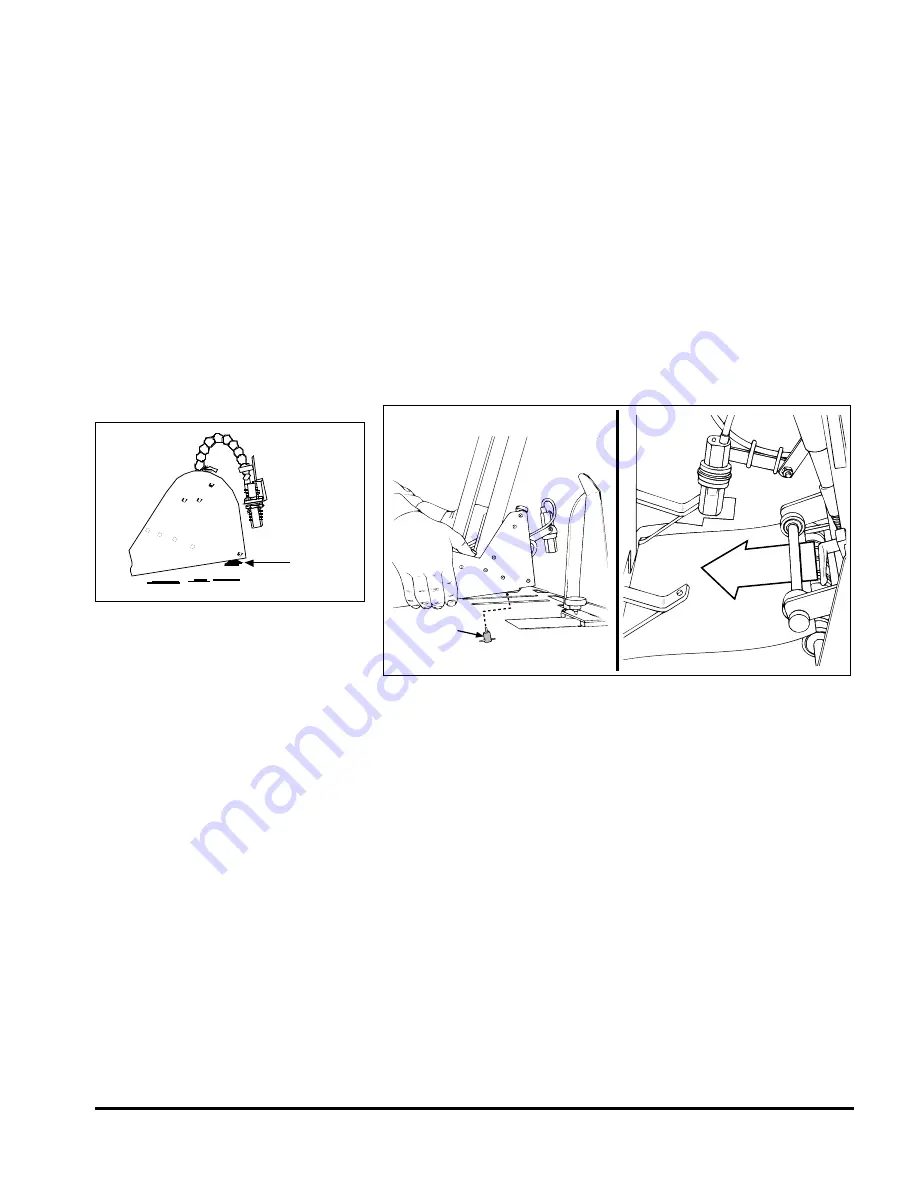
13
R
elaint
1500 M
anual
Figure 12. Aligning Feeder with Insert Station
STEP 7:
Aligning and
Securing Feeder to
Insert Station
• Using your finger, turn the drive belt to advance a piece of your
material through the gate assembly area and under the feeder hold
down springs.
• Continue advancing the material until the trailing edge of material
fits between the feeder exit rollers (.25 in. to .5 in., or 6.4 mm to
12.7 mm of material).
• Carefully slide the feeder into the inserter station and center the
leading edge of your material under the inserter hold-down springs.
Ensure the front edge of the material is in-line with the front hopper
plate. See Figure 12.
• Once you are satisfied with the feeder alignment, press down on the
feeder top plate to secure the feeder suction cups to the inserter rear
deck plate.
T-handle
screw
S uctio n
c up
Содержание Thiele Technologies Streamfeeder Reliant...
Страница 1: ...Manual Reliant 1500...
Страница 12: ...6 Reliant 1500 Manual...
Страница 36: ...30 Reliant 1500 Manual...
Страница 46: ...40 Reliant 1500 Manual...
Страница 49: ...43 Relaint 1500 Manual 8 Electrical Schematics 120V Electrical Schematic...
Страница 50: ...44 Reliant 1500 Manual 240V Electrical Schematic...
Страница 51: ...45 Relaint 1500 Manual 120V Electrical Schematic with Vacuum Select...
Страница 52: ...46 Reliant 1500 Manual 240V Electrical Schematic with Vacuum Select...
Страница 53: ...47 Relaint 1500 Manual 9 Mechanical Components...
Страница 57: ...51 Relaint 1500 Manual...
Страница 59: ...53 Relaint 1500 Manual...
Страница 61: ...55 Relaint 1500 Manual...
Страница 65: ...59 Relaint 1500 Manual...
Страница 67: ...61 Relaint 1500 Manual...
Страница 69: ...63 Relaint 1500 Manual...
Страница 70: ...64 Reliant 1500 Manual...
Страница 71: ......
Страница 72: ...2009 Thiele Technologies Inc Streamfeeder Printed in the USA...