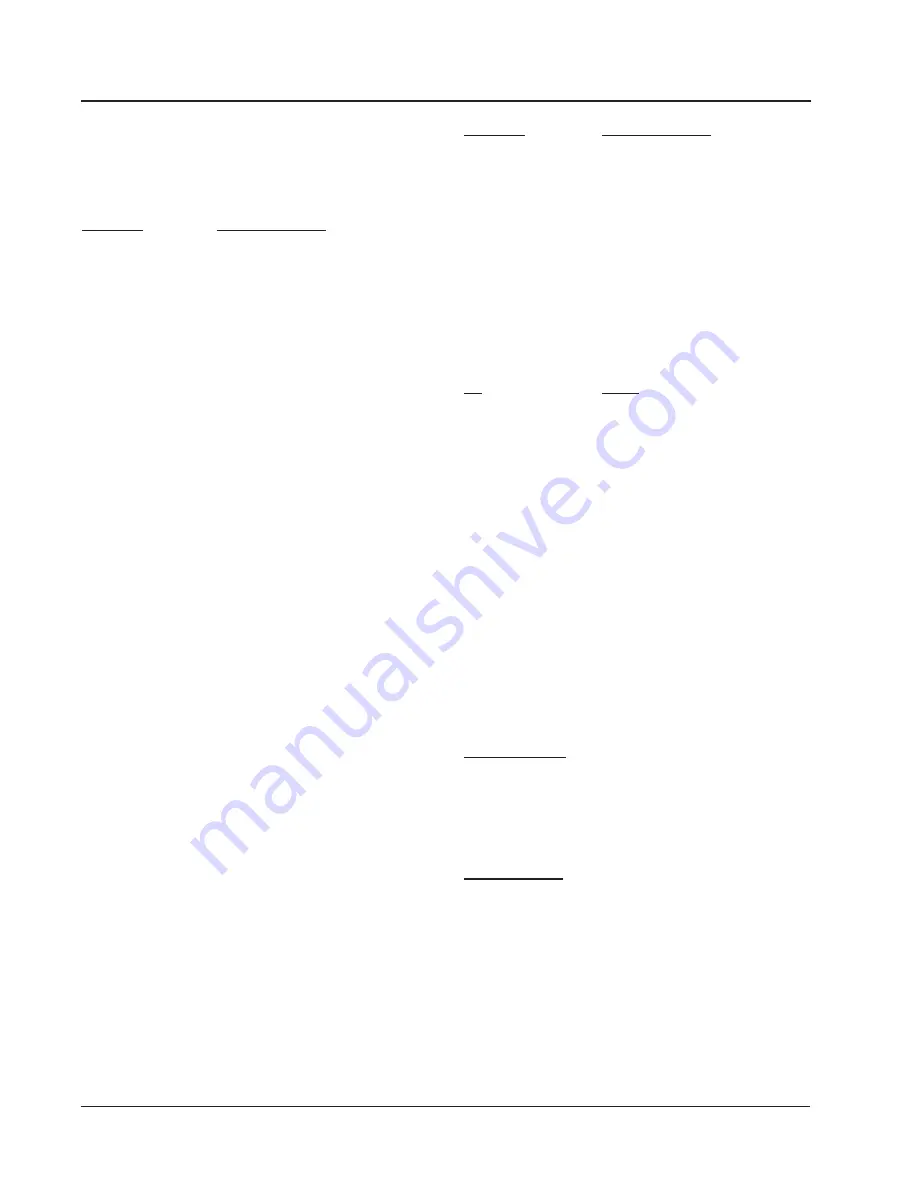
Manual 2100-603
Page
40 of 44
TROUBLESHOOTING ECM
™
MOTORS
CAUTION:
Disconnect power from unit before removing or replacing
connectors, or servicing motor. To avoid electric shock from
the motor’s capacitors, disconnect power and wait at least 5
minutes before opening motor.
Symptom
Cause/Procedure
Motor rocks slightly
•
This is normal start-up for ECM
when starting
Motor won’t start
•
Check blower turns by hand
• No movement
• Check power at motor
• Check low voltage (24 Vac R to C) at motor
• Check low voltage connections
(G, Y, W, R, C) at motor
• Check for unseated pins in connectors on
motor harness
• Test with a temporary jumper between R - G
• Check motor for tight shaft
• Perform motor/control replacement check
•
Perform Moisture Check
• Motor rocks,
• Check for loose or compliant motor mount
but won’t start
• Make sure blower wheel is tight on shaft
• Perform motor/control replacement check
Motor oscillates up
• It is normal for motor to oscillate with no load
& down while being
on shaft
tested off of blower
Motor starts, but
runs erratically
• Varies up and down
• Check line voltage for variation or “sag”
or intermittent
• Check low voltage connections
(G, Y, W, R, C) at motor, unseated pins in
motor harness connectors
• Check “Bk” for erratic CFM command (in
variable-speed applications)
• Check out system controls, Thermostat
•
Perform Moisture Check
• “Hunts” or “puffs” at
• Does removing panel or filter reduce
high CFM (speed)
“puffing”?
