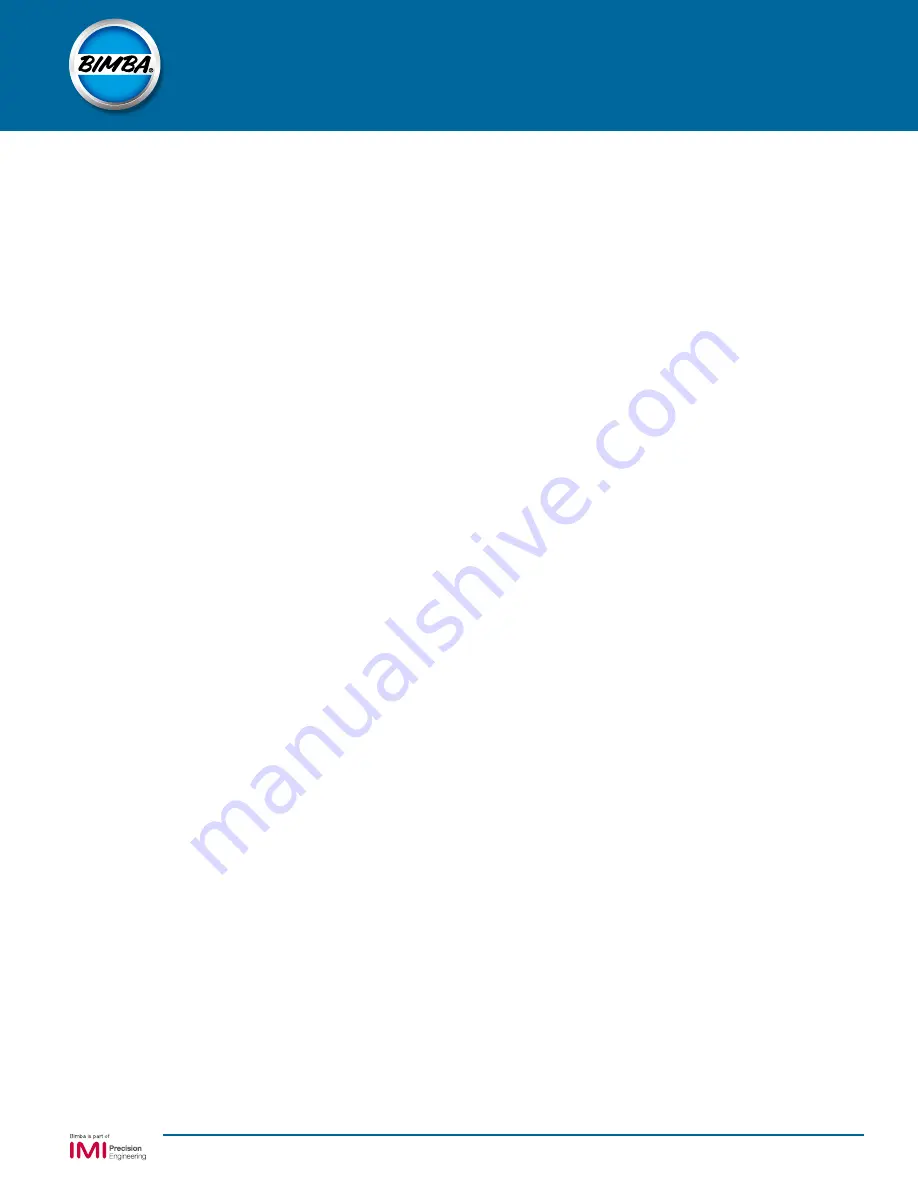
25
User Manual
Model PCS
Pneumatic Motion Control System
Problem:
The change in command signal is too small.
Solution:
Ensure that the change in command signal is large enough to cause the actuator to move outside
of the deadband. If the change in signal is too small (smaller than the adjusted deadband), the actuator will not
respond.
Problem:
The Zero adjustment is too high and/or Span adjustment is too low.
Solution:
Refer to the Installation Section of the manual that pertains to the Zero and Span Adjustments and
make the proper adjustments.
THE ACTUATOR IS NOT REPEATABLE OR STABLE
Problem:
PCS system parameters are not adjusted properly.
Solution:
Follow the Installation instructions to make the appropriate system adjustments for your application
parameters, ensuring that the deadband and decel adjustments are adjusted according to the application
requirements. Improper adjustments may cause actuator overshoot (deadband is too small), non-repeatability
(deadband is too big), sluggishness or instability.
Problem:
The actuator and PCS system are not sized properly.
Solution:
Refer to the Application Sizing Chart in the PCS catalog to ensure the actuator and PCS system are
sized properly for the application requirements.
Problem:
Noisy Command Signal.
Solution:
Provide an analog 0-10 VDC command signal that has less than 5 mV of ripple. Employ proper wiring
techniques to ensure signal noise is kept to a minimum (use shielded cables, proper grounding methods, etc.)
Problem:
The Electrical Power Supply is supplying less than the required 23.5 VDC. Utilize a DC power supply
that can supply the minimum 23.5 VDC required by the PCS. At voltages less than 23.5 VDC, the system
performance will degrade.
Solution:
Inadequately sized air line between the actuator and PCS valves. Application testing yielded best
results with 0.093 I.D. air line tube for
1-1/16” and 1-1/2” bore actuators and 0.170 I.D. air line tube for 2” bore actuators. Smaller or larger I.D. tubing
may result in less position repeatability.
Problem:
Air lines between the actuator and PCS valves are too soft or compliant. Avoid using soft easy to
expand air tubing. Use harder tubing such as nylon or metal.
Solution:
Air lines between the actuator and PCS valves are too long.
Longer air lines cause the system to be less accurate. Always use the shortest air lines as possible (< 18”). The
system will work with longer lines, but may not be stable or responsive enough for application requirements.
Option N allows you to mount the valves close to the actuator with the PCS electronics mounted separately.
Problem:
Air Supply pressure is too low (Below 70 psi)
Solution:
Turn air supply up to at least 70 psi. If the air supply experiences pressure drops due to excess air
demand in the building’s air supply system, an air reservoir may be required.