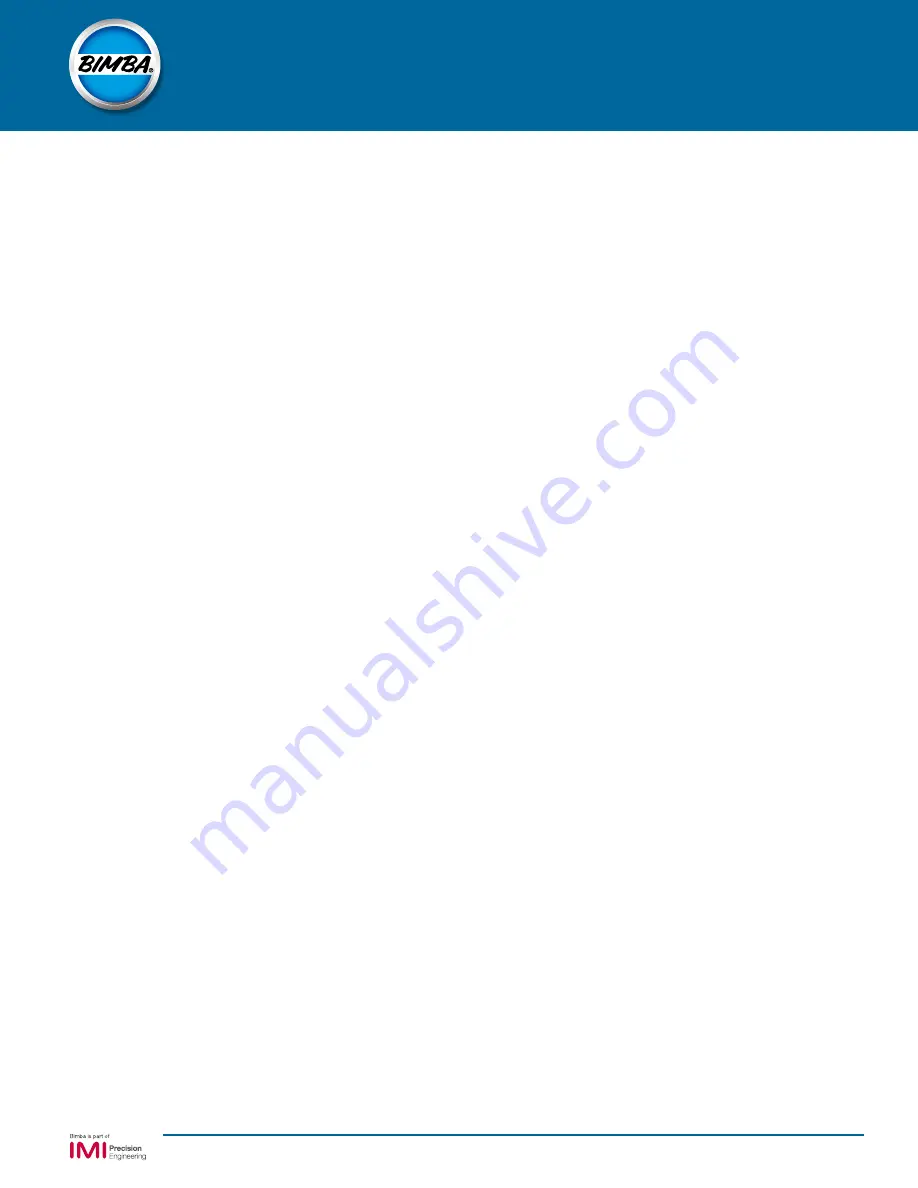
26
User Manual
Model PCS
Pneumatic Motion Control System
Problem:
Excessive air leak in the actuator or PCS system.
Solution:
Find and fix the leak. External fitting leaks are relatively easy to find. Use a solution, such as Leak
Tech, to identify leaks in fittings, couplings, and rod seal (if linear actuator). Check for leaks in the actuator seals.
Problem:
PCS valves are contaminated.
Solution:
Unfiltered air (>5 microns) can cause the valves to become contaminated causing them to leak. Use
a filter that is rated for <5 micron particles. Thread tape can also cause leaks in the valve if the tape becomes
loose and enters the system. It is recommended that a solid or liquid thread seal be used.
Problem:
The actuator feedback potentiometer is malfunctioning.
Replace the feedback potentiometer. See respective catalogs for part number information.
Problem:
Actuator seals are worn or contaminated.
Solution:
For PFC applications, order an RPFC (Cylinder with no probe) and replace existing cylinder (You may
use the existing probe if it is still in working order).
For PTF applications, order a seal repair kit (Part numbers are in the PTF catalog) and replace the worn or
contaminated seals.
Problem:
Excess friction is being exerted by application components.
Solution:
Reduce the friction to levels outlined in the installation section of the manual. External friction may
change as system components wear over time. Misalignment between the actuator and guiding system may
cause binding and increase friction to unacceptable levels.
Problem:
Varying loads in application.
Solution:
Stabilize the load variation. If loads cannot be stabilized, the deadband may need increased to
improve performance.
Problem:
Excessive velocity due to flow control misadjustment.
Solution:
Some applications require flow controls to limit velocity in order to attain required repeatability. The
flow controls may have been adjusted after initial settings were made. Re-adjust to proper settings.
THE ACTUATOR MOVES SLOWER THAN SIZING CHART INDICATES
Problem:
Inadequately sized air line between the actuator and PCS valves (tube diameter is too small).
Solution:
Application testing yielded best results with 0.093 I.D. air line tube for
1-1/16” and 1-1/2” bore actuators and 0.170 I.D. air line tube for 2” bore actuators. Smaller or larger I.D. tubing
may result in less position repeatability.
Problem:
The actuator and PCS system are not sized properly.
Solution:
Refer to the Application Sizing Chart in the PCS catalog to ensure the actuator and PCS system are
sized properly for the application requirements.