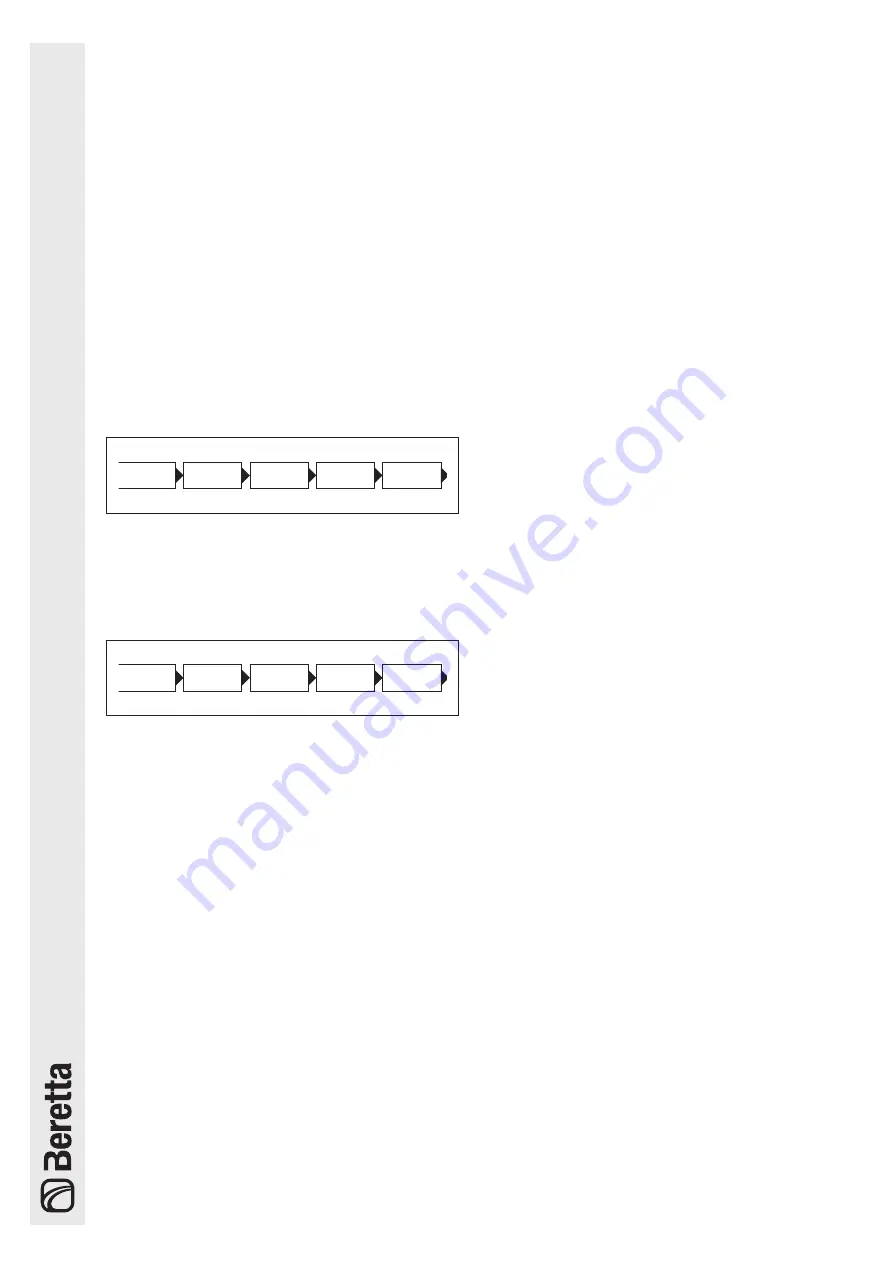
84
4.1.4 Setting the main parameters
Some parameters are essential in order for the system to operate in
cascade and setting these parameters is a determining factor for cor-
rect system operation.
b
The parameters described below must only be set on the Man-
aging module.
Par. 73 – Managing, Stand-alone mode
Parameter 73 defines how the thermal module is addressed and
serves to ensure that the signal from the secondary sensor is rec-
ognised.
You can set two values:
-
Managing:
to be set on the Managing module so that second-
ary sensor operation is activated.
NOTE: The secondary SC probe must be connected to the 13
terminals and 14 of the MO1 terminal block of the managing mod-
ule;
-
Stand Alone:
to be set on the Managing module so that sec-
ondary sensor operation is deactivated;
Boiler Cascade
Settings
(73) Stand
Alone Boiler
Boiler Settings
Settings
Home/Menu
screen
Par.147 – No. thermal modules
Parameter 147 defines the number of thermal modules in the system
(it is important to set the numer of connected modules for the system
to work properly). This parameter must only be set on the "Managing"
module.
Cascade
Module Config.
(147) Number
of Units
Boiler Settings
Settings
Home/Menu
screen
General operation
With cascade operation, the regulator of the managing module estab-
lishes a setpoint to be sent to the depending modules based on the
parameters 86-87, the difference between the setpoint value set and
the value read on the primary delivery manifold (or on the basis of par
176-177 and the difference between the setpoint value set and the
value read on the secondary delivery manifold).
On the basis of the setpoint received from the Managing module,
each module modulates based on its own PID (Par 16, Par 17 and
Par 18) as a function of the difference between the setpoint (sent by
the Managing module) and the value read by the delivery sensor on
the module itself.
b
The PID is a Proportional-Integral-Derivative control system
(abbreviated to PID) with retro-action. By reading an input val-
ue which determines the current value, it is able to react in the
event of a positive or negative error (difference between the
current value and the target value), tending towards 0. Reac-
tion to the error can be regulated through the terms "propor-
tional, integral, derivative".
Содержание 20141085
Страница 1: ...Installation Manual Modular system Power Max Box Installation Manual EN...
Страница 109: ...SYSTEM MANAGER 109...
Страница 110: ...SYSTEM MANAGER 110...
Страница 111: ...SYSTEM MANAGER 111...