- Reduce restriction
- Reduce max airflow
• Stays at low CFM
• Check low voltage (Thermostat) wires and
despite system call
connections
for cool or heat CFM
• Verify fan is not in delay mode; wait until
delay complete
• “R” missing/not connected at motor
• Perform motor/control replacement check
• Stays at high CFM
• “R” missing/not connected at motor
• Is fan in delay mode? - wait until delay time
complete
• Perform motor/control replacement check
• Blower won’t shut off
•
Current leakage from controls into G, Y or W?
Check for Triac switched thermostat or solid-
state relay
Excessive noise
• Determine if it’s air noise, cabinet, duct or
motor noise; interview customer, if necessary
• Air noise
• High static creating high blower speed?
- Is airflow set properly?
- Does removing filter cause blower to slow
down? Check filter
- Use low-pressure drop filter
- Check/correct duct restrictions
Symptom
Cause/Procedure
• Noisy blower or cabinet
•
Check for loose blower housing, panels, etc.
• High static creating high blower speed?
- Check for air whistling through seams in
ducts, cabinets or panels
- Check for cabinet/duct deformation
• “Hunts” or “puffs” at
•
Does removing panel or filter reduce
high CFM (speed)
“puffing”?
- Reduce restriction
- Reduce max. airflow
Evidence of Moisture
• Motor failure or
• Replace motor and
Perform Moisture Check
malfunction has occurred
and moisture is present
• Evidence of moisture
•
Perform Moisture Check
present inside air mover
Do
Don’t
• Check out motor, controls,
•
Automatically assume the motor is bad.
wiring and connections
thoroughly before replacing
motor
• Orient connectors down so • Locate connectors above 7 and 4 o’clock
water can’t get in
positions
- Install “drip loops”
• Use authorized motor and • Replace one motor or control model # with
model #’s for replacement another (unless an authorized replacement)
• Keep static pressure to a
• Use high pressure drop filters some have
½"
minimum:
H20 drop!
- Recommend high
• Use restricted returns
efficiency, low static filters
- Recommend keeping filters
clean.
- Design ductwork for min.
static, max. comfort
- Look for and recommend
ductwork improvement,
where necessary
• Size the equipment wisely • Oversize system, then compensate with low
airflow
• Check orientation before
• Plug in power connector backwards
inserting motor connectors • Force plugs
Moisture Check
• Connectors are oriented “down” (or as recommended by equipment
manufacturer)
• Arrange harness with “drip loop” under motor
• Is condensate drain plugged?
• Check for low airflow (too much latent capacity)
• Check for undercharged condition
• Check and plug leaks in return ducts, cabinet
Comfort Check
• Check proper airflow settings
• Low static pressure for lowest noise
• Set low continuous-fan CFM
• Use humidistat and 2-speed cooling units
• Use zoning controls designed for ECM that regulate CFM
• Thermostat in bad location?
Содержание Q-TEC Q24H2D Series
Страница 6: ...Manual 2100 603 Page 6 of 44 FIGURE 1 UNIT DIMENSIONS Q24H2D Q60H2D Q30H2D Q36H2D Q42H2D Q48H2D...
Страница 9: ...Manual 2100 603 Page 9 of 44 FIGURE 6 DUCTED APPLICATION FIGURE 5 INSTALLATION WITH DUCT FREE PLENUM...
Страница 13: ...Manual 2100 603 Page 13 of 44 MIS 2469 DRAIN BOX WALL SLEEVE OVERFLOW TUBE CAULK AROUND TUBE FIGURE 12A...
Страница 15: ...Manual 2100 603 Page 15 of 44 REMOVE KNOCK OUT FOR INDOOR DRAIN HOSE CONNECTOR MIS 2471 FIGURE 12C If Used...
Страница 31: ...Manual 2100 603 Page 31 of 44 FIGURE 22 FRESH AIR DAMPER REMOVAL MOUNTING SCREW...