Zero potentiometer CCW slowly, until the red LED goes off. (If the zero potentiometer was adjusted
too far and the actuator moved away from zero, adjust the Zero potentiometer CW just enough to move the
actuator back to the zero position. If adjusted too far, the red LED will come back on). Both LEDs should be off
when set correctly. This ends the preliminary Zero adjustment.
If Both LEDs are Off
- (The Zero setting is currently set somewhere in mid-stroke.) Slowly adjust the Zero
potentiometer CW to move the actuator toward the zero position. The red LED will flicker while being adjusted.
When the actuator hits the zero position, the red LED will continue to flicker even when the adjustment is no
longer being turned. Now adjust the Zero CCW just enough to turn off the red LED. Both LEDs should be off
when set correctly. This ends the preliminary Zero adjustment.
Note: Improve performance by not using the actuator end of stroke limit as a hard stop. (Eliminates
any potential stiction between the actuator piston and the end cap, as well as improves the
positioning capability at end of stroke or rotation). This can be accomplished by implementing
mechanical hard stops in the application fixturing or by using command signals greater than the set
zero position or less than full scale.