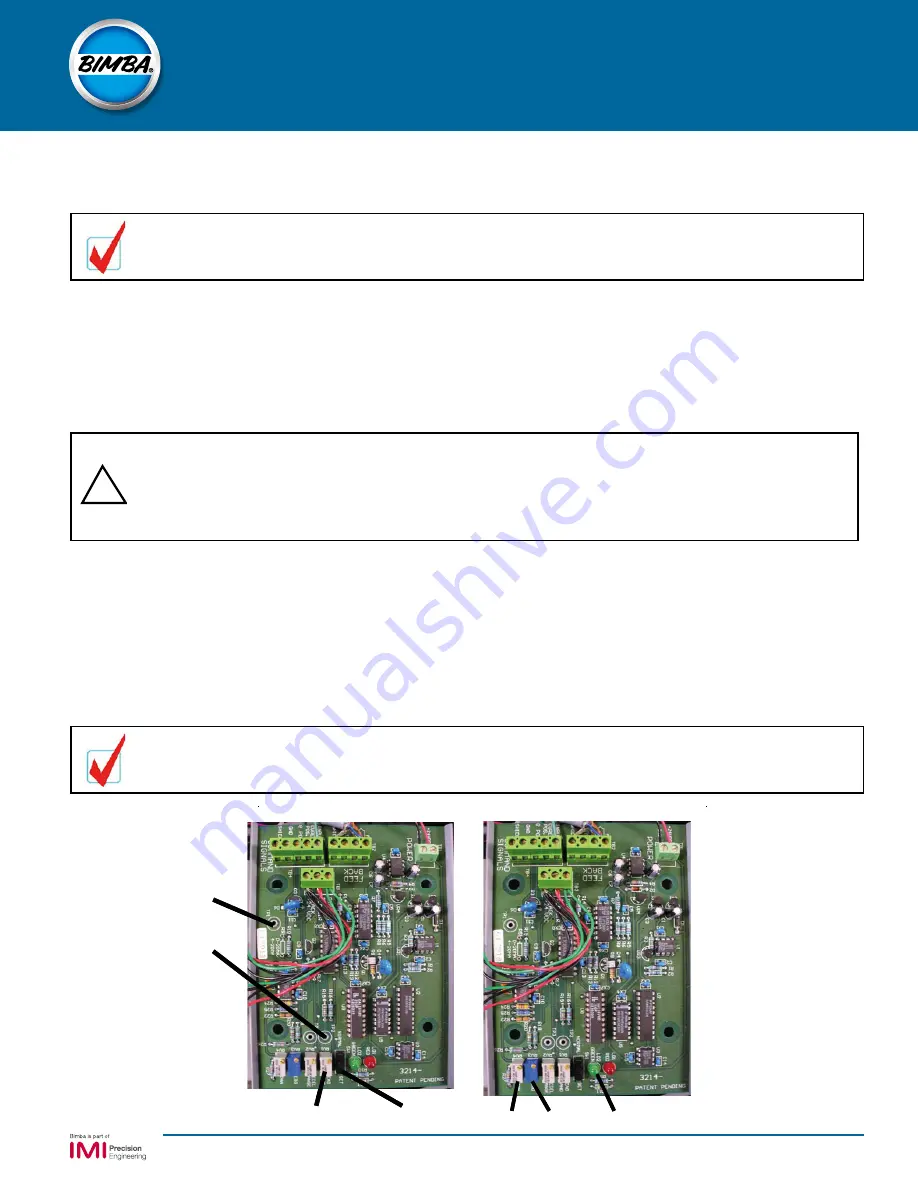
15
User Manual
Model PCS
Pneumatic Motion Control System
!
CAUTION!
If full system pressure is applied with a large error signal present, the actuator will attempt to in-
stantaneously move to the command signal position. This could potentially cause physical harm or
damage to application tooling. Once system is installed, always ensure that the command signal and
feedback signal are equal at start up or start system up at low pressure.
10. APPLY PNEUMATIC PRESSURE
Ensure the actuator is clear of all obstacles. Apply a low pneumatic pressure (20 psi). The actuator should
attempt to move. If no command signal is applied to the PCS, the cylinder will attempt to assume its zero
position. Once the cylinder has moved and stopped, raise the pressure to the normal operating pressure (70 to
80 psi). If the actuator does not move, it may already be at the zero position.
11. SET THE “DEADBAND”
The Deadband should initially be set according to the Application Sizing Chart. Move switch SW1 on the PC
Board from the NORMAL to the SET position. (see illustration on page 11 and the photo below). Set the digital
voltmeter to DC volts and measure the voltage between the Ground Reference Point (TP1) and TP2 on the
printed circuit board. Adjust the Deadband setting to the recommended minimum voltage setting shown in the
Application Sizing Chart.
Measure the voltage with a digital voltmeter at Terminal Block TB1 on the PCS PC Board. The
voltage must be between 23.5 VDC and 24.5 VDC for the system to function properly.
After the Deadband is set, the SW1 Switch must be returned back to the Normal
position or the PCS will not function.
Deadband
TP1
TP2
SW1
LED’s
Span
Zero